Why and how are rubber compounds important? Were you aware that the market for conveyor belts is rapidly increasing and is expected to be worth an incredible $5.39 billion by 2027? One of the main reasons for this growth is down to new uses of materials – particularly advanced rubber compounds.
These groundbreaking substances are changing these belts’ performance levels and their ability to withstand wear when used in tough industrial settings. In short: This piece looks at some of the amazing things advanced rubber compounds can do for conveyor belts!
We will examine what makes these specially designed materials so effective; how they make belts last longer and perform better–and how using them is improving operations involving handling materials across many sectors. During our discussion, we will identify key features of advanced rubber compounds–for example, their strength when pulled, resistance to wear from abrasives, and flexibility.
We’ll explain how these benefits mean belts made with such compounds can carry heavier loads, need less frequent repairs, and last longer: plus do other things too! If you want to know how advances in rubber technology could help your business move forward take a good look through what we have written here today!
Tehnoguma’s industrial rubber facility – supplies industries such as the mining industry, food production, ergonomics technologies, roller technologies, and more. Patiently read till the end of this article and get to know each aspect of rubber compounding for conveyor belts.
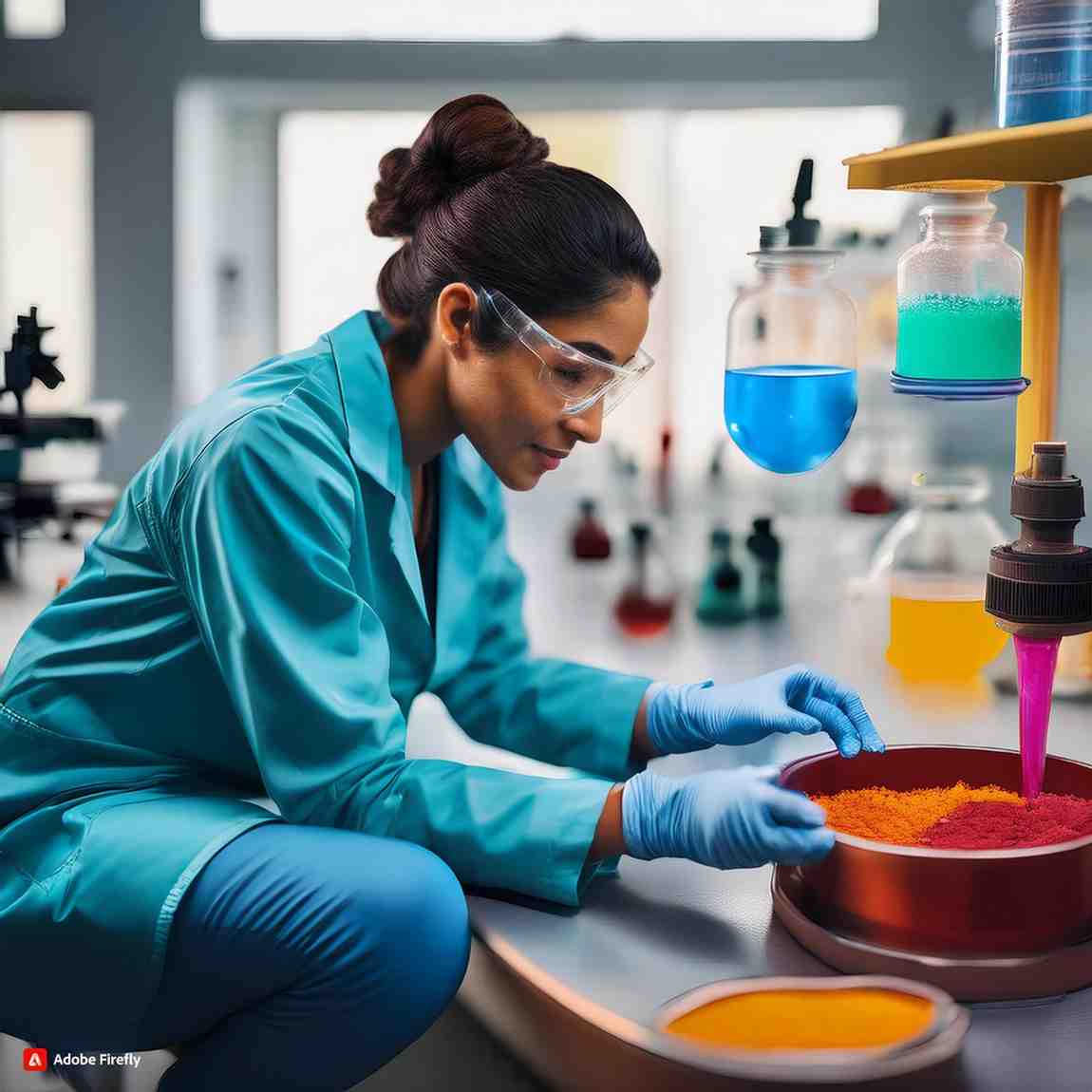
Understanding Rubber Compounds: The Backbone of Conveyor Belts
The Foundation of Strength: In many industries, conveyor belts do a lot of the heavy lifting by moving all sorts of materials along their paths. But at the core of these belts, there is an essential building block–rubber compounds. We’re not talking about any old rubber here though. Advanced rubber compounds are specially designed mixtures that are made with great care so they can provide the strength, flexibility, and durability needed to cope with tough modern industrial jobs.
