The key to the success of aerospace missions is precision. Whether it’s a lunar lander gently lowering itself onto the surface or a fighter jet performing an intricate high-speed maneuver, every element must work perfectly–and within minuscule margins. This is where custom polyurethane parts come in. These components may be tiny but they play a big role in making sure that an aircraft’s systems run smoothly and reliably. If you are an aerospace engineer, work in a research-and-development department, or have responsibility for buying equipment used by pilots, this article is for you. We want to explain how using tailor-made polyurethane components could give your organization an edge.
No matter what industry of interest you come from at Tehnoguma you can find industrial rubber products and services for various purposes mining industry, food production, ergonomics technologies, roller technologies, and more. proceed reading so you get into details.
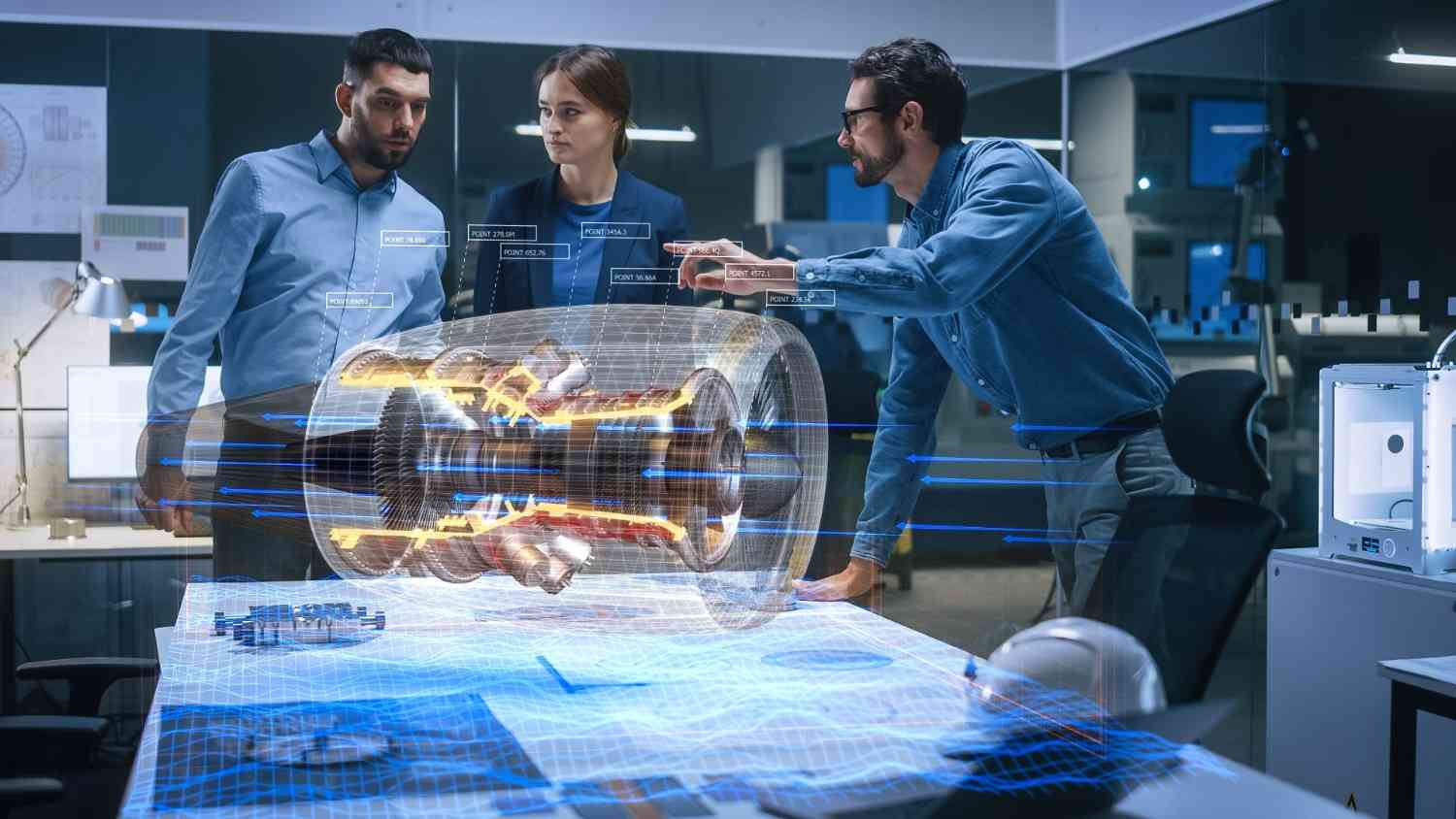
Polyurethane Custom Parts Precision – The Heart of Aerospace Engineering
Picture this — a fighter jet is trying to land on a carrier deck that’s as big as a football field. The deck is being hit by wind and waves. For the jet to land safely, thousands of different parts need to work perfectly. And by perfectly, we mean they have to do their job exactly right, even if it’s just by a hair’s width. This quest for accuracy isn’t just important for aerospace engineering; it’s what keeps it alive.
