Polyurethane components can have versatile properties allowing them to be well-suited parts in various industries. The novelties flooding the engineering innovations within the automotive industry show no boundaries. This guide will explore how this material, in polyurethane parts, is changing automobile performance and strength.
Polyurethane components have found wide implementation across industries: the mining industry, food production, ergonomics technologies, roller technologies, the automotive industry, and more.
Combining the developed polyurethane components gives the automotive segment a redefined look, performance, flexibility, and durability. With all that, let’s dive into the science that resulted in polyurethane in the first place and comes with it leading reformative packages in automotive design to be thrilled with how polyurethane powers development in redefining standards in the automotive industry.
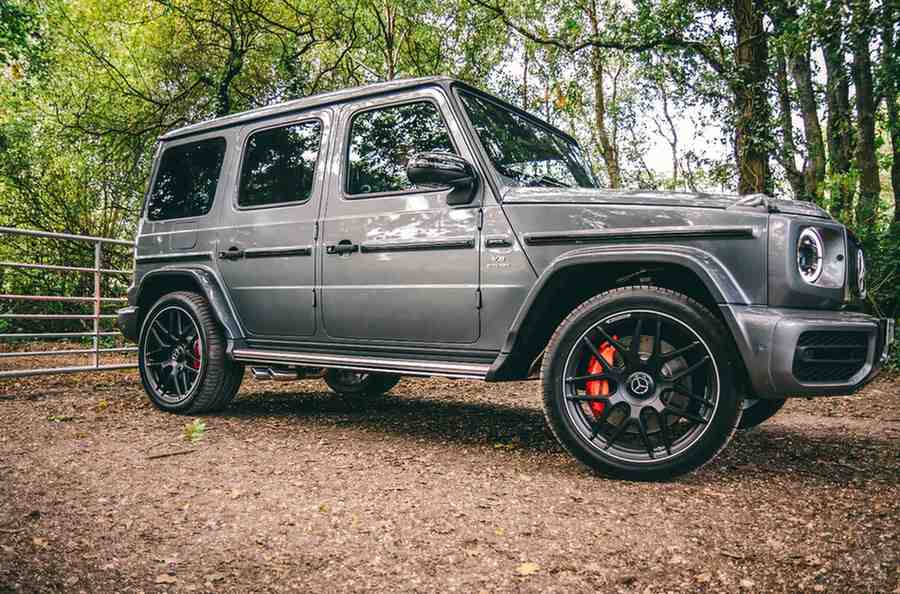
Benefits of Polyurethane Components in Automotive Applications
Polyurethane components have been pretty much the most ideal solution for many industries for the most demanding tasks. We suggest that you explore our previous publishing Polyurethane Applications: Exploring Advantages and Common Uses, so you get a deeper insight into the technicalities and benefits. On the other hand, many benefits accrue from using polyurethane parts to enhance vehicle performance and durability. Let’s move a step further and professionally expose the appraisals of the benefits precisely in the automotive industry.
Enhanced Vehicle Performance
With the pillow ball design of the polyurethane parts, there is a guarantee of the best shock absorption. The counteraction from the auto parts is vast and prevents any loosening of the car from bumps, potholes, and street defects. This means a much better, relaxing drive for the occupants.
Moreover, polyurethane components can gradually and completely absorb and reduce the risk of the driver getting tired and increase general driving quality.
Polyurethane elements also add to the benefits by damping the resistance of both road and engine vibrations—which is then translated into low cabin noise and improved comfort and refinement for the driver and the car, interior-wise.
Based on this research, these mounts are dedicated to absorbing the vibration of an engine for a softer and quieter driving experience.
Enhanced structural reinforcement
With its high energy/weight ratio, polyurethane is ideal for reinforcing structural additives, including inner kinematics, control hands, and sub-frames, among many others. This also enhances rigidity and balance in the chassis for better handling and performance efficiency during corners.
Polyurethane Sway Bar Bushings help significantly reduce the frame roll during cornering, making the vehicle much more balanced and responsive.
