Rubber seals for military and defense? Military equipment operates under extreme conditions, demanding peak performance from every component. Rubber seals for military and defense play a critical role in ensuring this performance, safeguarding vital systems from harsh environments. The global military rubber seal market, reflecting this importance, is projected to grow at a robust Compound Annual Growth Rate (CAGR) of 5.2% by 2027.
In this article, we delve into the world of military rubber seals. We’ll explore the essential properties these seals must possess, the rigorous standards they need to meet, and the careful material selection process that goes into their creation. Ultimately, we’ll discover how these unassuming components contribute to the success of military operations around the globe.
If you are active in other domains you will also find useful Tehnoguma’s industrial rubber coverage in the mining industry, food production, ergonomics technologies, roller technologies, and more. Go till the end of the article so you become knowledgeable about rubber seals for military and defense.
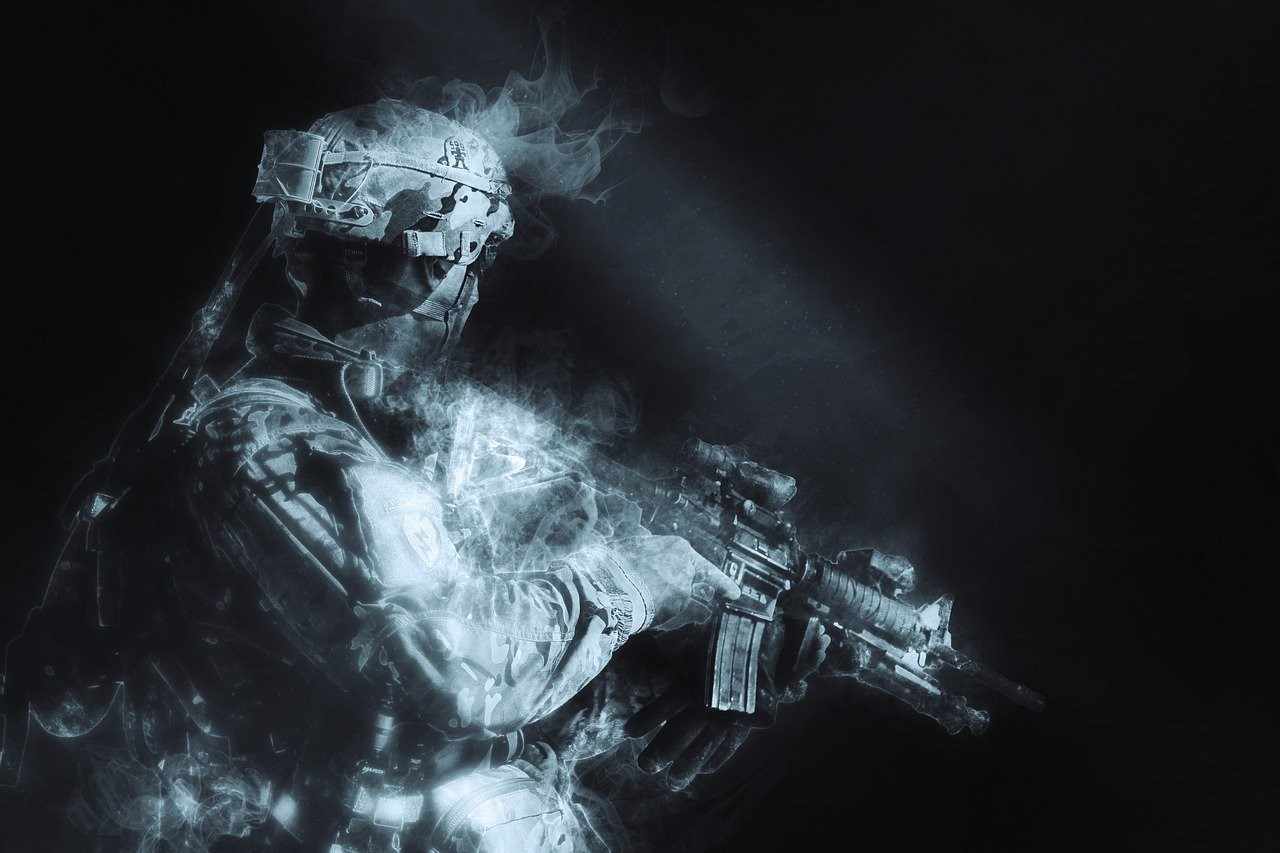
Understanding Rubber Seals For Military And Defense
Definition and Importance
Rubber seals are an essential part of military equipment, which has to work in very difficult environments – from extremely hot deserts to very cold icy places. These seals are usually rings or gaskets. They stop leaks and protect important inner parts by making a tight seal between two surfaces. This helps the machines to carry on working properly without breaking down. So we have the best solution – rubber seals for military and defense.
The Critical Role of Rubber Seals For Military And Defense
Rubber seals help military systems stay “well” so often that you hardly ever hear about them: they do their job quietly! Rubber seals do the same job across all sorts of military equipment: on land, under the sea, and in the air. Their flexibility means systems can work properly even when conditions are tough. Employing rubber seals for military and defense purposes allows for:
- Preventing Leaks: Military gear needs fluids such as fuel, coolant, and hydraulic oil to operate at peak efficiency. Rubber seals stop these fluids from leaking out and damaging system performance – for example by ensuring that water doesn’t get into the engine compartment of a tank crossing a river.