Precision: The Invisible Architect of Flight
If you want systems that work every time, you need components built with extreme precision. Don’t believe us? Check out these examples:
- Landing Gear: These bad boys have to take a lot of pressure when planes touch down. If their shape or structure is slightly off, things can go very wrong, very quickly
- Flight Control Systems: Pilots steer planes using pedals and two control sticks. But they’re not physically connected to the aircraft’s wings or tail. Instead, they’re sending signals that move things based on how far and how often they push or pull. For this system to function safely (let alone work at all), each part must enable exactly the right kind of movement — no more, no less.
- Fuel Systems: Imagine something going haywire while an airplane is zipping through the sky. A loose cap, break/hole along the line, sticky valve… any of these issues could cause the aircraft to malfunction or fall out of the heavens altogether.
The Enemy of Precision: A Delicate Balancing Act
It is no small task to achieve such precision in aerospace engineering, where professionals must continuously fend off a host of foes:
- Microscopic Deviations: Tiny differences: If dimensions or materials vary even slightly from one part to another, forces may not balance properly – with serious consequences for components in aircraft or spacecraft.
- Thermal Expansion and Contraction: When things heat up they get bigger, cool down and they contract. Imagine what this does during an airplane flight to bits of metal bolted together.
- Vibration and Fatigue: All objects vibrate a bit all the time when moving — but too much stress from regular shaking makes them tired (just like you after a long walk!). If parts such as wings or engines become worn out it could end in disaster and there is a constant battle against them by engineers working in the field.
This helps explain why high-tech materials like custom polyurethane parts are so important for building things like planes that need to work perfectly.
You can check out our article on Custom Rubber Bushings: A Versatile Solution for Industrial Needs and see how wide application they have.
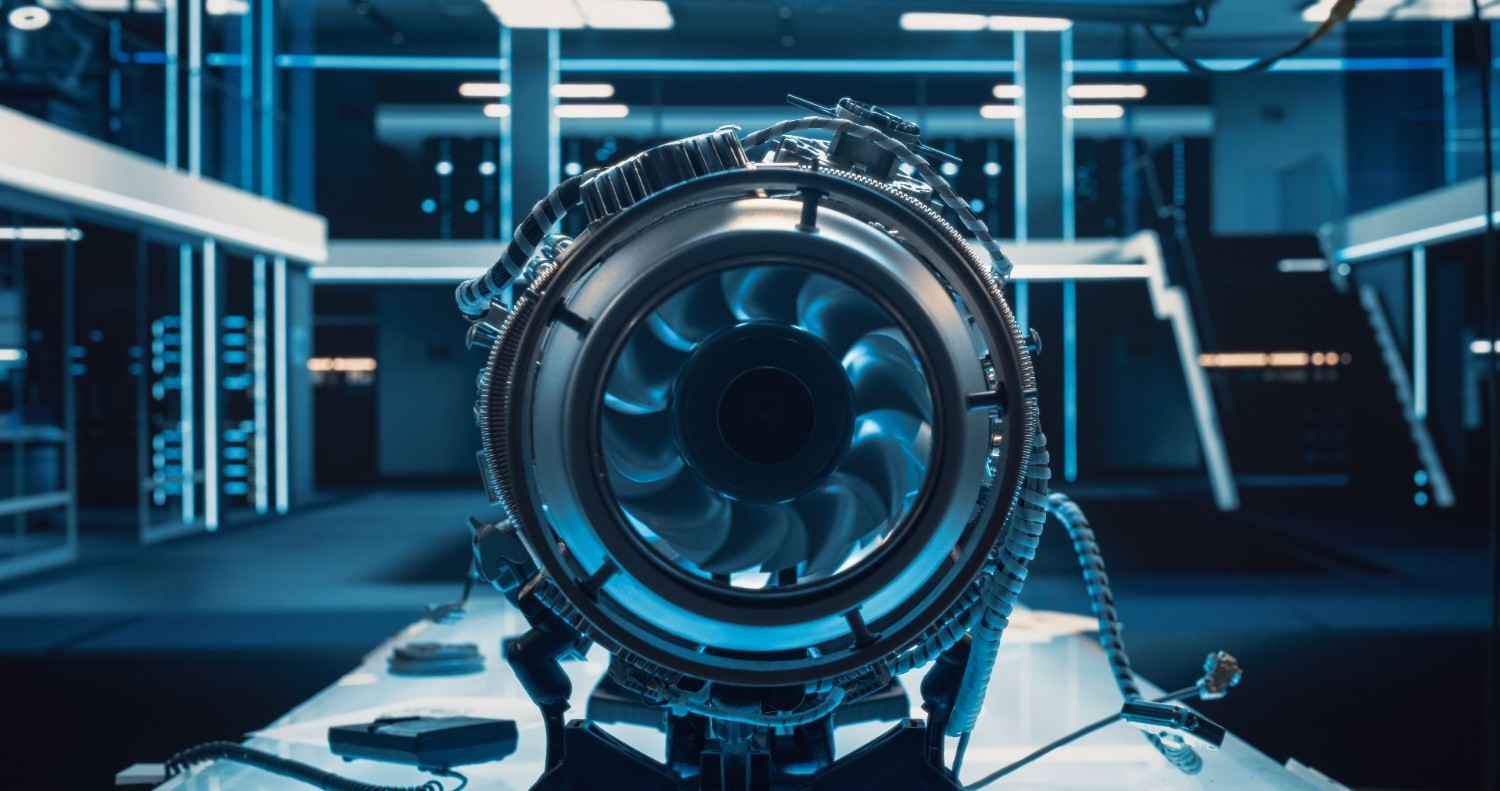
Polyurethane Custom Parts: The Rising Star in Aerospace Materials