Why It Matters Whether Your Rubber Is Advanced Or Not?
While basic rubber compounds get the job done, they often struggle to perform in today’s challenging settings. This is where advanced compounds come in. By being better all-rounders than their traditional counterparts, they meet this head-on; there must be a reason why superior is used across the board!For instance take durability as an example — because they have impressive resistance to wear and tear, conveyer belts last longer when made using these advanced compounds. (In case you were wondering-yes costs do end up being lower overall too since the belts need to be replaced less frequently.)
The Power of Four
Exploring the main features that distinguish advanced rubber compounds:
- Abrasion Resistance: It is well known that advanced compounds outperform others in their ability to withstand the scuffing and scraping that all materials undergo. This quality is essential for conveyor belts that are constantly coming into contact with abrasive materials such as rocks, minerals, or even heavy equipment.
- Flexibility with Strength: A material must be flexible enough to bend around rollers and corners without splitting if it is to be used as a conveyor belt.
- Balance: Advanced compounds have this balance between flexibility and tensile (pulling) strength – indeed they can improve an object’s tensile strength by up to 30 percent compared with regular rubber. This also means the belts can carry heavier loads without losing performance.
- Chemical Resistance: Conveyor belts may come into contact with many different chemicals in areas where things are being made. Again, advanced compounds do an excellent job here too; they resist oils, greases, and solvents very well (and also keep on working when submerged in these substances).
An Overview of Two Materials
This is a general comparison between the two material approaches:
Property | Advanced Rubber Compounds | Traditional Rubber Compounds |
Abrasion Resistance | Excellent | Good |
Flexibility | Excellent | Moderate |
Tensile Strength | High (Increased by up to 30%) | Moderate |
Chemical Resistance | Excellent | Good (May degrade with exposure to certain chemicals) |
A World of Rubber Options
The realm of rubber options for conveyor belts is vast – one type does not fit all! Below are some details about the different varieties you may encounter:
- Natural rubber: Good flexibility and elasticity are its hallmarks. It is often used in applications where there is a lot of call for high resilience to impacts.
- Synthetic rubber: If you need a material that will resist abrasions well and also stand up to chemicals, look no further than synthetic rubber. It is perfect for tough conditions. Synthetic rubber does not do as well in applications requiring elasticity
- Specialty blends: By taking the best qualities of natural and synthetic rubber chemists have been able to create compounds with tailored capabilities. This means conveyor belts can be made for specific industries or uses by blending chemicals. Other examples include belts that work well in high-heat or fire-resistant environments.
By adjusting how they make these materials, it is possible to get properties that suit particular industries exceptionally well. For example, some blends can cope with high temperatures making them useful for things like oven gloves or firefighters’ uniforms. These advanced rubber compounds are changing the way we make conveyor belts. Next, you can learn more about Rubber Compounding: The Science in Mining Equipment. Using them can help your industry — not just because belts last longer either!