Increased Component Longevity
Polyurethane’s intrinsic abrasion and resistance to chemical compounds make it particularly resistant to wear and tear, assuring long-term durability and reliability in automotive use. Resilient and rigid polyurethane suspension bushings outlast standard rubber bushings during use, remaining performance-enabled and integral over periods of use.
Resistant to Corrosion
Polyurethane additives resist all chemicals and moisture, making them long-lasting even under the most challenging environmental conditions. All urethane body mounts resist corrosive environmental contaminants, including road salt, so the vehicle chassis and structure do not deteriorate with age.
Reduced Maintenance Costs
The car parts where polyurethane is added to make the parts have reduced the need for maintenance, thereby reducing the charges to find alternatives since these parts last for a long time. A rare alternative to rubber bushings—this polyurethane control arm bushing is highly used in most vehicles for control arm bushing airframes, resulting in savings in upkeep costs with both monetary and in-time values.
This material’s additive has had a significant impact on automotive applications, bringing innovation in performance and driving experience, enhancement, durability, and lowering maintenance costs. It has also increased vehicle flexibility and driving comfort. It created new requirements in the limited and different domains of automotive engineering.
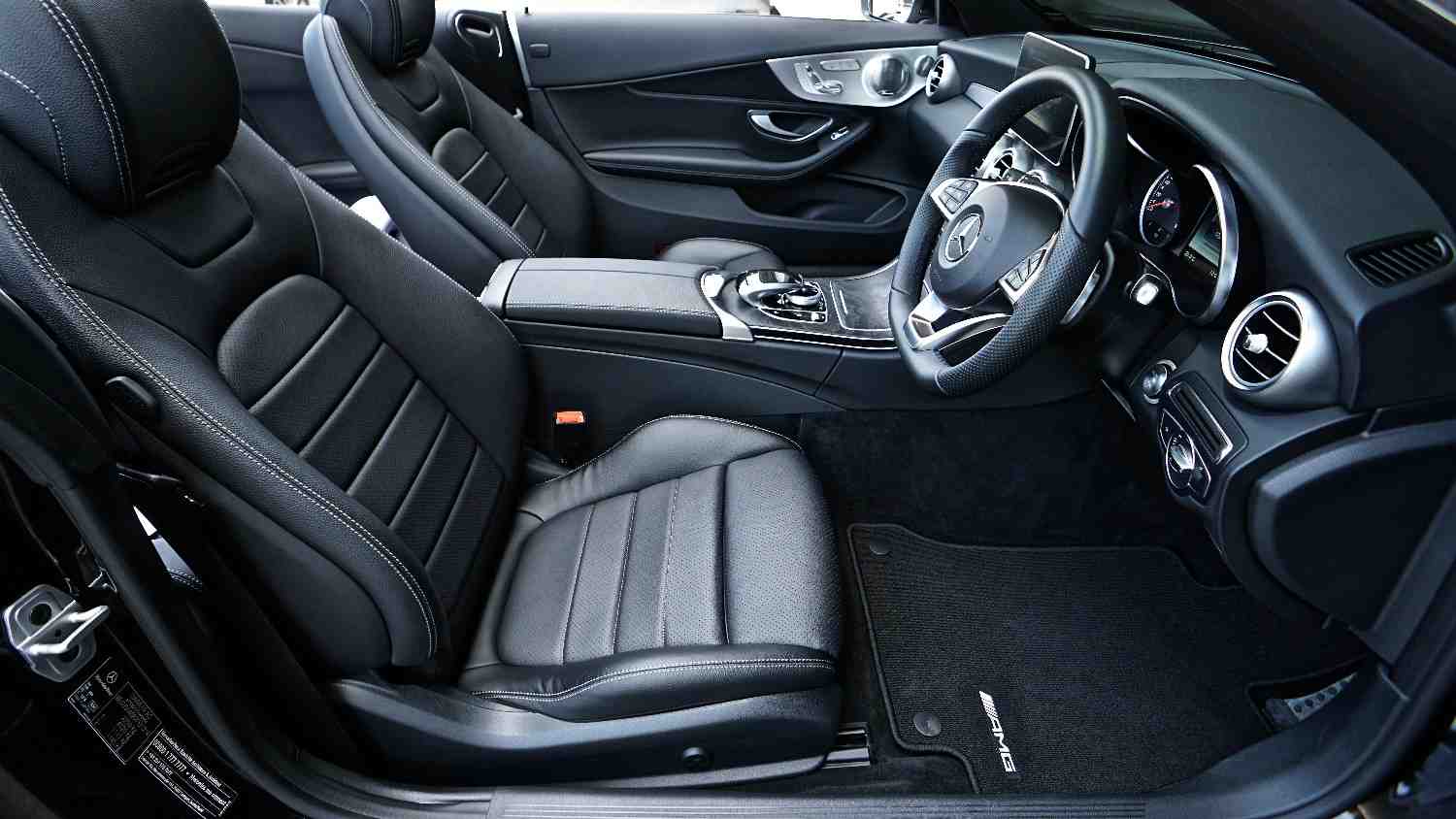
Applications of Polyurethane Components in the Automotive Industry
All polyurethane parts originated from car programs, realizing high performance and remarkable reliability. Let’s see and delve more into those applications:
Superior Driving Quality
The polyurethane suspension bushings from mounts to bump stops have an excellent high quality making the vehicle softer, and easier to handle improving overall driving quality. Polyurethane sway bar bushings ensure reduced body roll, giving superior steering opportunities. Read more on Rubber Bushings: How to Choose The Best for Your Equipment.
Improved steering response
