Industrial roller hardness affects the machinery on a large scale. Imagine that your conveyor system comes to a standstill instead of a machinery malfunction because the rollers are too hard. Any company that moves goods around knows this is a worst-case scenario—but who would have thought that getting the right result would be so complicated? The type of roller you choose is crucial and one of the most important things about it is how soft it is (or hard, for that matter). In this blog article, we will look at a durometer on the Shore A scale. Understanding more about industrial roller hardness and Shore A could make all the difference when selecting rollers that will do exactly what you need them to; whether that involves coping with heavy impacts or tasks in the mining industry, food production, ergonomics technologies, roller technologies, the automotive industry, and more, keeping going mile after mile without wearing down. We will also discuss how our knowledge regarding industrial rubber might help steer decision-making processes surrounding which type of roller would best suit a given scenario—meaning uninterrupted workflow alongside peace of mind.
Shore A Demystified: How to Choose the Right Industrial Roller Hardness
Shore A hardness may be understood using a straightforward tool: a durometer. This gadget does not measure strength conventionally; rather, it assesses how much an elastomeric material like rubber will bend or distort—it’s ‘hardness’. Picture a tiny, uniform finger pushing into such material to observe resistance levels (indentation). Reading will range from 0 (highly elastic and soft) to 100 (rigid and tough). Consider its implications for rollers after grasping this scale:
- Shore A 0-10: Material here is extremely soft with high elasticity: if pressure is applied it will bend a great deal (up to 80% of its depth in indentation). Think about a bouncing ball; it gives lots. Uses for these super-soft rollers include mounts designed to absorb vibrations—they need to deform substantially when shockwaves hit.
- 11-30 Shore A: When we move up on the scale, it means we’re looking at rubbers that are softer to medium-soft. These have some elasticity – if you press with a finger and create a dimple, it will only be 50-80% as deep as in the original untouched surface; but they also hold their own shape well enough. This combination is useful for conveyor rollers carrying things such as electronics or foodstuffs where there needs to be a little “give” so nothing gets broken but no sponginess either.