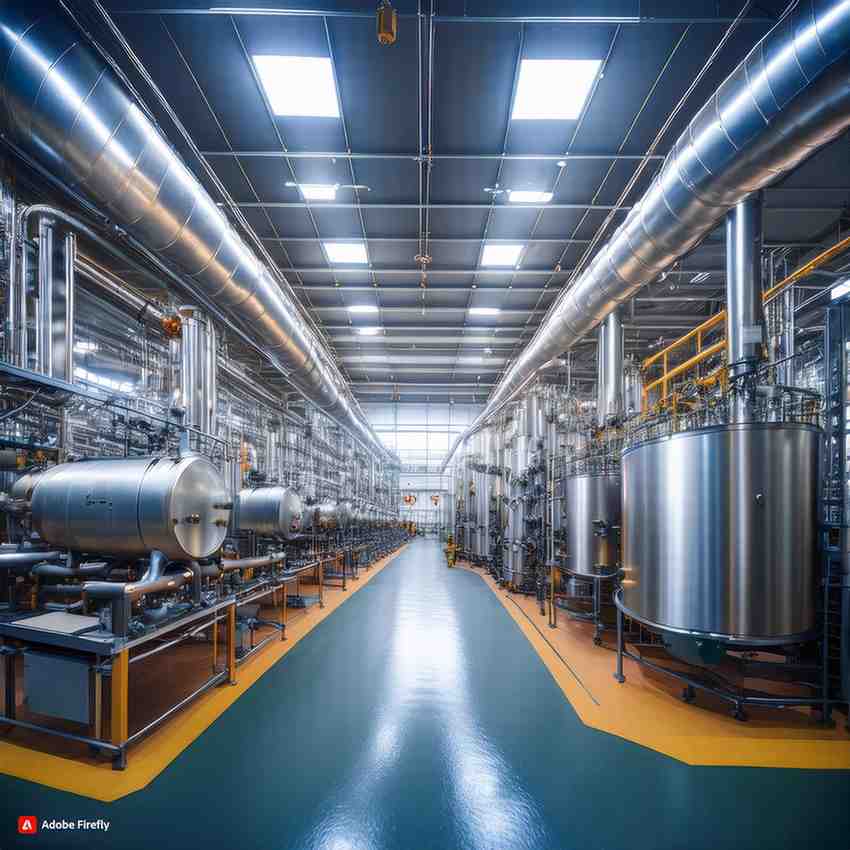
Enhancing Conveyor Belt Performance with Advanced Rubber Compounds: Strength Meets Efficiency
Using Advanced Rubber Compounds to Improve Conveyor Belt Performance: When Strength Meets Efficiency Conveyor belts made from advanced rubber compounds have better properties than traditional belts. This means the belts can do more jobs well. Here is how:
Wearing Down Wear and Tear:
Do you remember that these rubbers are very good at resisting damage from rubbing or scraping? Because they are, belts last longer if they are made from them. It is like having a protective shield along the lengths of all your belts – and not just any shield but a tough one. For example, a mining company was using conveyor belts to move large amounts of sharp-edged rocks around. These stones quickly made holes in their traditional belts causing lots of regular wear and tear. But when the company changed to belts containing advanced rubber compounds, they found something amazing happened: wear rates dropped by up to 40%. This meant fewer new belts needed to be fitted as replacements each year saving both money and time normally lost during repairs.
Flexibility and Strength: A Dynamic Duo
- Bending Without Breaking: Conveyor belts must flex without damaging themselves as they move along curved paths or uneven surfaces. They do this job particularly well thanks to high-tech rubber compounds that let them bend a lot – essential for staying in one piece while going around rollers or over bumpy tracks. But just because these materials are super-flexible doesn’t mean they’re weak.
- Strength Under Pressure: In fact, tensile strength (the amount of stretching or pulling they can take before breaking) is very impressive indeed! A belt made from such compounds can therefore manage heavier loads without the risk of snapping mid-job. Engineers also love data on how well things work under extreme conditions — like temperature changes: With regular belts for instance one might have to avoid using them if it gets below freezing (32°F/0°C) or above boiling (212°F/100°C) because at either point the belt might stiffen up & crack OR become so soft it stretches too much as moves around pulleys, etc.
Conquering Chemical Challenges
Chemical Compatibility: In rough industrial settings, conveyor belts come into contact with many chemicals such as oils, greases, and even corrosive substances. Advanced rubber compounds are specially designed to withstand exposure to these chemicals without degrading or losing their effectiveness. Technical Specifications: Some advanced compounds have extremely good resistance to particular chemicals — for instance, those formulated with nitrile rubber which provide outstanding resistance to oils and greases. Such specialized compounds can be used in places like food processing plants and recycling centers.
Through the utilization of cutting-edge rubber compounds, conveyor belts can do more than just move materials — they also become dependable workhorses that can operate in tough conditions while carrying heavy loads. In the following paragraphs, we will look at the benefits, financial upside, innovations, and real-world examples of these developments and show how their use improves cost efficiency in material handling. If you are interested in going deeper, check out Conveyor Belt Maintenance Tips: Revamp Efficiency & Lifespan.