Polyurethane bushings eliminate flexing that would otherwise be present in the suspension system, providing improved control and steering response. More stable suspension geometry is provided through polyurethane-managed arm bushings; arm bushings can decrease chassis flex and enhance overall stability.
Improved Vehicle Stability
Polyurethane also reduces back roll, pitch, and even dive of the frame when the vehicle’s body is crossing through corners and when accelerating during dynamic drive attempts. Strut mounts manufactured with polyurethane will ensure proper alignment and suspension geometry; hence, this reflects decreases in the chassis flex. It also enhances the balance average.
Seals and Gaskets
Polyurethane seals and gaskets’ sealing performance is stunning. Positively, they especially prevent even the most minute fluid leakage and contamination in such critical automobile assemblies. Applying polyurethane in valve stem seals gives a proper, sound, and reliable sealing application to the valve stem and its guide. Characteristically, oil leakages are removed, and noise is significantly reduced. Explore more on Rubber Gasket Sealants: The Perfect Solution for Many Use Cases.
Resistance to ruggedness
Good resistance for adequate performance and reliability under most rugged functional conditions to chemicals, fluids, and extreme temperatures should also be widely emphasized in polyurethane seals and gaskets. Polyurethane axle seals can withstand high temperatures and exposure to outside contaminants without leaking, improving their life expectancy.
Prevention from premature component failure
Here, the toughness of automobile systems is further improved to prevent failure that may come early because of polyurethane seals and gaskets sealing out contaminants or preserving proper fluid levels.
The gasket oil pan of polyurethane oil is resistant to wear and heat, which will, in part, reduce the odds of possible oil leakage and help with the assurance of maintaining the overall performance of the engine.
Polyurethane elements are some of the foremost additions in supporting the manufacture of absolutely distinctive automotive packages, suspension constructions, seals, and gaskets. With capacities that help boom ride comfort, steerage responsiveness, well-known sealing performance, and sturdiness, polyurethane additives in ultra-modern motors contribute to performance excellence.