- 31-70 Shore A: For lots of general-purpose conveyor applications this is ideal. Rollers made from these materials are about medium hardness to hard (20-50% indentation depth): they resist wear whilst being firm enough to absorb bangs. Goods can weigh quite a lot (or there may be quite a thump when they hit the belt) but these rollers won’t distort excessively as they rotate beneath items. If you’ve ever seen rollers on a conveyor belt system moving boxes around a distribution center, or bags of cement at a DIY store – then you probably know what we mean!
- 71-100 Shore A: At the other extreme you’ll find very hard rubbers indeed here (indentation < 20%). They don’t bend much when compressed so are useful in specialist applications including casters for heavy industrial wheels where there must be minimal give under load – otherwise things bounce along rather than roll accurately down flat surfaces such as factory floors.
Now that you have been on the journey for the standard measures let’s see what effect they can reach.
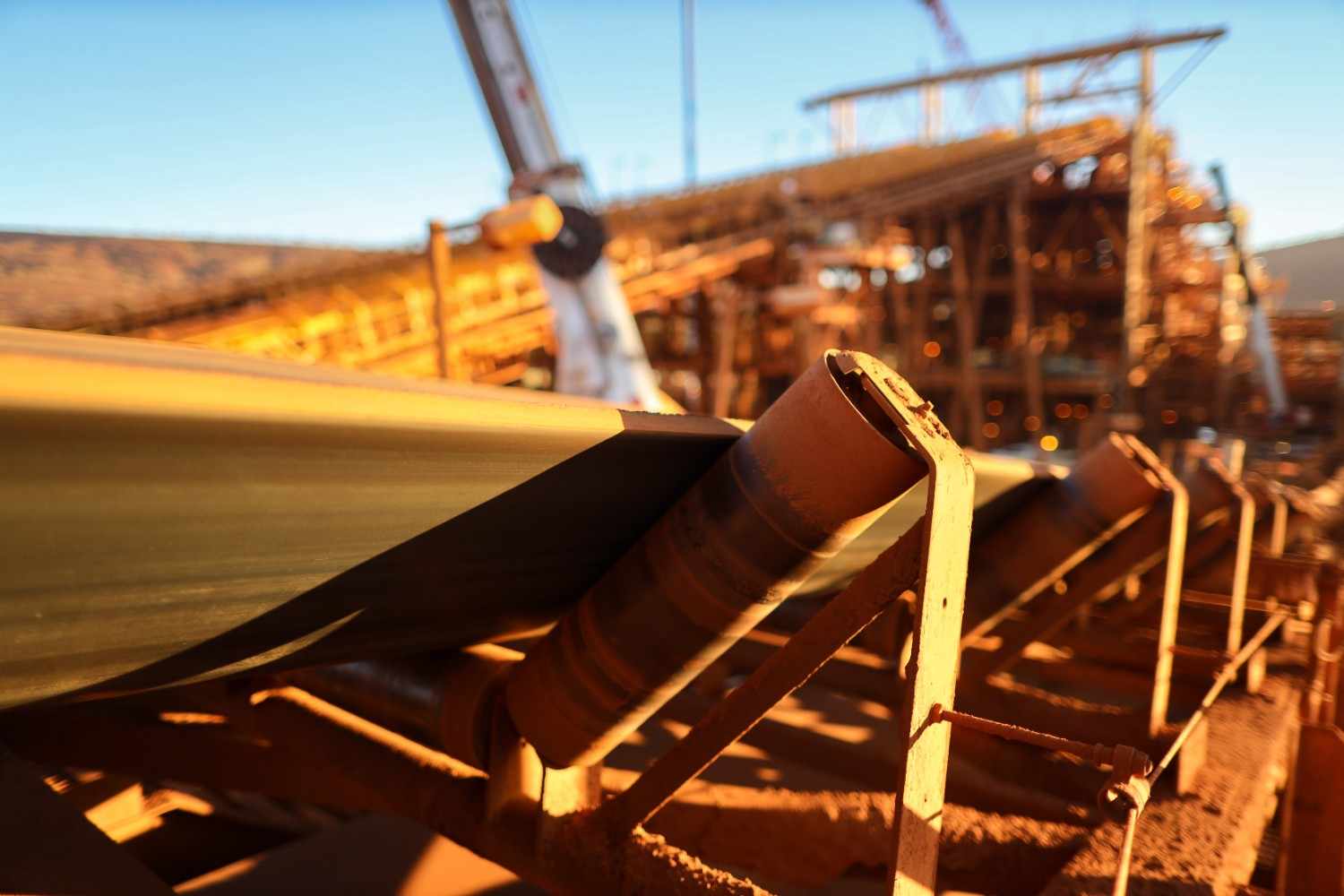
The Effect of Shore A on Industrial Roller Hardness Performance
An Analysis to understand how a roller will perform in key areas, such as elasticity or wear resistance, it’s useful to know its Shore A rating. Here we take a closer look into deflection characteristics when pressure is applied:
- Deflection under Pressure: Soft rollers with a low Shore A reading will compress more under load than hard ones (which have high readings), thus providing some shock-absorbing properties. A 100kg weight placed on a soft 20-shore-A roller might cause it to deflect 5mm, but the same load on a hard 80-shore-A model may make it give only 1mm.
- Wear Resistance: Hard rollers tend to have better resistance characteristics against wear because their structure doesn’t break down easily. But if materials being carried are very abrasive an excessively hard roller could cause damage by being too inflexible.
- Elasticity and Impact Absorption: Softer rollers deform further when hit–they’re more elastic. This does not mean hard rollers cannot cope with knocks though: they just deform less.
Optimizing performance over long periods means selecting rollers whose initial hardness (Shore A durometer) suits them best for your needs; whether this is simply to increase efficiency or perhaps also to cut down on damage costs because of continual use. It’s only part of the wider story!
