At the core of every mining venture that runs smoothly is the ability to screen well. It is essential to separate materials that are valuable from those that are not if you want to make as much money as possible. With so many rubber screens available, selecting the right one can seem like a huge job. But there’s no need to worry: this article has got your back! We are going to take you through everything you need to know about rubber screens so that when it comes time to pick one out, there will be nothing daunting about the task. We will discuss various key points like opening sizes and wire widths, materials used in construction, and different aperture shapes–all with one goal in mind: increasing efficiency while also reducing any downtime costs (and therefore boosting profits). Just think of us at Tehnoguma as being by your side throughout this process; after all, we have years of experience providing industrial solutions with our high-quality rubber products.
Rubber screens find applications in multiple industries: the mining industry, food production, ergonomics technologies, roller technologies, the automotive industry, and more. Let’s now see how to choose the right one for peak performance.
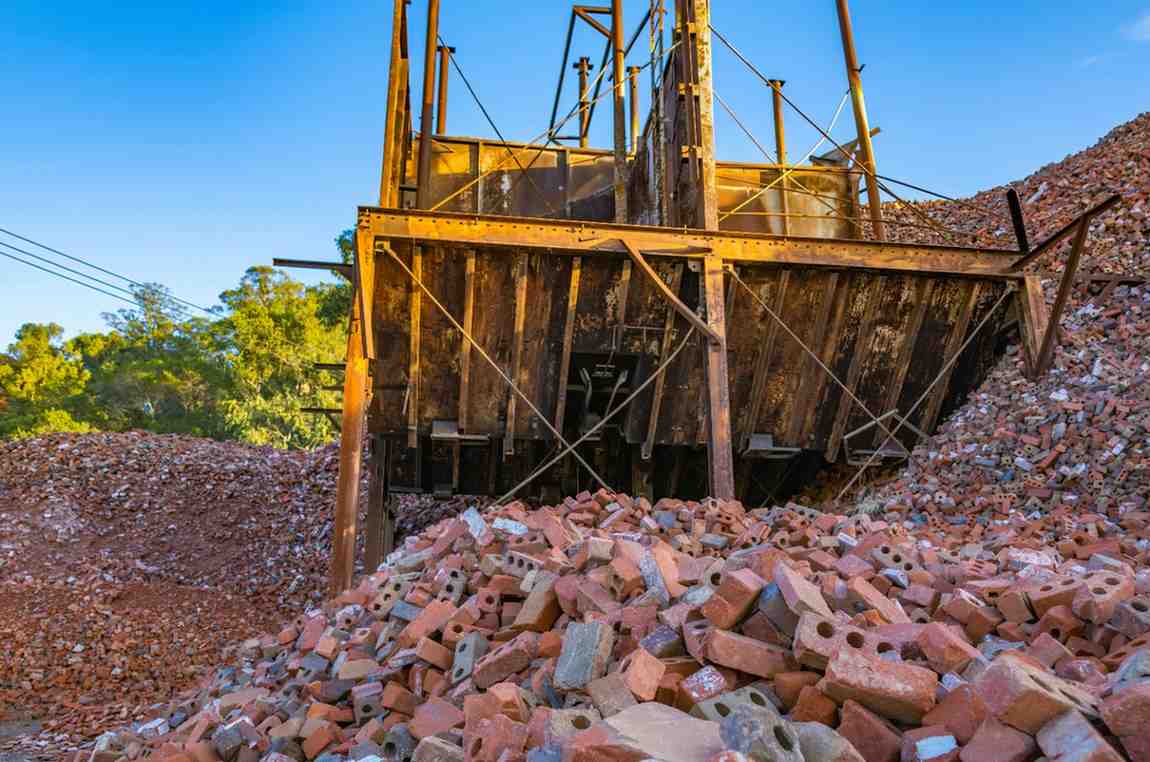
The Inner Workings of Mining Screens Revealed: A Functional Analysis
Mining screens, also called screening media, are essential components in the operation of any productive site. These screens carry out a range of tasks that are crucial to efficiency–separating material by size alone brings benefits such as increased yield and greater profitability. But before you can choose which screen is right for your job, why not get to know them a little better? Below we’ll take apart these hard workers so their secrets are revealed; we’ll also identify what different bits do.