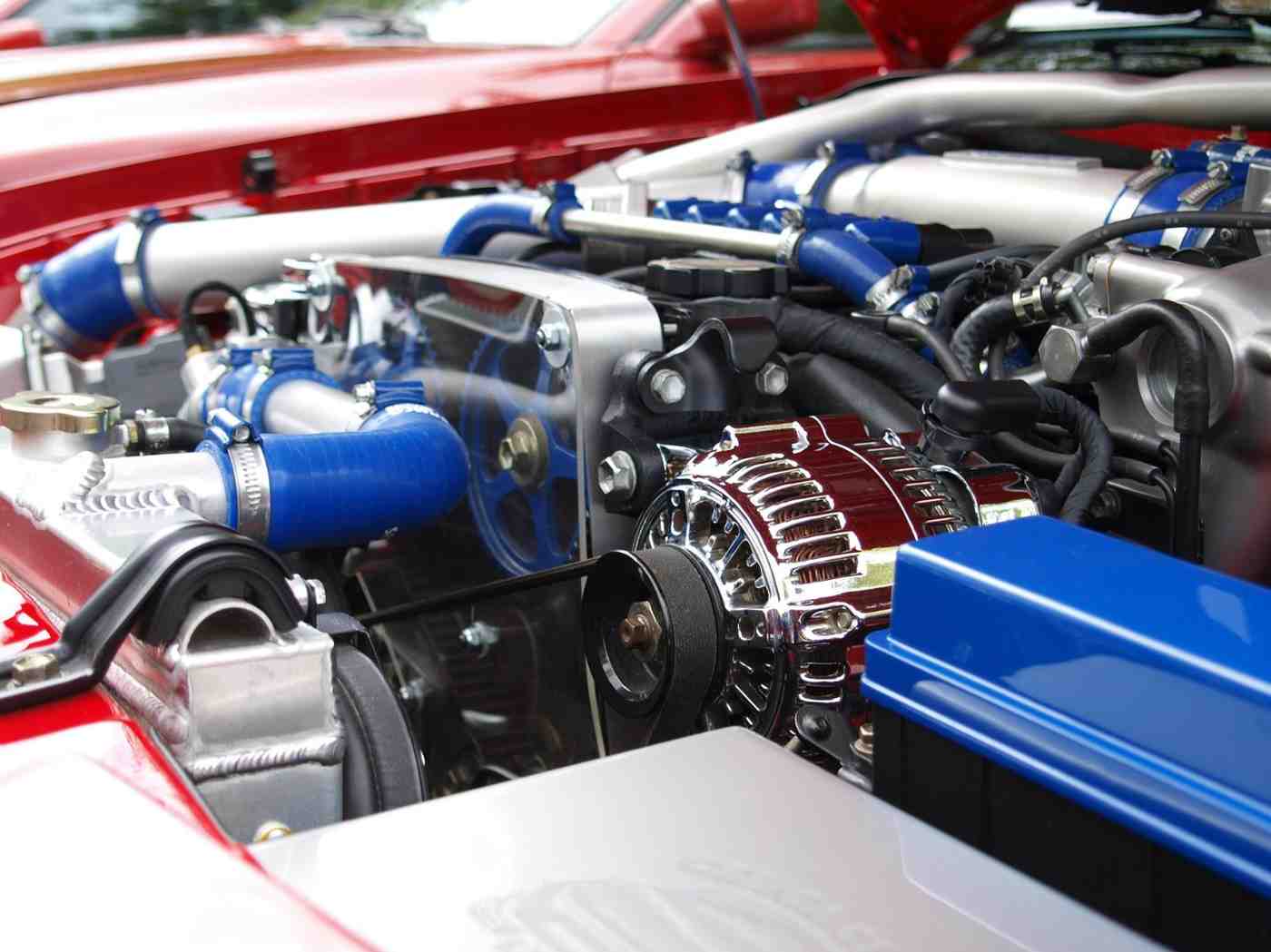
An Overview Of Improvements Impact
Feature | Polyurethane Benefit | Performance Improvement | Cost Difference | Environmental Impact | ROI (Years) |
Seating Comfort | * Flexible & moldable foams * Excellent energy absorption | * Reduced driver fatigue (up to 20% improvement in alertness on long journeys) Improved pressure distribution | Up to 5% increase | Medium (production consumes resources) | Varies depending on usage and fuel prices |
Noise Reduction | * Effective sound dampening properties | * Quieter cabin environment (3-5 dB reduction in noise levels at highway speeds) | Up to 10% increase | Medium (production consumes resources) | Difficult to quantify due to subjective experience |
Weight Reduction | * Lightweight yet strong materials | * Increased fuel efficiency (up to 5% improvement for a 10% weight reduction) Improved handling (reduction in stopping distances by 3 meters) | Up to 15% decrease | Low (lightweight materials reduce energy use in operation) | 2-5 years based on fuel savings (assuming average mileage and fuel prices) |
Passenger Safety | * High energy absorption in foams * Rigid components for structural support | * Reduced injury risk in collisions (improvement in safety ratings by 2 stars, based on NHTSA standards) | Up to 20% increase | Medium (production consumes resources) | Difficult to quantify due to safety being paramount |