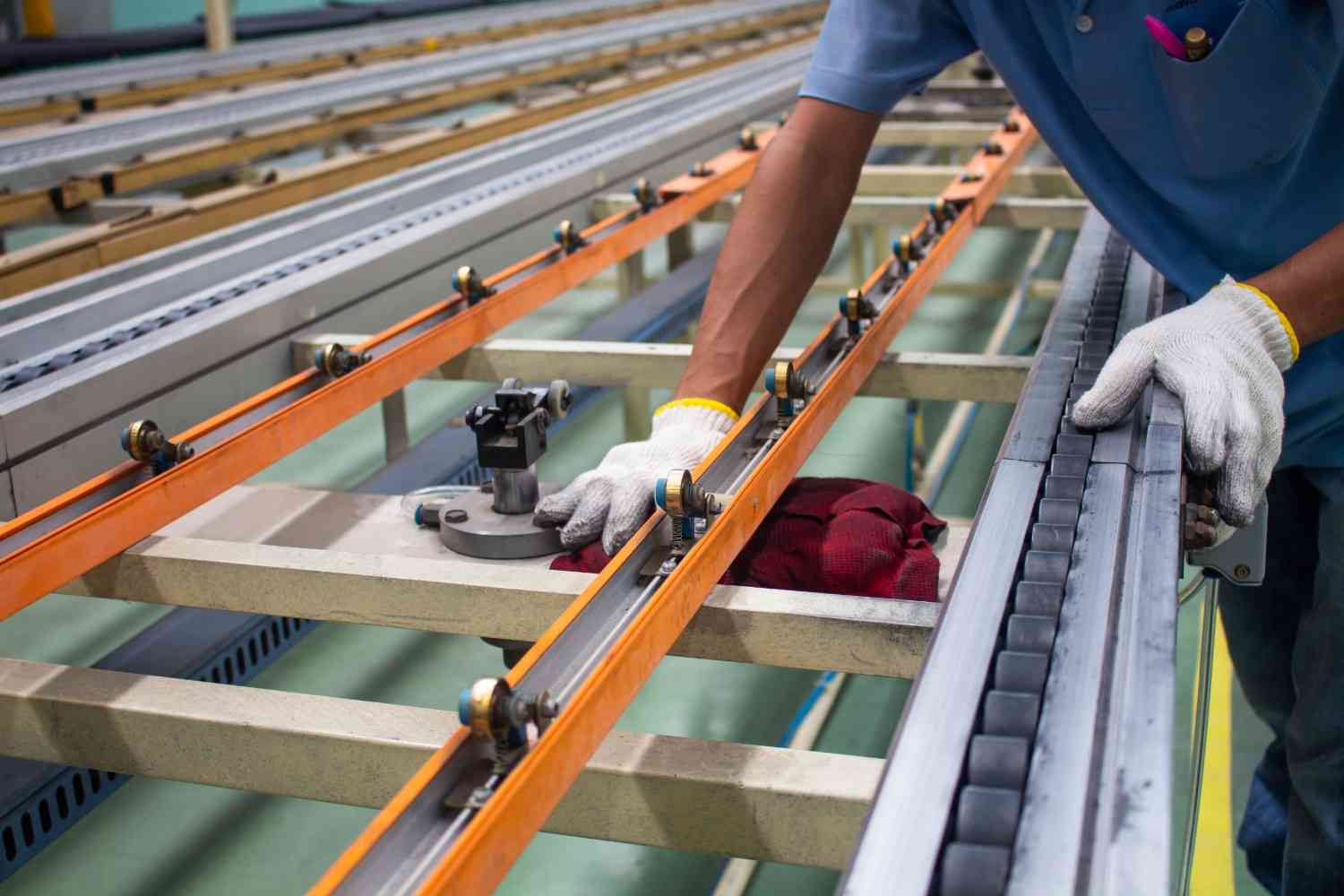
Choosing the Right Industrial Roller Hardness for Your Needs
When picking the perfect hardness for your rollers, it’s not enough to plug a number into an equation and order material. Selecting hardness is also about strategy–how hard or soft you want that roller surface to have implications for performance (will it grip?), wear resistance (how quickly does anything shred it?), and overall efficiency of operation(the way things move along belts, etc.). In short, the Durometer value of an elastomer such as polyurethane also known as its Shore A hardness could affect many factors apart from simply being a measure of resistance. The role played by Shore A values can have particular importance in different applications:
- Light-Medium Duty Applications (11-30 Shore A): Delicate materials electronics or foodstuffs for example may necessitate the use of soft rollers products with high elasticity enabling them to deflect significantly (up to 80% indentation depth) upon loading – helping exert cushioning effects (like those spongy surfaces playground equipment that absorb shocks). To put this another way, imagine if you will one of these has a rating of 20 having a support weight of 20kg. Cardboard boxes as they travel along conveyor deflection might reach 8mm preventing any crushing-type damage from occurring. Brick-a-brack being gently sorted.