- Sealing Out Contaminants: ealing Against Contamination: Dust, dirt, and moisture can all interfere with the smooth operation of the sensitive electronics and machinery used in military equipment. Rubber seals provide a protective layer that keeps these contaminants out; if there’s an aircraft cockpit door with seals around it, they’ll stop debris or dust from affecting anything inside when controls need to be moved.
- Dampening Vibrations: Military hardware undergoes a lot of movement and vibration during use. Rubber seals help to reduce noise by absorbing some vibrations – but they also have an important role in protecting delicate equipment as well as making working conditions more comfortable for crew members (who will still be able to hear each other better if things are quieter).
Properties of Military-Grade Rubber Seals:
In military settings, there is no room for errors – everything must perform at its best all the time. Rubber seals used in such conditions need to have several important qualities:
- High Abrasion Resistance: Constant rubbing can quickly wear out an ordinary seal, but not one that’s been specially made to resist abrasion. For example, when a tank moves across rough ground, its seals must cope with lots of small knocks or scrapes if they’re to remain intact and prevent leaks;
- Superior Flexibility: they have to work well even when they are fitted onto slightly uneven surfaces or used as part of moving parts that alter shape slightly with temperature changes. Seals around hatches on ships are a good illustration – these metal openings may warp (slightly bend) as temperatures vary during ocean trips. To stop seawater from getting in, the flexible seals need to stay tightly compressed as if the hatches were still a perfect rectangle;
- Exceptional Tensile Strength: seals on hydraulic lines in planes need to be very strong so they can safely cope with the high pressures caused by movements inside the aircraft’s wings, wheels, etc.
- Impressive Chemical Resistance: Resistance to chemicals including petrol, oil, and other fluids they might come into contact with.
** Fact: Military-grade rubber seals are made to last in extreme temperatures. They hold up in a cold arctic environment of -60°F (- 15°C) as well as in blistering 400°F ( 200°C) deserts — so equipment keeps working perfectly whether it’s icy or hot.
Comparison Table: Rubber Seals Materials for Military and Defense
Military seals require different rubber types depending on the environment and use case. Here are some common materials with their properties:
Property | Nitrile Rubber | Fluorosilicone (FVMQ) | Fluoroelastomer (Viton) | EPDM |
Temperature Resistance | -40°F to 250°F | -60°F to 400°F | -40°F to 460°F | -60°F to 350°F |
Chemical Compatibility | Good for oils & greases | Excellent for fuels & oils | Excellent for fuels, oils, & harsh chemicals | Excellent for water & steam |
Abrasion Resistance | Good | Excellent | Excellent | Very Good |
The table above gives a rough guide only! In reality, there will be many other factors that need consideration before choosing which compound is best suited for any specific application such as mechanical properties, cost, and other technicalities and details. If you are willing to discover more read our previous publishing on Rubber Gasket Sealants: The Perfect Solution for Many Use Cases. And if you are in questions, it is best to consult our customer support and get informed beforehand.
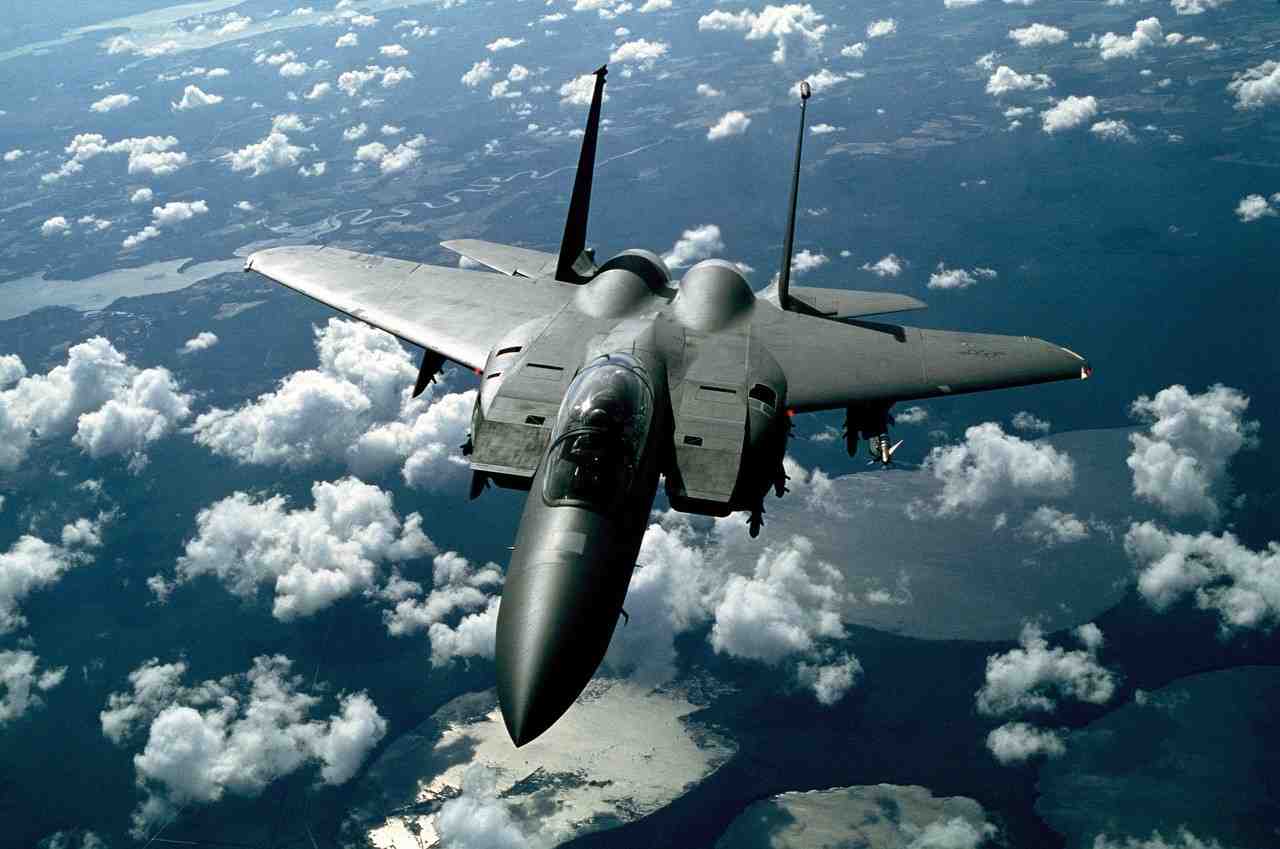
Standards Compliance of Rubber Seals for Military and Defense
In military operations, nothing can go wrong. Everything needs to be in line with rules – even small things like rubber seals! These seals may look basic but they are very important: military equipment must be safe and work properly all the time. That’s why there are strict checks on these parts.