For plastics, polyurethane is anything but ordinary. These polymers have a range of special qualities that make them perfect for many aerospace applications–and engineers are taking note. Imagine a material that is:
Strong Yet Lightweight
In some cases, polyurethanes can be stronger for their weight than materials like aluminum–which means lighter aircraft components that do not sacrifice performance.
In one study Airbus did in 2022, using polyurethane composites rather than traditional aluminum ones for specific airframe elements led to a 20% reduction in weight.
An Abrasion Warrior
Areas such as ducting systems and landing gear get a lot of use–and can wear out faster. One thing polyurethane is known for is resisting abrasion (that is: being rubbed so much it wears away).
According to one industry estimate, using these materials could triple the lifespan of some landing gear components.
Unfazed by Extremes
From scorching high-altitude flights (reaching -70°C) to the frigid vacuum of space (-270°C), polyurethane maintains its integrity.
Whether it is being used thousands of feet up in the sky (where it can get very cold) or sent into orbit (where temperatures plunge) aerospace engineers need to know their materials will work as expected. Polyurethane does: even Boeing has been impressed after testing how well it withstands deep-freeze conditions during spaceflight simulation.
A Chemical Fortress
Jet fuel, and hydraulic fluids — these harsh chemicals pose a threat to component performance. Polyurethane’s resistance to such chemicals minimizes degradation. This means that seals, gaskets, and fuel lines last longer. One NASA study from 2023 suggests using polyurethane composites in fuel lines because they withstand jet fuel better.
Flexible with Durability
Polyurethane is more flexible than some rigid metals — a useful quality. This flex helps parts like seating and wing components absorb vibrations and impacts (when something hits them).
In aerospace, flexibility plus durability make polyurethane great for many applications. Even engine mounts!
Additional Considerations
Rigid foams, flexible foams, elastomers, coatings – polyurethane comes in lots of forms so you can use it all over an aircraft — from its tail to tip!