- Standard Conveyor Applications(30–50 Shore A): Here we are talking about harder-wearing items still with the ability to take some punishment medium resistance category products between 2010% again having payloads applied maintained within range efficiently over long periods. The slight bending (approximately 3-5 mm when a load of 100 kg is applied to a 50 Shore A roller) absorbs small knocks; the greater hardness provides improved wear resistance compared with softer alternatives. Heavy Duty
- Conveyor Applications (51-70 Shore A): When things get tough, hard rollers (51-70 Shore A) get going. These bad boys are designed for super rough conveyors moving highly abrasive materials such as rocks (crushed rock can have a compressive strength of over 100 MPa), scrap metal (steel’s yield strength is around 250 MPa), or building waste (concrete’s compressive strength can exceed 40 MPa). With minimal bending (indentation depth under 20%, even at high loads) there is very little wear. However, you do need to consider what you’re moving along them: Some goods might get damaged by really hard rollers.
- High-Temperature Applications (Shore A Hardness And Heat Resistance Both Matter): Temperature adds another twist. Normal rubber compounds can soften when it gets hot – this affects their Shore A hardness and could mean conveyor rollers don’t perform as well as expected for as long as they should. For heat up to 150°C, we have rollers made from special heat-resistant compounds here at Tehnoguma. They keep their nominated Shore A hardness even when it’s extremely hot: which means they last well under tough conditions and don’t wear out prematurely just because things get warm. Picture a conveyor in a factory oven running at 120°C while carrying metal parts along a standard rubber 60 Shore A roller might start to soften up a bit – making it less resistant to wear. In this specific application, Tehnoguma’s 60 Shore A roller that is resistant to heat will keep working just as it always has.