Key Military Standards and Specifications:
- MIL-STD-810 (Environmental Engineering Considerations): Tests for Toughness Military seals have a tough life – as tests based on environmental standard MIL-STD-810 show. Such checks mimic what seals may face in places where armed forces operate such as:
- Extreme Temperatures: Seals have to work after being frozen and then burnt; dimensions are also checked so they don’t crack when temperatures change quickly (stat from Army Research Laboratory report 2021 notes kit can undergo temperature swings of 100°C-plus within 24 hours). Deserts get very hot in the daytime but cold at night so seals on vehicle engines need to cope with this.
- Humidity: Places with lots of warm wet air can make rubber seals deteriorate and stop them from sealing properly. Tests include long periods at up to 95% humidity (militaries may need this type of seal for jungle operations or crafts that go straight from water into use).
- Vibration and Shock: Things in military use get shaken and jolted a lot! Seals are checked to see if they stay in place (and continue to stop leaks) when machinery vibrates intensely or has sudden knocks. Military helicopters are capable of producing vibrations that go beyond 20 Gs. This shows why seals need to be made to take a lot of punishment.
- MIL-R-6855 (Rubber, Synthetic, Sheets, Strips, Molded or Extruded Shapes): If you want to get into the details, this is where you will find them: It tells you exactly what physical and chemical properties these tough rubbers have to have when they are used to make certain seals or gaskets for the military. Properties such as how much stretching they can take before breaking — tensile strength — how resistant they are to tearing, or whether they will swell up if they come into contact with a particular liquid.
Testing Procedures and Criteria for Compliance:
Ensuring compliance with these standards is quite challenging. Independent laboratories test the seals made by rubber seal manufacturers in many different ways. One part of this testing includes putting seals through various environmental conditions to see how well they hold up under set criteria. For example, after being subjected to extreme temperatures seals might need to work as normal – not leak – for a specific period if they are going to be approved under something called MIL-STD-810. If any seal does not pass all parts of any test there may be lots more tests still ahead before it can be used in military equipment — and those that do make it through everything will often be called “military grade.”
The Imperative of Standards Compliance:
The significance of abiding by military standards is immense – and here is why:
- Mission Success: When it comes to rubber seals, for example, making sure they meet all necessary criteria is crucial if our forces are going to achieve their objectives without any problems. If these seals don’t comply with regulations they can crack under pressure. This may cause fluids and vital pieces of equipment to leak meaning they won’t work properly – or at all. In turn, this could put missions at risk: imagine a fighter jet having a hydraulic fluid leak from a faulty seal; there could be a terrible crash crew might be killed or injured.
- Safety of Personnel: Then there is the human aspect. Because service personnel often operate in environments with dangerous fuels explosives compliance is again vital otherwise seals on things like fuel lines fail there could be serious accidents; people could even die.
- Equipment Longevity and Cost Savings: Equipment doesn’t come cheap and if seals aren’t up to scratch there could also be financial implications further down the line: kits designed to last longer while those meeting required standards should need less maintenance than those don’t will have to be replaced more frequently — this means either greater spending operational costs or both.
Enhanced Durability Through Standards Compliance
Extreme heat in deserts was wrecking military vehicles’ rubber seals prematurely, making them degrade and fail. So the top manufacturer set up tough tests to check their seals could cut it with the very hardest conditions – as laid down by MIL-STD-810. The seals they came up with were made from advanced materials that had undergone a huge amount of testing for heat resistance. When used, these new seals lasted 40% longer than the old ones – meaning fewer needed to be fitted overall. As a result, tanks, etc. didn’t break down so often (or at least not because of seal problems) and troops were better able to do what was being asked of them at any given moment: enhanced mission readiness.
The requirements for rubber seals within the military are far more than just bureaucratic obstacles. They are critical protective measures that need to be met so that missions can be completed successfully while keeping personnel safe and equipment operational for as long as possible. By sticking with these standards – and making use of cutting-edge materials – companies can be sure that although small and often overlooked, seals will carry on doing their jobs wherever needed to such an extent that military activities around the world can continue apace.