- Function: If you’ve ever seen a really big sieve then it’s easy to understand what rubber screens do. They allow particles smaller than the gaps between individual sections to drop through (these are known as undersized materials) but retain anything larger on top (oversized ones). This separation process is vital when you need to classify mined materials or extract wanted fractions only.
- Components: Rubber screens usually are made from tough, robust types of elastomer that wear well like synthetic or natural rubbers. They have several important elements including:
- High-Tensile Wires: These form a screen’s basic structure and provide apertures with their strength plus define its size too. Wire diameter (which might also be called gauge) is an important factor affecting performance: bars supporting sieves loads thicker can cope with more weight but let less material through holes of their own.
- Openings (Apertures): The spaces between wires do jobs letting undersized particles pass. Aperture size – that is width between one wire and the next – must be considered carefully if materials are to be separated correctly. Think about your kitchen sieve: should holes be small only tiny things like couscous would get through them!
- Aperture Shape: As well as considering dimensions manufacturers think a lot about whether shape could make a difference in efficiency. Materials people mine behave in a certain way when they know how it behaves shaped accordingly helps flow this may mean gainfully employed. Popular options include square apertures that have oblong Bananas curved sides – each has its own merits depending upon the application type minerals being worked.
The initial step in choosing the best rubber screen for your mining needs is to comprehend how different parts affect screening. Once you understand these dynamics, you can select a screen that will make your operation more efficient and ultimately more profitable.
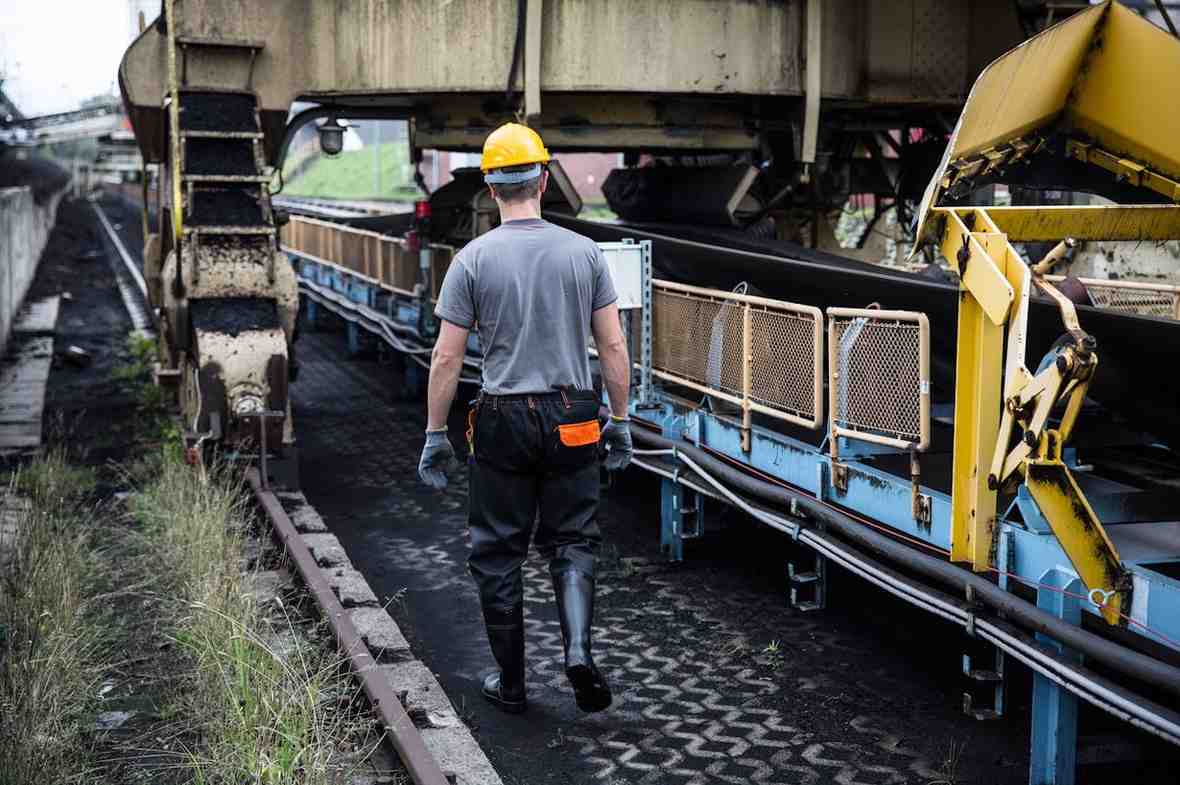
Choosing the Best Rubber Screen for Optimal Performance: Why One Size Doesn’t Always Fit All
To get the most out of your mining operation, you need more than just any rubber screen – you need one tailored to your specific requirements. Here are some key points to consider:
- Tailoring Your Approach – Application specifics: What exactly do you need your screen to do? This will determine its size and shape. eg Scalping screens have to cope with big rocks so they need to be pretty robust: openings of 100mm (4in) plus wires 5mm (1/5in) thick. If you’re separating smaller particles for further processing; then you’ll want something different again!