- Impact Applications (A Multi-Faceted Approach): When considering impact resistance from different angles you might need more than hardness measurement alone if working within a high-impact environment. In those cases we have rollers with special core designs available – like ones made out of steel or reinforced nylon – which are better able to take knocks and keep on turning; they stay whole when others might break. Moreover, there is also the option of using shock-absorbing materials in rollers’ covers: meaning things can be dropped onto them from a great height without sustained damage.
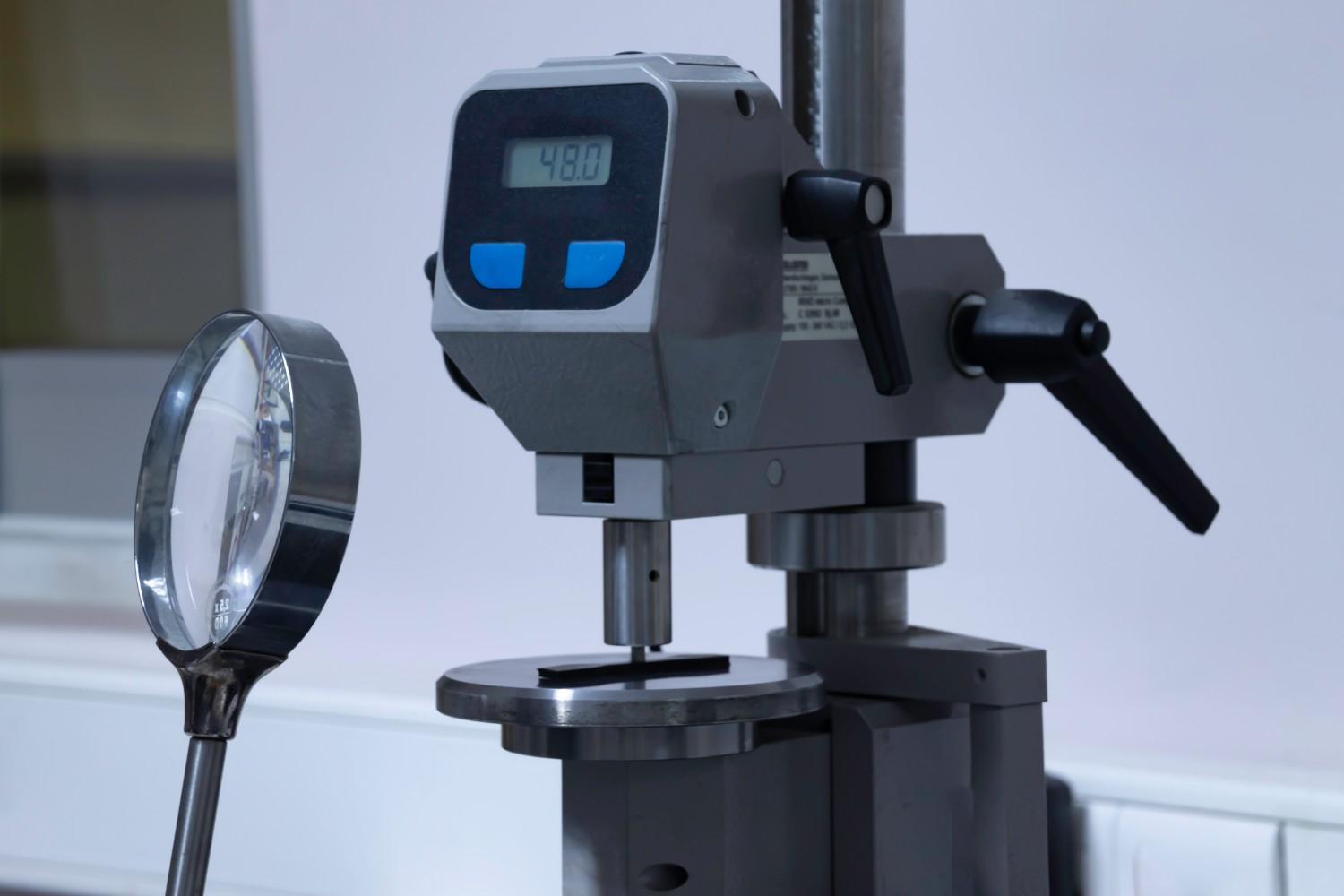
Common Types To Choose From
If you need help to choose the best rollers for your needs, talk to our experts. We will consider many factors–such as how hard the rollers need to be (Shore A), their size, and how fast they need to go. Also important: what materials you are moving with them, plus any special environmental concerns. Tehnoguma has all kinds of rubber for rollers; here is some information about different types:
- Gravity Roller Conveyors: For medium loads these light-duty conveyors are perfect.
- Powered Roller Conveyors: If you need to move something quickly these are great.
- Conveyor Belt Idlers: These rollers support belt conveyors when they have a heavy load on them.
- Specialty Rollers: Choose from models that work well in very hot or cold temperatures and make less noise while working -–even some that have a lot of impact every day.
By understanding how all these things work together with hardness, clients can buy products that offer:
- Performance: Working ‘right’ in this case means being able to cope under pressure, deal with knocks without marking things, and lasting well.
- Less Downtime: Pick the correct items then there is less risk of them wearing out/breaking so often. This keeps costs down and helps firms meet deadlines.
- Efficiency: If loads move smoothly and steadily throughout the system then everything works better; firms can sometimes do more jobs in a period.
Incorrectly specified rollers may mean things don’t move as efficiently as possible–don’t let this happen! We suggest that you go over our previous articles on Industrial Rubber Rollers: Know their Role and Procedures and Conveyor Belt Maintenance Tips: Revamp Efficiency & Lifespan for more insights on the topic.