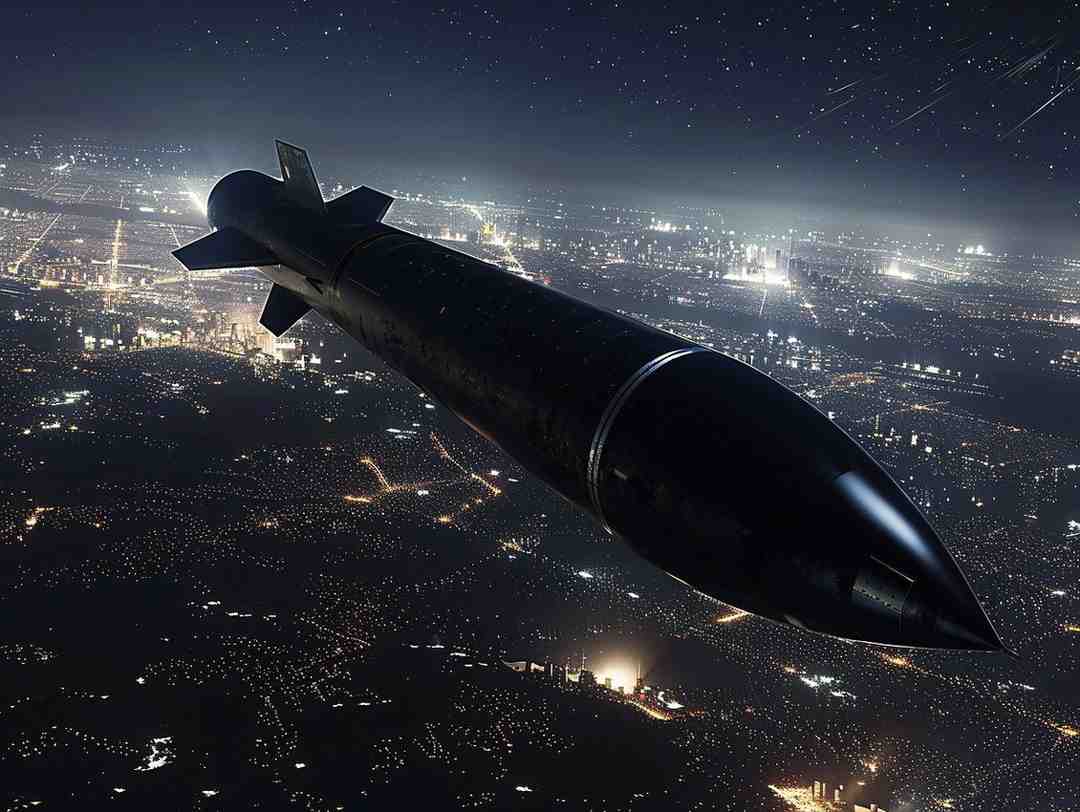
Enhancing Durability and Performance: Advanced Rubber Seals For Military And Defense
Tough jobs need tough materials – for longer life and better performance in military applications, advances in both choice of material and compound design are being constantly sought.
Advanced Material Selection: A Spectrum of Benefits
Not all rubber seals are suitable for every job. To achieve top results whilst in service (and to reduce maintenance needs), those working in Defence have options that offer benefits such as:- Improved resistance to environmental factors and extended operational life The following overview explains more about some types of advanced materials along with reasons why they are selected for particular tasks:
- Fluorocarbon (Viton): Fluorocarbon, also known as Viton, is a top-of-the-line material with many outstanding qualities:
- Temperature Resistance: Withstanding temperatures between -40°F and 460°F, Viton seals can be used in frigid cold or scorching heat — making them perfect for all kinds of climates.
- Chemical Compatibility: In military operations where performance counts most (such as those involving fuels, oils, or harsh chemicals), Viton seals are unbeatable.
- Durability: Viton seals last a long time even under tough conditions.
- Silicone: Silicone also has multiple benefits:
- Temperature Resistance: Silicone seals work well from 400°F to -60°F.
- Flexibility: If you need something that will make a tight seal even on uneven surfaces (or move around a lot as it opens/closes), Silicone might be your best option.
- Chemical Resistance: Silicone offers good resistance to many oils and some chemicals.
- EPDM (Ethylene Propylene Diene Monomer): EPDM (short for Ethylene Propylene Diene Monomer) shares several advantages of its own:
- Temperature Resistance: Seals made from EPDM can perform between -60°F and 350°F. That makes them useful in many military applications.
- Chemical Resistance: Able to resist water as well as steam; works fine with lots of polar fluids.
- Cost-Effectiveness: sometimes — when compared to more advanced materials EPDM offers a more economical option.
Comparison Chart: Viton vs. Silicone vs. EPDM
Property | Viton (Fluorocarbon) | Silicone | EPDM |
Temperature Resistance | -40°F to 460°F | -60°F to 400°F | -60°F to 350°F |
Chemical Compatibility | Excellent (fuels, oils, harsh chemicals) | Good (oils, some chemicals) | Excellent (water, steam, polar fluids) |
Durability | Excellent | Very Good | Good |
Flexibility | Moderate | Excellent | Good |
Cost | High | Moderate | Low |
Improved Wear and Abrasion Resistance: Lasting Performance
Military equipment faces continuous friction and wear. In tough conditions like these, regular rubber seals may fail early and start leaking. Advanced rubber compounds tackle this problem in two main ways:
- Reinforcing fillers: They can include special fillers such as aramid fibers which boost tear and abrasion resistance a lot – meaning seals last much longer. (According to technical information, studies have proven that seals made from advanced rubber with extra fillers can last up to 50% more time under extreme conditions like constant contact with sand and grit.)