- A dewatering screen: is a scalper that also allows water to drain out for final grading: these may have very fine apertures and usually slimline rubber. Special features on dewatering equipment might include raised edges to help prevent the ‘pooling’ of liquid at the end of the process area.
- Material specifics: Some quarried products wear out rubber VERY fast indeed eg. granite and industrial sand. There are various compounds available that address this issue whilst still giving producers good output capability from screening plants. Besides abrasion resistance, potential users should also think about flex-crack properties but all reputable firms will provide detailed tech data on request.
However, the particular rubber compound utilized in the construction of the screen may also play a role. Some compounds perform better in damp conditions which means the screen does not degrade as quickly, and it separates objects efficiently for longer periods.
When operating the equipment you need to think about:
How fast materials are put on it, and vibrations from use. If lots are being processed, then a screen with more holes that allow things to pass through (but don’t break up) might be needed—especially if there is also shaking! A solution could be using thicker wires or making them in a way they don’t move as much because of their design elements; both will help products wear out less often but still do what they’re supposed to when shaken lots during operation. By thinking carefully about these things together – why the equipment is needed, what it’s made from/how this type works best under certain conditions & now also considering how often the parts should wear out due only to usage patterns or shaking alone – one can choose an ideal rubber-screens you have considered, application, material properties, and operational considerations, you’ll be able to select rubber screens tailored perfectly for your mining operation. These screens will help make sure that you’re working more productively as they will be efficient at screening things whilst also cutting down any time when replacements are needed.
Downtime can cost money so if there is less of it with these types then over a year there should be higher profits after costs are deducted for everyday use like power to run machines!