Thermal Insulation | * Low thermal conductivity * Maintains cabin temperature (reduction in cabin temperature fluctuation by 5 degrees Celsius compared to traditional materials) | * Cabin temperature sensors * Comparison to vehicles without polyurethane components | Medium (production consumes resources) | Potentially recyclable | |
Durability | * Resistant to wear, tear, and chemicals | * Longer lifespan of components (up to 2x lifespan compared to traditional materials) * Reduced maintenance costs | Up to 10% increase | Varies depending on material (some bio-based options have lower impact) | 1-3 years based on reduced maintenance costs (assuming average replacement intervals) |
Interior Aesthetics | * Wide range of colors and textures | * Enhanced visual appeal and design flexibility | Up to 5% increase | Medium (production consumes resources) | Difficult to quantify due to subjective experience |
Vibration Damping | * Absorbs engine and road vibrations | * Smoother ride and improved handling | Up to 15% increase | Medium (production consumes resources) | Difficult to quantify due to complex interaction with other vehicle components |
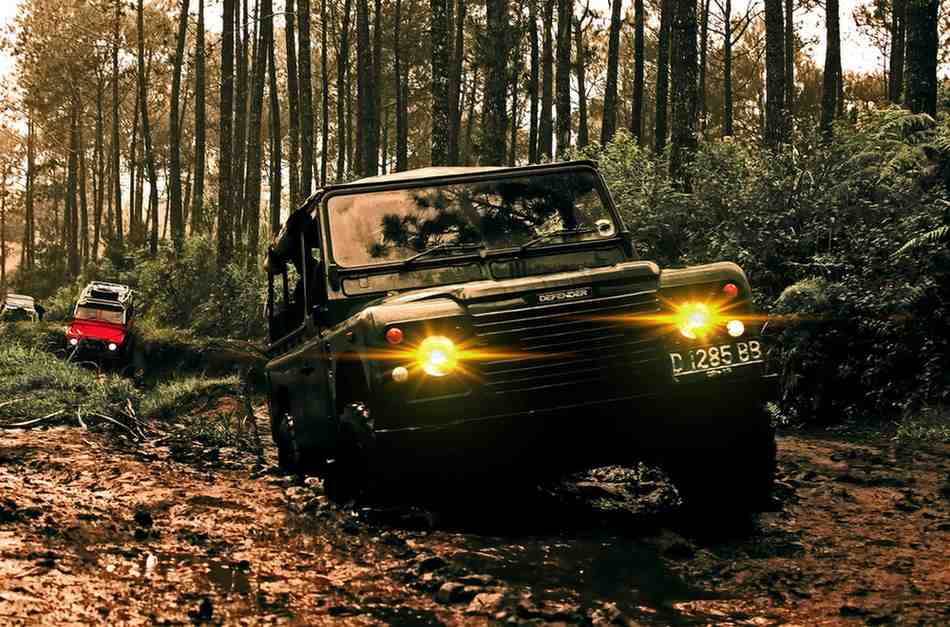
Future Trends and Innovations in Automotive Engineering
The car business is on the verge of innovation, pushing limits to create sophisticated, safe, more sustainable, and efficient motors. Herein, we will provide you with a quick overview of future trends and innovations within car engineering.