- Special additives: Some compounds have extra ingredients like those found in lubricants; this lets moving parts work together more easily so they don’t wear out as quickly.
Chemical and Environmental Resistance: Unfazed by Harsh Conditions
Military equipment operates in many different environments, from hot deserts to salty oceans. Rubber seals must be able to resist exposure to lots of different harsh substances. Here is some more information:
- Chemical Resistance: Military seals come into contact with all sorts of fuels, oils, fluids, and chemicals used to remove ice. Scientists have developed special materials that can withstand these chemicals so seals do not break down or let leaks start. Rubber seals in military applications need to resist chemicals with a wide pH range. They may be exposed to very acidic substances with a pH as low as 2, as well as highly alkaline ones with a pH as high as 12.
- Environmental Resistance: Being near the sea can also affect rubber seals; sunlight, ozone, and temperature changes can damage them over time if they are not specially protected. Environmental resistance: Rubber seals near the sea can be damaged by sunlight, ozone, and temperature changes. Special additives help protect seals from these factors and extend their life. UV stands for ultraviolet. Some words have been changed in this version.
Manufacturers are using new materials and innovative formulas to make rubber seals that go beyond current limits for how long they last and what conditions they can withstand. These advances are important because military gear needs to work well for a long time in all kinds of situations—it can’t break down or wear out quickly if serious problems are to be avoided. The wide application of rubbers seas allows them to be a perfect fit in many industries. If interested additionally, read more on Gaskets and Seals: The Silent Sentinels In Food Production.
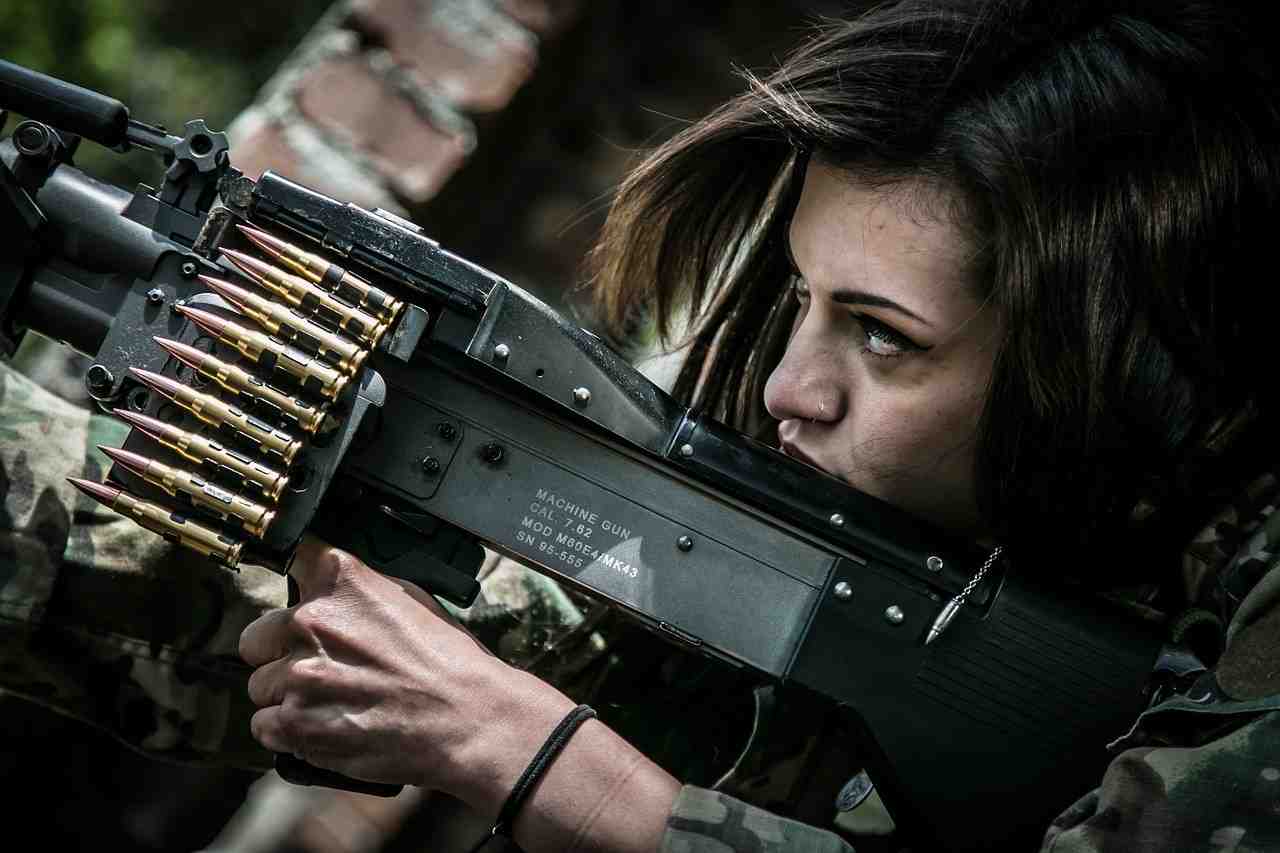
Material Customization for Specific Military Applications
Military gear has to work wherever it’s needed — and that includes specialized rubber seals. These need to be made from advanced materials specially chosen for each job if they’re going to perform at their best possible standard.