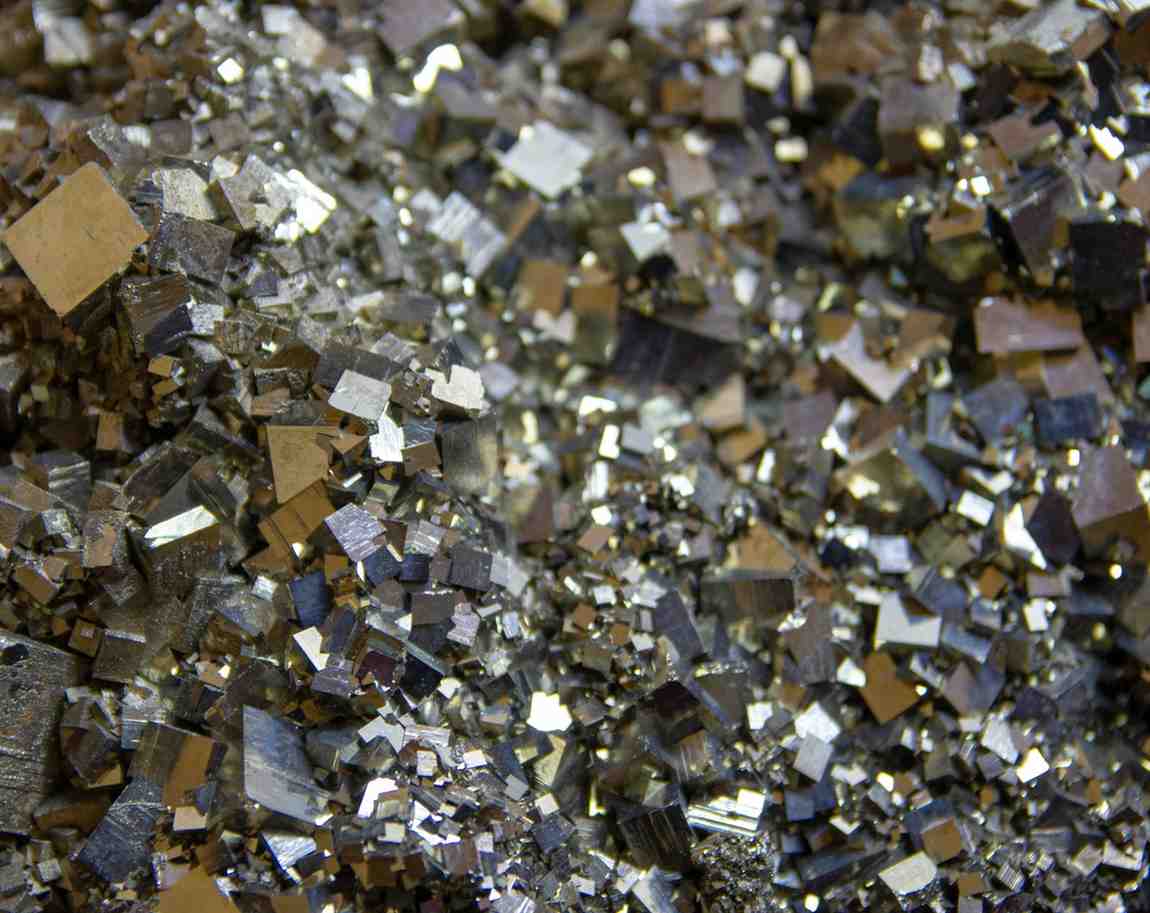
Going Above and Beyond the Basics in Screen Selection Optimization
Building upon the foundational elements of optimal screen selection discussed earlier, there are further factors to bear in mind that can help you hone your choice.
- Temperature Resistance: Not all materials are made equal – for example, some mining operations deal with extremely hot materials. If this applies to you, make sure that any rubber screen you are considering can cope with operating temperatures without its performance degrading over time. Tehnoguma produces heat-resistant rubber screens specially designed to be used in environments where temperatures are high; opting for these products will not only ensure that each screen lasts longer but also deliver better overall results.
- Chemical Compatibility: When a material stream contains chemicals, it is essential to choose a screen whose chemical-resistance properties match the substances going through it. Failure to do this can result in screens wearing out more quickly (degrading) or becoming damaged – both scenarios bring with them costs via reduced efficiency and/or downtime. If you know exactly what chemicals are present, selecting suitable screen(s) becomes easier.
- Environmental Regulations: There may be dust-control rules that apply because of where you are carrying out work. If so, choosing a screen with dust-suppression features such as special surface textures or an integrated spray system could be beneficial. These sorts of characteristics limit the amount of dust produced when materials are separated by screens; using them means you’re more likely to comply with regulations meant to safeguard employees’ health at the same time as looking after the planet.
- Cost-Effectiveness: Although it’s always important not to pay over the odds initially, bear in mind that cheapness does not necessarily equal value for money! A durable screen that lasts a long time might well work out cheaper in the end than several cheaper options which wear out more quickly – especially when other factors like maintenance and wear resistance are taken into account.