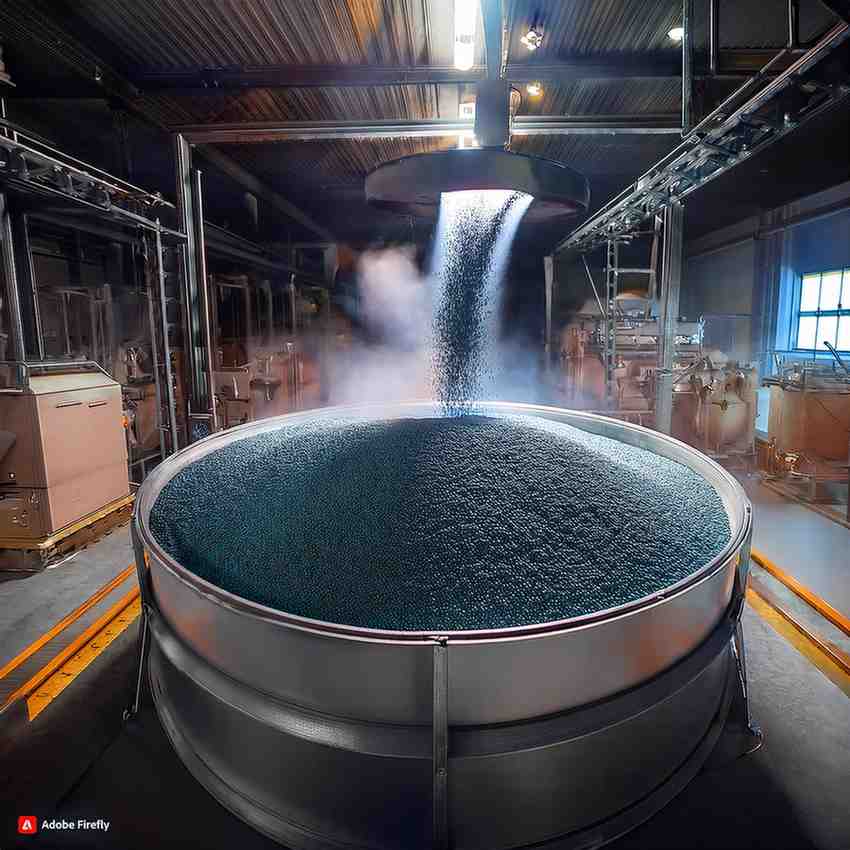
Benefits of Advanced Rubber Compounds: The Winning Formula
The benefits of advanced rubber compounds are unparalleled for material handling operations: Why?
Strength in Numbers: Increased Load Capacity
Effortlessly Carrying More. Conveyor belts made with regular rubber compounds have limits on how much they can transport. This is not the case with belts using advanced compounds. They have such exceptional tensile strength (how much weight they can support without breaking) that loads can be increased without performance being affected. Just think about a system moving hefty machine parts or lots of gravel: if you use advanced rubber compounds loads can be moved efficiently boosting materials handling — maybe even cutting the number of belts needed. For instance, when cement manufacturer upgraded their belts to those containing these kinds of compounds, their capacity went up by 20 %. That means each run could shift more materials and overall production efficiency improved too.
Less Maintenance, More Material Movement: Reduced Maintenance and Downtime
If conveyor belts have to be replaced too often, they can spend more time in the workshop than working. However, tough new rubber compounds cut the amount of upkeep needed – as statistics from the National Mining Association show. Its studies reveal systems using these advanced materials require a quarter less servicing than those that rely on older versions; this enables them not only to last longer overall but also helps maintain an uninterrupted flow of goods along their lengths at all times.
A Cost-Effective Choice: Long-Term Savings
While the upfront cost of conveyor belts with advanced rubber compounds might be slightly higher than traditional options, the long-term benefits outweigh the initial investment. Consider this cost-benefit analysis with additional figures based on industry averages:
Factor | Advanced Rubber Compounds | Traditional Rubber Compounds |
Initial Cost | 5-10% Higher | Lower |
Maintenance Costs | 30% Lower (Reduced Frequency) | Higher (More Frequent Replacements) |
Downtime Costs | 20% Lower (Less Maintenance) | Higher (More Downtime for Replacements) |
Belt Lifespan | 2-3 Times Longer | Shorter |
Considering these factors, advanced rubber compounds come out on top for cost-effective materials. Lower maintenance requirements, less downtime, and longer belt life all add up to significant overall cost savings over the conveyor system’s lifespan. It’s an investment in efficiency over time: plus you’ll find that using them helps your materials move better too! Consider also exploring Custom Polyurethane Parts: Aerospace Engineering Precision.