Customization for Specific Applications: Seals Built for Purpose
Tailoring seals for particular purposes Rubber seals used by the military aren’t like the ones you’d pick up at a hardware store — mass-produced parts are good enough in most situations. Instead, they’re individually designed so they can do exactly what’s needed in one specific role or piece of equipment. Here few examples of customization:
- Submarine Hatches: Consider the immense pressure placed on a seal for a submarine hatch when it dives deep below the ocean surface. To ensure crew safety, it is vitally important that seals used in such applications are custom-manufactured from special blends of silicone or fluorocarbon (Viton). These materials need to have very high compressive strength so they can withstand the enormous water pressure pushing against them; they also need low permeability (the ability of a substance to allow another substance to pass through it) to remain watertight.
- Aircraft Engine Seals: Aircraft engines produce power under extreme conditions. Custom seals made specially for these engines may be composed of compounds which include fluorosilicone (FVMQ) that can cope with both high temperatures and chemicals found in aviation fuels. The seals must not leak oil either as this could affect an engine’s performance; neither must they become damaged by regular contact with fuel.
- Ground Vehicle Suspension Systems: Military vehicles often travel over rough terrain, which can be very tough on their suspension systems. A good way to protect these systems is by using specially-made seals. These might be created using EPDM or nitrile rubber mixed with extra-strong fillers. Such materials are highly resistant to abrasion – the wearing away caused by friction – and can cope with being stretched and torn; they also allow for demanding movements typical of a suspension system. As a result, components last longer (meaning lifespans are increased) and performance levels stay high: valuable characteristics for those in the armed forces.
Innovation Under Pressure
One of the top producers of submarines had trouble keeping their hatches watertight when going deep below the ocean surface. The rubber seals they usually used were not up to the job at hand – there was too much pressure for them. To solve this problem, the company joined forces with a specialist developer of rubber compounds. Working together, they came up with an entirely new type of seal made from a mix of Viton (a type of fluorocarbon) and an unusual solid filler material. Tests showed that this groundbreaking stuff withstands 30 % more squeezing force before it starts to break down compared with seals currently available. When fitted to the manufacturer’s hatches, the new seals did exactly what they were supposed to do: no water came in. As well as making subs safer for crew members, it also meant savings because vessels did not have to surface so frequently for checks.
Integration with Military Equipment: The Unsung Heroes of Performance
Rubber seals do more than just block things – they are a vital part of how well military gear works. Take these instances for instance:
- Missile Systems: Missiles need to be guided and controlled by electronics. But these systems can’t have interference from other electronic equipment. One way the US Army has solved this problem is by using silicone seals with great dielectric properties. These seals stop electromagnetic signals from messing up the guidance system, which means the missile goes where it’s meant to –- and does the job it was designed for.
- Communication Equipment: When soldiers are out in the field (a battle scenario) communicating with each other or their base is crucial. Electronic systems can be damaged by moisture (wet conditions). To prevent this from happening special rubber seals made from EPDM are used to form protective barriers around sensitive parts of the communication equipment — keeping everything dry so that it all keeps working perfectly.
- Weapon Systems: Guns and ammunition launchers also rely on hi-tech electronics nowadays. The last place you’d want those sophisticated gadgets to get wet is while they’re being fired! So the US military uses specially designed rubber seals when manufacturing these items as well. A type of nitrile rubber seal that has proved to be incredibly tough (resistant to damage) even when lots of heat and pressure are produced as bullets or shells are shot.
By choosing different materials and designs engineers can make sure seals do everything needed them without causing problems of their own. And because they are often made to order there are no end products meaningless! Their wide usage is also shown in science. Read more about Rubber Gaskets: Fluid Handling Excellence in Science Labs.
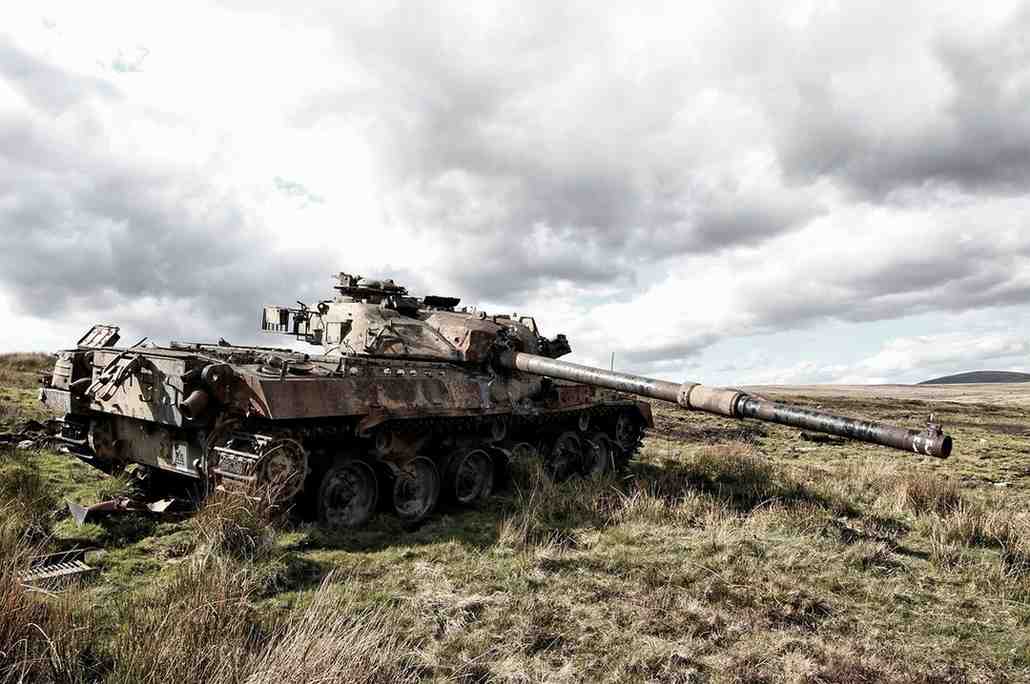
Powering Performance and Efficiency with Advanced Rubber Seals For Military and Defense
The advantages of the theory of using advanced rubber seals turn out to make a real difference on the ground – as two different examples from military usage show well. Getting more out of planes: US Navy’s F-18 fighter jets.