- Talking to the Experts: If in doubt, talk to firms who have been supplying screening media for many years. At Tehnoguma we have lots of advice based on practical experience; please get in touch!
- Our expert team offers the following: A comprehensive analysis of your needs to find the best solution. Custom screen recommendations are based on how your materials behave and what you need the screens to do for you.
Advise from people who know a lot about getting more efficient screening and less downtime. If you factor in these extra things and work with a supplier that knows their stuff, you can be sure that the rubber screens selected will deliver top results–increasing profits overall!
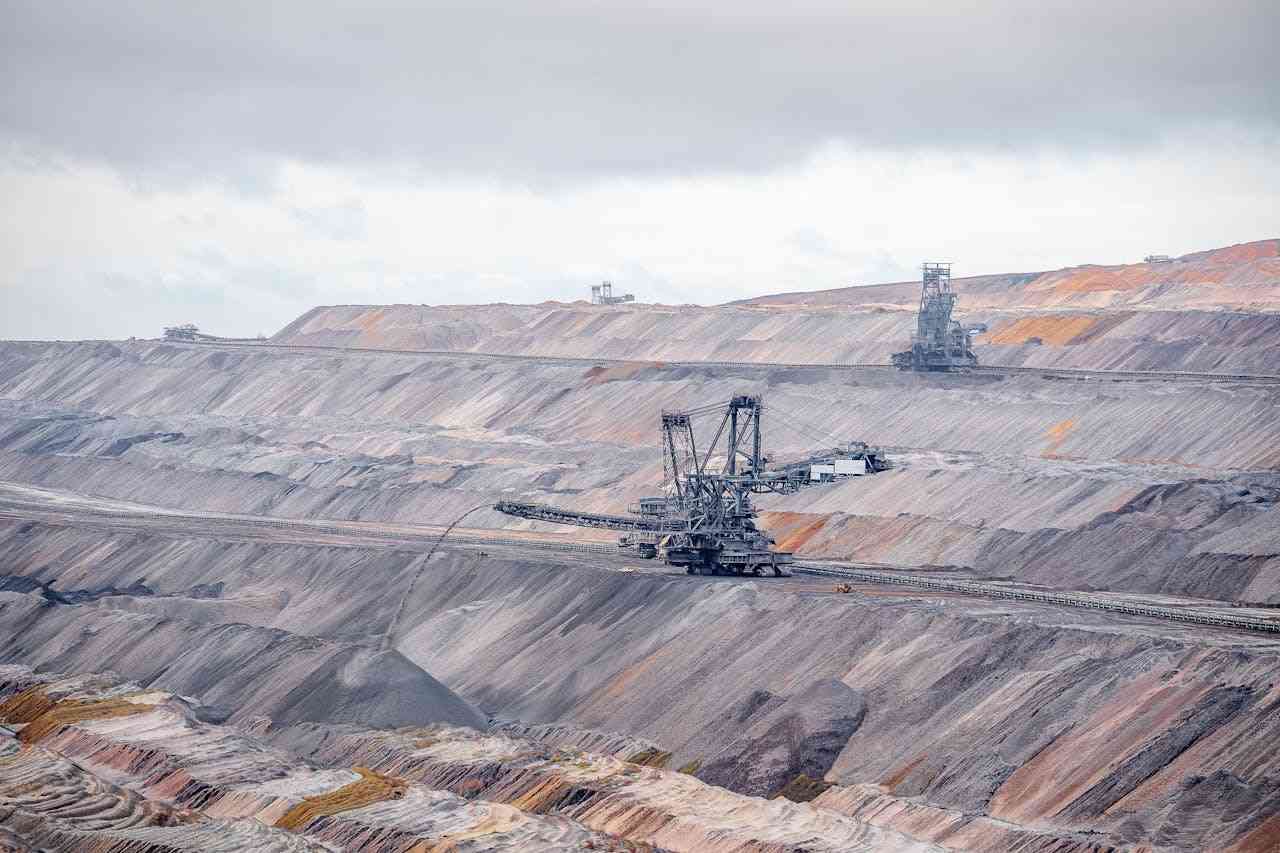
Tehnoguma – All You Need for Top Mining Screen Performance
Tehnoguma recognizes how important screening media is for getting your mining site running at peak efficiency–and we’ve got everything you need to make sure nothing holds you back. Our range of high-quality rubber screens is designed for outstanding performance in all conditions; let our team help you choose the best ones for your job, taking into account factors we’ve discussed plus more. What makes Tehnoguma different:
- Rubber Screens for every purpose: Whether you need to scalp rock, separate ore, or deal with water in the sand, Tehnoguma has it covered. We offer screens with different-sized holes and patterns so the material is processed more efficiently.