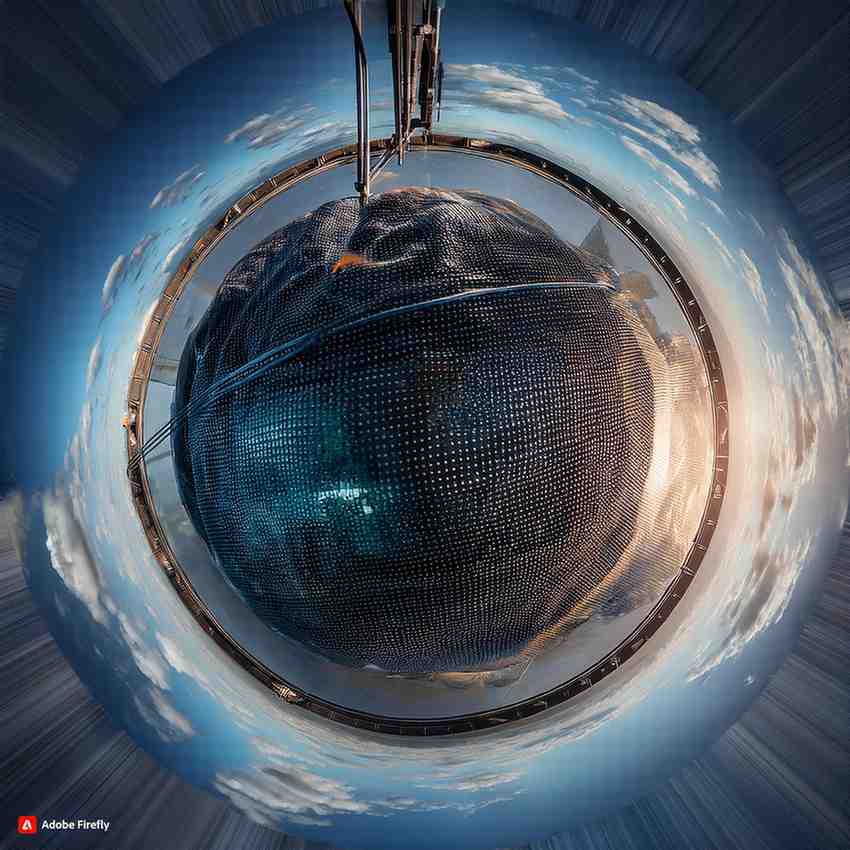
Innovations in Rubber Compound Technology for Conveyor Belts
The conveyor belt industry is not sitting still when it comes to technology. By formulating innovative rubber compounds, manufacturers can create materials that do even more –- better performance plus greater efficiency. Here are a few of the latest developments:
Advanced Compositing Techniques: A Stronger Bond
Traditional rubber-compounding methods are not being replaced. They are, however, being supplemented with new techniques that take performance to a higher level:
- Multi-layer Compounding: This involves putting together different types of rubber with specific properties. A wear-resistant top layer might be combined with a flexible inner layer, for instance. The result? A belt that is tough as well as adaptable — and therefore has increased wear resistance plus improved troughing (material-carrying) capabilities.
- Incorporation of Nanomaterials: Another case in point is the employment of nanomaterials (such as nanotubes and graphene) within rubber compounds. These substances are incredibly strong! They also bring benefits like better abrasion resistance and tear strength to the party. If belts could talk, these would be saying “We can cope with harsh environments even longer than usual.”
Specialty Blends: Tailored Solutions for Specific Needs
Conveyor belts cannot use the same material in all industries—it’s just not practical. That’s why we offer specialty rubber blends. These custom formulations are designed for specific needs. For example, logistics companies that move hot materials such as clinker need belts that can handle very high temperatures without burning or breaking. Belts made with our special heat-resistant polymers stay strong and last longer than those made with regular materials when used at these intense levels. Case in point – a business was wearing out belts quickly because they moved so much hot asphalt. When they switched to using our heat-resistant rubber blend, their belts performed a lot better. One statistic shows just how much tougher these belts were under extreme heat — there had been a 40% reduction in wear-and-tear damage! This meant fewer maintenance costs plus also having each belt last longer before it needed replacing.
Integration with Modern Conveyor Systems: A Symphony of Efficiency
Modern conveyor systems work best when they can be linked with other high-tech equipment. Rubber compound technology is helping in several ways.
- Sensor Integration: some compounds now have sensors built into them so that the condition and performance of the belt can be monitored constantly. By collecting data on how a belt is used and worn out in real-time, it becomes possible to predict when maintenance might be needed – and so avoid breakdowns caused by wear and tear.