All materials used in planes must meet strict flammability standards; poly resins do. And now there’s interest in sustainable products too. New bio-based polyols mean manufacturers rely less on petroleum feedstocks.
Emerging Applications
- Acoustic Insulation: Polyurethane is great at absorbing sound waves. This makes it useful for reducing noise inside cabins – helping passengers to have a more pleasant flight.
- Radome Applications: Polyurethanes that let radar signals through (radar-transparent) have enabled designers to develop radomes that are more aerodynamic and weigh less than those made from older materials.
Advancements of Custom Polyurethane Parts in Aerospace
Ongoing research and development are expanding the potential uses for polyurethane in aerospace — with new formulations poised to play an even larger role. For example:
- Self-healing properties: Scientists now are designing polyurethanes that repair small cracks or abrasions; aircraft coatings made from them might mean fewer dings to buff out on the flight line.
- Recyclability: Tomorrow’s polyurethanes could be more readily recycled than today’s, a plus for sustainability efforts.
As further discoveries unlock this versatile substance’s full capabilities (in many industries), there will almost certainly be spinoff benefits and spinoff jobs.
Standing Out from the Crowd: Polyurethane vs. Traditional Materials
When compared to traditional materials such as metals and other polymers, polyurethane has several advantages:
- Lighter than Metals: Metal is heavy–this is its strength. But polyurethane can be just as strong as metal while weighing much less. This is good news for things such as aircraft: not only do they become more fuel-efficient when made from lighter materials; but overall performance also improves.
- Outperforming Other Polymers: Some polymers may struggle to withstand very hot or very cold temperatures, or being exposed to certain chemicals. Nylon is one example used within aerospace engineering for its lightweight properties – although there are times when engineers find it lacking. Polyurethanes have greater flexibility there plus they are robust against lots of different solvents too.
In the following sections, we take a closer look at custom-made polyurethane parts: how these components are created, and explore some exciting examples that could help shape the future direction of aerospace design.
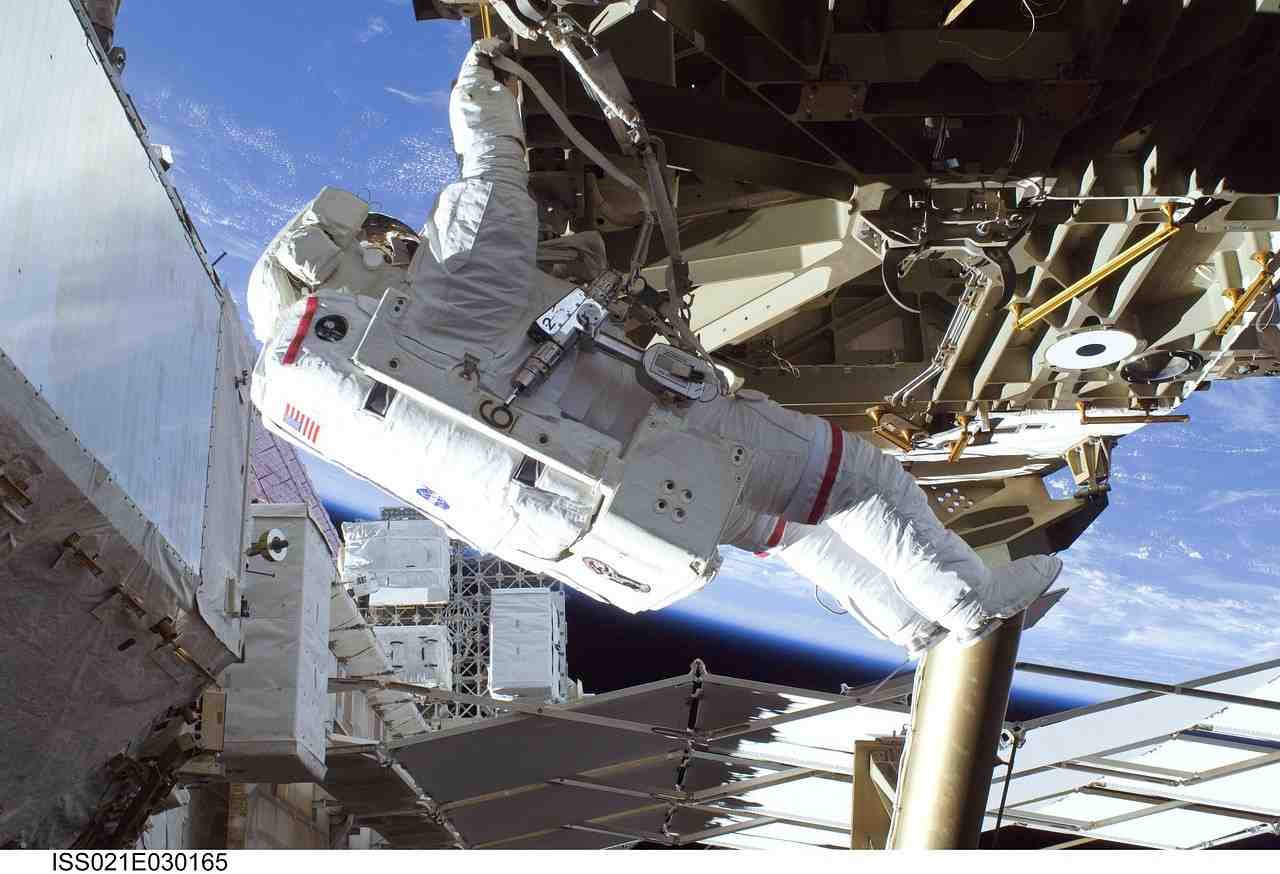
Custom Polyurethane Parts – Building on Precision, One Part at a Time
When engineers and scientists team up to make aviation parts better, they turn to the power of polyurethane customization. Here’s an inside look at how things get done:
The Tailored Approach: The Customization Journey
Converting raw polyurethane into a mission-critical component is no simple task:
- Design Collaboration: Aerospace engineers determine what the part needs to do, how much weight it must carry, and the kind of conditions it will face. Material scientists then work out how to give the polyurethane exactly the right properties by creating a tailor-made mix.