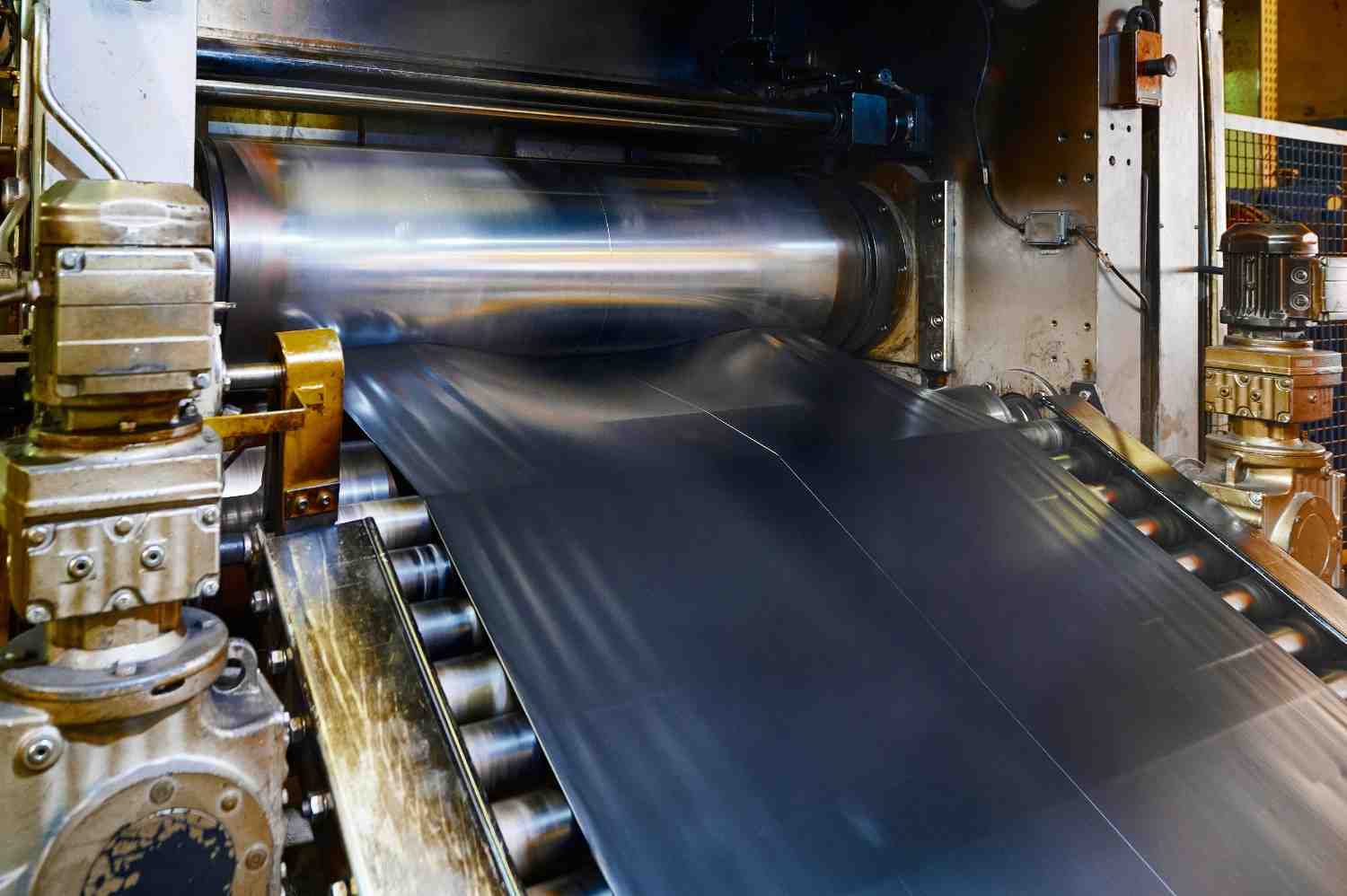
Conclusion
In the fast-moving world of material handling, choosing the correct rubber for the right industrial roller hardness can seem like a high-stakes game. But don’t worry! Once you grasp the science behind Shore A hardness, you can choose rollers that combat wear and tear with ease–absorbing impacts well too. Operations will run more smoothly overall. Of course, Shore A is only part of the story.
This is why our experts on rollers are here at Tehnoguma: They’ll help guide customers through every stage from selection onwards; taking into account factors such as diameter speed plus which substances you’re working with. Always stay tuned to our news section on industrial rubber – so there’s no need to remain confused about rollers any longer: Start enjoying better performance today and get in touch with us.