- Technical Detail: Some compounds have been developed that can cope with having temperature sensors incorporated within their makeup. This means staff can keep an especially close eye on whether belts are getting too hot (a common cause of parts failing) and take action if necessary.
- Smart Material Handling: A key aim for tomorrow’s conveyor systems will be to link up more and more with robots and computers doing the handling work. If you want materials to move around a factory quickly, easily but above all safely, then the belts carrying them may need to ‘talk’ to machines making or packing goods as well.
One big plus of developing such innovative new uses for rubber compound technologies is that manufacturers end up producing not just tougher products for the industry but ones that fit its requirements better each time they change. It’s like having clothes that mend themselves while warning what might wear out next; plus every season’s styles come along too! One big surprise in rubber compounding is polyurethane. Read and discover more about Polyurethane Applications: Exploring Advantages and Common Uses.
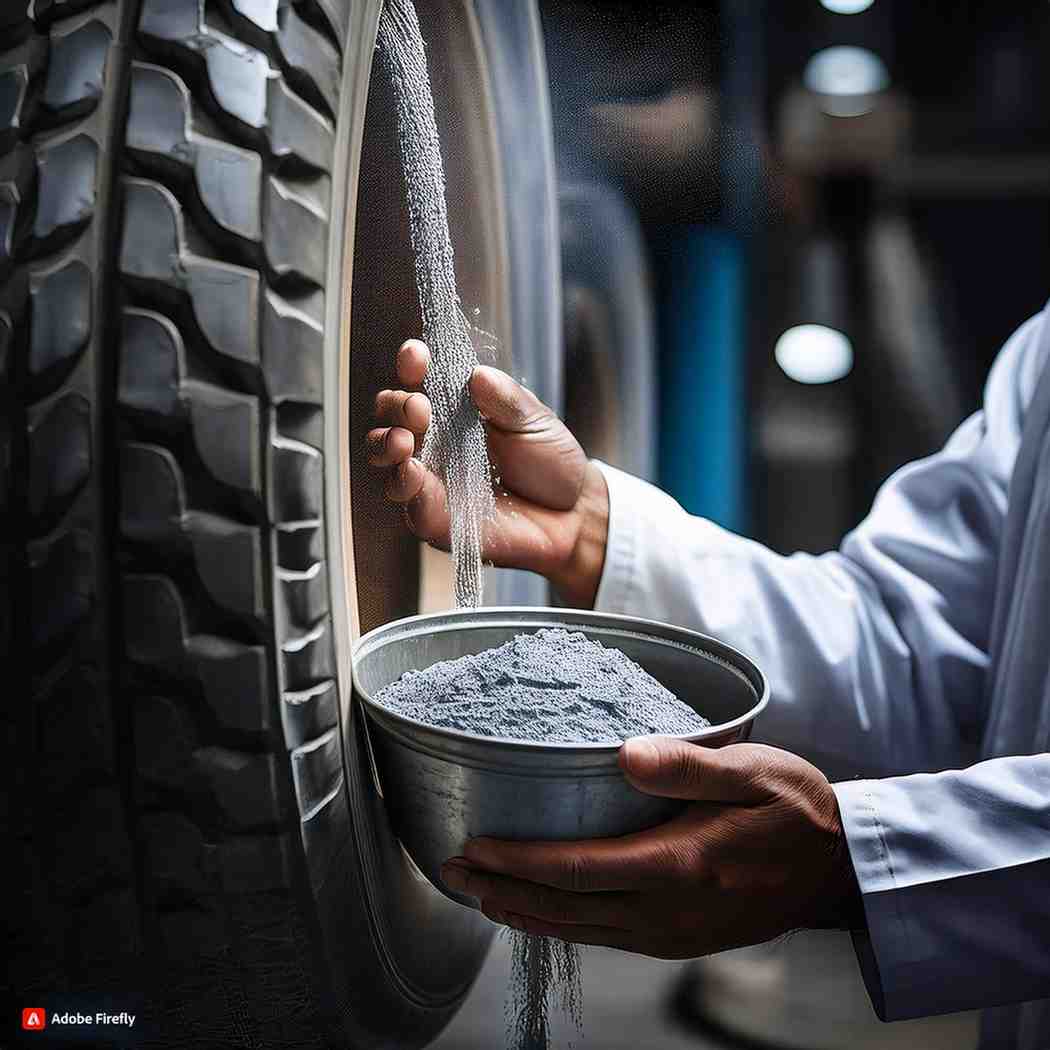
Real-World Power: Advanced Rubber Compounds in Action
Advanced rubber compounds don’t just talk the talk – they walk the walk. Here are two case studies that show how these materials can make a real difference:
Conquering the Grind – Advanced Rubber Compounds Boost Mining Efficiency
- Challenge: A large iron ore mine was having big problems with the belts on its conveyors. Every day they had to transport tons of rock – and the belts were wearing out far too quickly. Standard belts don’t last long when used hour after hour to move rough rock over steel rollers; the cost of replacing them all the time was hurting the mine’s profits as well as its production schedules (things like cleaning and maintenance jobs take longer if machinery has to be stopped every day for new belts to be put on).