- Made from special materials: Rubber compounds used by Tehnoguma are formulated for tough mining conditions. Choose from resistance to abrasion, heat, and chemicals – or a combination that matches the rock or minerals being worked.
- Products designed especially for you: When standard screen designs won’t do the job effectively, speak to us. We can make something just for your site that fits machines perfectly and works better/lasts longer than shop-bought options.
- Long-lasting with less downtime: Don’t spend hours changing screens when you could be processing materials. Tehnoguma products are made well and undergo rigorous testing. They last longer on average than those bought elsewhere meaning fewer stoppages for replacement parts.
Don’t accept anything besides peak performance when screening! Contact Tehnoguma now. Our team will help find the best rubber screen solution for your mining needs. This means we can help you be more efficient and lower costs — so you make more money in the end.
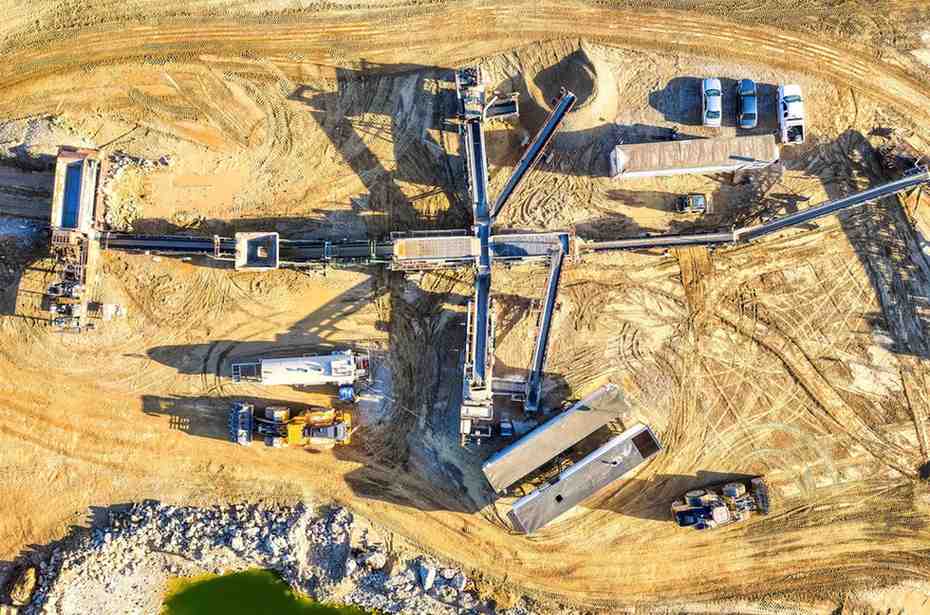
Conclusion
Don’t accept anything besides peak performance when screening! Don’t hesitate anymore contact Tehnoguma now and get what you deserve. Our team will help find the best rubber screen solution for your mining needs. This means we can help you be more efficient and lower costs – so you make more money in the end.
To get into details reach out to our customer support experts and discover today what will be the best fit for you. Don’t forget to stay tuned to our publishings in the news section on industrial rubber and stay up to date on the latest advancements, discoveries, and standards. You are still hesitant if we can respond to your needs? go through our market and service section to explore our more than 50 years of successful operation for various markets.