Taking Flight with Enhanced Efficiency – F-18 Fighter Jets
Challenge: The hydraulic system seals of the F-18 fighter jet, which is widely used by the US Air Force, posed a problem. Because regular seals wore out too quickly under tough flight conditions, there were often leaks – and the plane had to be grounded for maintenance. This meant it was not as effective as it could be, and looking after both the sealing system and fixing any leaks cost extra cash.
Solution: But help was at hand from an unexpected quarter: a collaboration between America’s air chiefs and a major aerospace firm has come up with an answer. Instead of fitting standard rubber seals that do not last very long, why not use some specially developed high-performance ones instead? After carrying out successful trials using fluoro silicone (FVMQ) compounds the team found these custom-made components did the trick. Tolerating extremes … that was just one benefit of the advanced material; resisting chemicals was another plus point along with being tough when constantly rubbed against!
Results: Results have been impressive too once they made the switch from the boring old type to the fancy new kind efficiency went up by 35 %. With more flying hours possible per aircraft, this means readiness levels have also improved greatly – so there are savings all around on maintenance bills thanks largely.
Impact: The advantages of swapping usual rubber seals for those made using hi-tech stuff are plain to see when one looks at how fine-tuning their use has boosted battle-readiness while simultaneously cutting costs across the entire fleet- something which has far-reaching implications beyond purely monetary matters if you stop think about it for more than few seconds.
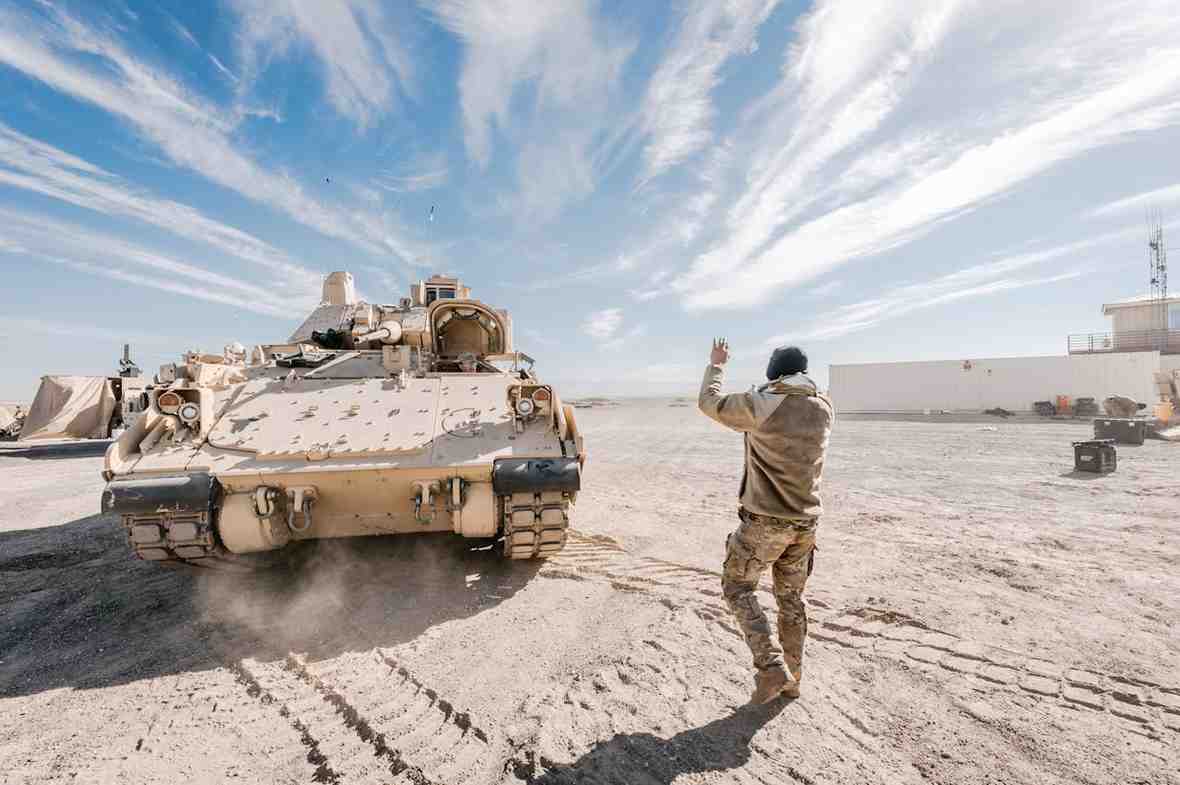
Riding the Waves with Reliable Seals – Nimitz-Class Aircraft Carrier
Challenge: Deterioration of rubber seals on watertight doors caused leaks in compartments of Nimitz-class aircraft carriers because the material couldn’t stand up to constant exposure to saltwater or harsh weather.
Solution: Working with a company that makes special seals, the Navy came up with new ones specially designed for these doors — using both EPDM plus nitrile rubber instead of just standard stuff (which didn’t work). These two materials combined well together and offered.