- Solution: Engineers realized something else was needed so they decided to try belts made from rubber which can resist wear caused by abrasion. These types of rubber are very strong indeed: tests have shown that they can cope with materials rubbing against them that would cause standard rubber to disintegrate within minutes.
- Results: When they fitted belts made from these special rubbers the results were impressive. Each belt lasted an average 30% longer than those currently being used – with three benefits across the board; reduced costs due to less frequent replacement; fewer shutdowns because maintenance could be carried out after longer periods of continuous operation (uptime); plus overall improvements in efficiency because there were fewer interruptions to normal working patterns by mining engineers.
- Technical Details: The formulation used during this particular trial included extra polymers and other materials that reinforce strength. It had been hoped these might provide extra resistance against cuts etc., caused by sharp fragments of rock constantly hitting against moving parts like belts (a common problem known as abrasion).
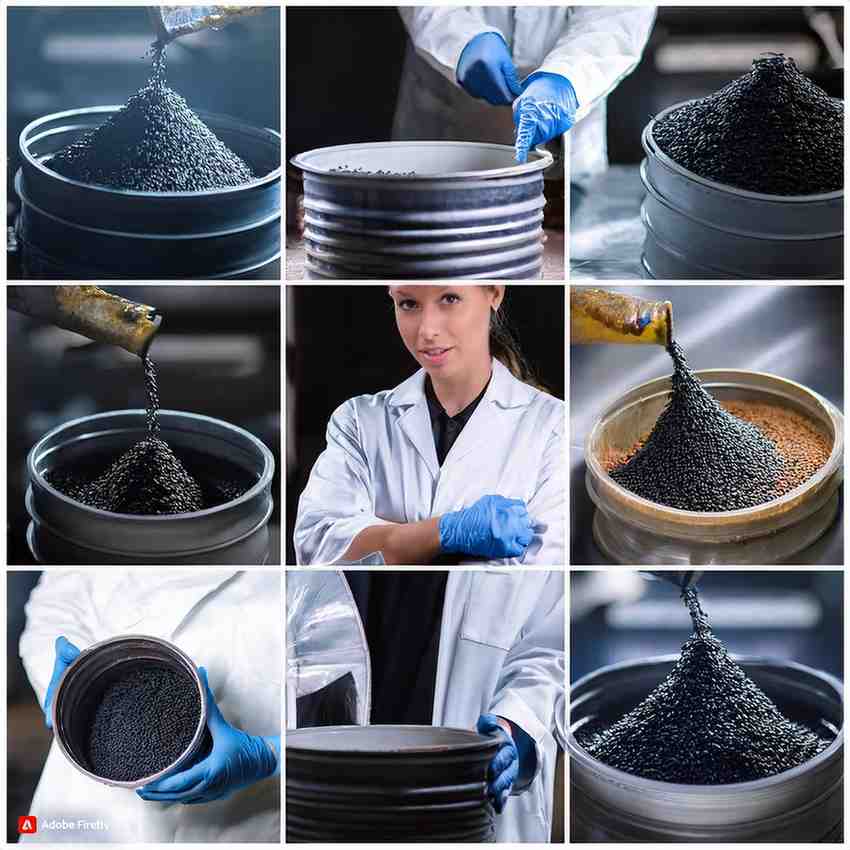
A Smoother Operation – Specialty Rubber Blend Enhances Manufacturing Efficiency
- Challenge: A factory that makes hot tar roof tiles had problems with its conveyor belts. The tar was causing the belts, made of normal rubber, to fall apart – putting workers at risk and stopping production. Workers had to spend lots of time fixing belts; sometimes there weren’t enough working belts left for the job in hand.
- Solution: The factory decided to try using belts with a special type of rubber that can cope better with heat. This rubber has chemicals added to make it resist high temperatures (heat-resistant polymers) and stop fires from starting too easily (flame retardants).