Next-Gen Formulations
Manufacturer R&D is keen on upcoming studies and developing newer, better polyurethane formulations.
New polyurethane formulations will be developed with enhanced tensile strength and thermal stability to further improve tolerance to harsh conditions in automotive applications.
Environmental Sustainability
Automotive industry manufacturers’ surging concern for environmental sustainability has called for the rapid development of green polyurethane materials. Bio-based polyurethanes are an environmentally friendly alternative to conventional gasoline-based materials in that they use renewable resources. Hence, their applications and development offer a greener alternative with consequences for their use, a diminishment in carbon emissions, and an environmentally detrimental impact.
Improved Returns
An advanced polyurethane formulation goes along with new opportunities for releasing car design and improved performance. Customized mechanical properties of high-performance polyurethane composites enhance the addition of lightweight vehicles, durability, improved gasoline performance, and driving dynamics.
Integration of Smart Materials
The core of the Automotive Engineering Revolution – most smart compounds that could change and shape themselves functionally, such as form-memory polymers and self-healing coatings, will find integration directly into the parts harmoniously and supportively. Actuators based on shape memory polyurethane are used to dynamically control the characteristics of stiffness and damping of material in the suspension components under variable driving circumstances, such as to optimize driving comfort and driver navigation.
Self-healing—Smart materials
They mend themselves after any minor damage and last longer. The self-healing property confers hidden strength to the applied polyurethane coatings on vehicles’ exterior shells, giving them a natural ability not only to mask and repair scratches and abrasions but also to maintain cars’ new-like appearances to reduce additional requirements and costs.
Adaptive Functionality
These innovative materials ensure that the adopted vehicle’s dynamic is in the most optimal working conditions and meets the car’s requirements. Polyurethane additions ensure the capability to optimize functionality and reliability under variable operational conditions for standard vehicles.