-
Chemical Resistance: By using EPDM, our seals were able to withstand saltwater-related degradation.
-
Durability: Nitrile rubber made the seals more resistant to abrasions and tears; they could therefore cope with the tough conditions of watertight door operation.
-
Watertight Integrity: The materials’ combined properties also guaranteed water-tightness — so compartments stayed dry and sailors remained safe!
Results: The new seals had some great results.
-
Enhanced Seal Durability: the watertight door seals lasted 30% longer with them – so we didn’t have to replace them as often or spend as much time maintaining them.
-
Reduced System Failures: We also had fewer system failures caused by water leaks by 15%. This means that there were more days when all systems worked perfectly; it also made each aircraft carrier safer overall.
Impact: In fact, these findings show how important such sealants are when it comes to protecting important ships like Nimitz-class aircraft carriers. When these seals do their job well … then not only does their presence help ensure things stay dry where they’re supposed to be (for instance: inside a ship’s components), but also contributes towards other factors like crew safety plus whether missions can be completed successfully or not! (Essentially: don’t underestimate the value provided by a tiny piece of rubber).
The case studies demonstrate that advanced rubber seals do more than just sit there – they’re crucial to boosting performance, making machinery more efficient, and keeping costs down in military settings. Thanks to clever material advances and careful planning, engineers can keep using these undervalued little lifesavers to protect soldiers and help things work smoothly worldwide.
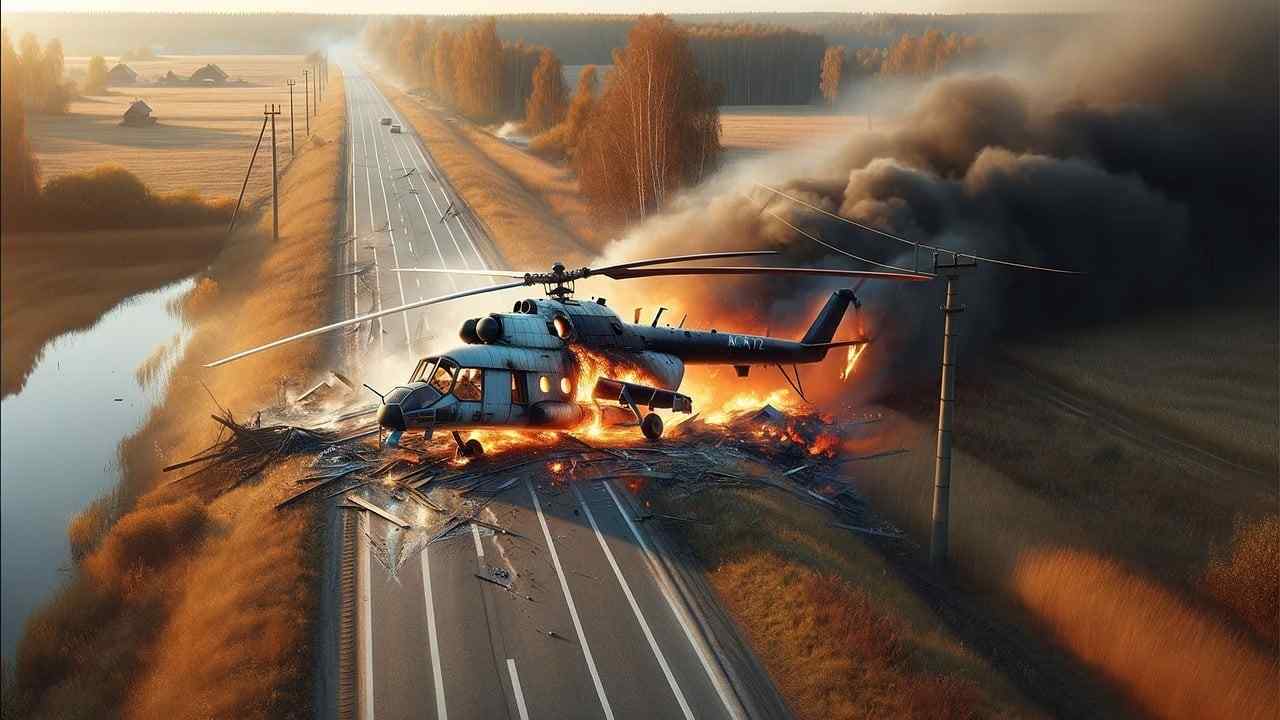
Conclusion
From burning hot deserts to cold arctic wastelands, military gear operates at the very limits of what is physically possible. And there’s one humble item that makes sure it does so reliably – the rubber seal. Rubber seal for military and defense proved extremely efficient.
The piece took a look at hi-tech rubber seals: what they have to put up with, and how they’re designed and made so they can cope with it. We learned that because these seals are made from advanced materials and tailored to do a specific job, they can work even if it gets extremely hot or cold, or they come into contact with harsh chemicals all the time.
Examples were given to show how using high-spec seals doesn’t just help equipment to work better (in the case of F-18 fighter planes); they also stop it from breaking down too often (like onboard Nimitz-class aircraft carriers).
In short, advanced rubber seals are no ordinary O-rings. They’re essential for making sure the kit does what it’s meant to when it matters; not surprisingly, therefore, they need to pass lots of tests before being allowed near a battlefield. So here’s to these unsung heroes: long may they help keep military missions on track – worldwide!
Still have a plethora of unanswered questions. Get the best offer and answers by directly contacting our customer support.