- Results: Switching to these belts brought several advantages. They stay cooler so can be used with very hot materials like tar without falling apart. Because they last longer between repairs, staff spending on maintenance fell by one quarter. Less stopping and starting meant more work got done as well over each shift: efficiency rates went up noticeably. As fewer breakdowns also mean you do not need as many spare belts “just in case”, overall usage figures improved further.
- Statistical Evidence: Since the new-style belts were introduced, breakdowns due to overheating have fallen by 70% based on figures collected over periods when all belts were now of this type; there were also fewer instances where production had to be halted because none were available for use whatsoever.
The conveyor belt industry is being changed by advanced rubber compounds in amazing ways. These examples from everyday life show how conveyor systems can work better when they have new kinds of rubber: They perform well, need less upkeep—and so last longer. This kind of formula also makes things safer overall meaning factories using them can make savings while upping productivity levels. We are only just starting to see the benefits these materials can bring: as researchers continue developing hi-tech options further improvements will surely follow suit. A whole host of breakthroughs are on the horizon thanks part this cutting-edge science – watch space! You may want to learn more about Industrial Rubber Rollers: Know their Role and Procedures.
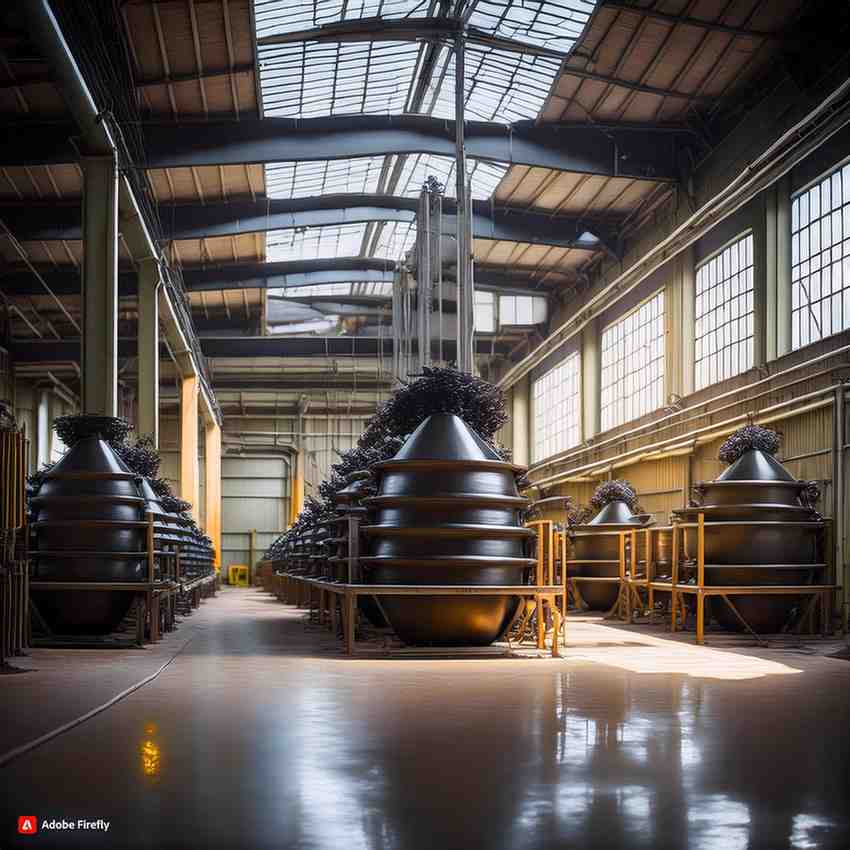
Conclusion
To sum it up, through this investigation we have delved deep into what makes a conveyor belt more than meets the eye. A quiet revolution is happening thanks to cutting-edge rubber compounds – and those in the know can do amazing things with them.
These special substances have some impressive features. They can stand up to lots of wear and tear exceptionally well; they also won’t fall apart when they come into contact with certain chemicals. Put simply: using advanced rubber compounds has benefits such as making belts last longer, carry heavier loads, and need less looking after.
When conveyors are made with these materials, it means they can work better (increased efficiency) for longer (greater productivity) without costing as much money to keep running (or repairing). In the future, there will be even cooler things people find out they can do! If you work in areas like buying stuff for business, keeping it all running nicely, or designing systems so everything happens automatically: pay attention!
By taking advantage of the special powers contained within advanced rubber compounds; there could be loads (pun intended) of advantages waiting just around the corner.
Maybe you are still full of questions. Contact directly our customer support, and reach your answers and decisions with the best offer.