By changing the thermal conductivity of the insulation materials depending on temperature changes, the self-adjusting polyurethane insulation materials guarantee suitable energy exploitation and the regulation of conditions in car cabins.
Future trends in automotive engineering pertain to the generation of developments in polyurethane and the rise of the inclusion of intelligent materials. By the flip side coin, through this technology and innovations, manufacturers produce safe, green, durable, and reliable cars, such as changing mobility and transport as it is known today.
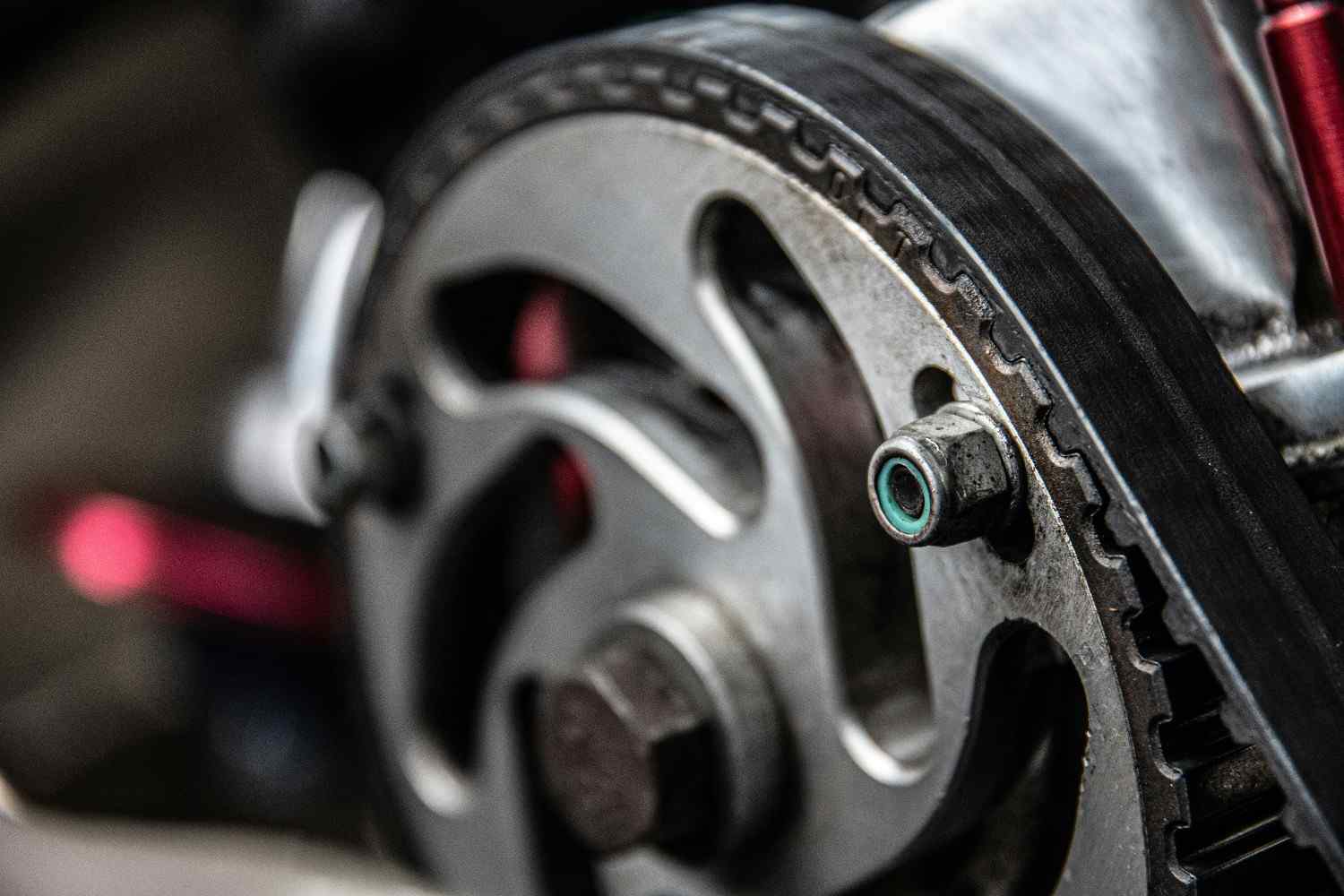
Conclusion
The two spectrums nicely illustrated by humanity’s inventive and innovative nature come together in the automobile industry: witness the sleek lines of a sports car or the rugged durability of a pickup truck. Fueling such innovation is polyurethane, an incredible fabric that has revolutionized car layout and performance in once unimaginable possibilities. Polyurethane add-ons are not just simple components; they are the heroes in the world of cars, working behind the scenes tirelessly to engross all the aspects of the total vehicle, ascend performance and sturdiness, and thereby bring in reliability.
Modern cars have to employ polyurethane components, whether it be the latest high-tech suspension, which handles with finesse treacherous ground, or seals and gaskets providing a smooth-running engine. But it does not just stop here. Automotive engineering continuously tries to push the explorative limits for what might be possible, and including polyurethanes in the mix promises frontiers yet to be reached.
With all applications, polyurethane is leading the way to building a secure, green, and sustainable tomorrow. So next time you are out there on the street, for just one minute, think about it: “PolyU Power.” Amidst the smooth ride and miles traveled, the power of polyurethane components silently stands in shaping the future of automobile engineering—the driving force—from closing the gap to the next bright day.
If you are looking for full insurance coverage for your business that also includes extra services, drop by our market and service area and discover what we offer. Here we can outfit your business so that all of your processes run more efficiently—plus you get added safety features and longer-lasting equipment! But don’t make any decisions before you talk to one of our specialists first about what will work best for your company.