- Prototyping for Perfection: Initial models of the new part can be made using 3D printing or similar techniques. These prototypes are then tested very thoroughly to find out if they are good enough both structurally and performance-wise.
- Testing the Limits: Custom polyurethane components undergo an array of tests to make sure they will perform when fitted to an aircraft & exposed to real aerospace conditions. Tests include seeing how far you can stretch or squash something without it snapping (stress-strain analysis) plus checks inside special chambers that can simulate sunshine, rain, wind, and cold temperatures.
The Art of Design: Factors Shaping Custom Parts
Designing each polyurethane component involves considering several important factors:
- Load-Bearing Capacity: It’s vital that every part can cope with particular weights or pressures. To meet these requirements, engineers carefully devise both the part’s geometry and the type of polyurethane it will be made from.
- Thermal Stability: As previously mentioned, properties that don’t alter much even when things get very hot or cold are needed; along with other ingredients special blends are sometimes selected by materials scientists so their performance across a wide temperature range can be optimized for its intended use.
- Environmental Resistance: Exposure to chemicals, UV radiation, or even fluids like hydraulic oil is factored into the design. Selecting the appropriate polyurethane formulation ensures the part maintains its integrity throughout its service life.
Beyond Theory: Examples of Custom Polyurethane Parts in Action
Custom polyurethane parts are used on aircraft because they can do so much:
- Seals: These seals don’t leak. They stop oil and other liquids from getting out where they shouldn’t be between important bits of machinery. By doing this, custom seals help systems work properly without wearing out too soon.
- Bushings: Metal parts need protecting so they don’t get damaged when aircraft vibrate as they fly through the air. Bushings made of polyurethane absorb these vibrations. They also stop separate parts rubbing together all the time (which would make them wear out quickly).
- Gaskets: When two surfaces that meet each other closely need to be sealed together–but still able to move very slightly–gaskets do a great job. Custom gaskets of this type made from polyurethane prevent fluid leaks under pressure in lots of different systems within aerospace vehicles.
Engineers love using custom-made polyurethane components in airplanes and helicopters because it enables them to work better than ever before. Customization means designing and making things exactly how you want them to be: with this material, they can achieve an amazing level of accuracy. In our next section, we’ll investigate some specific properties of polyurethane — and show how these lend themselves to aerospace applications.
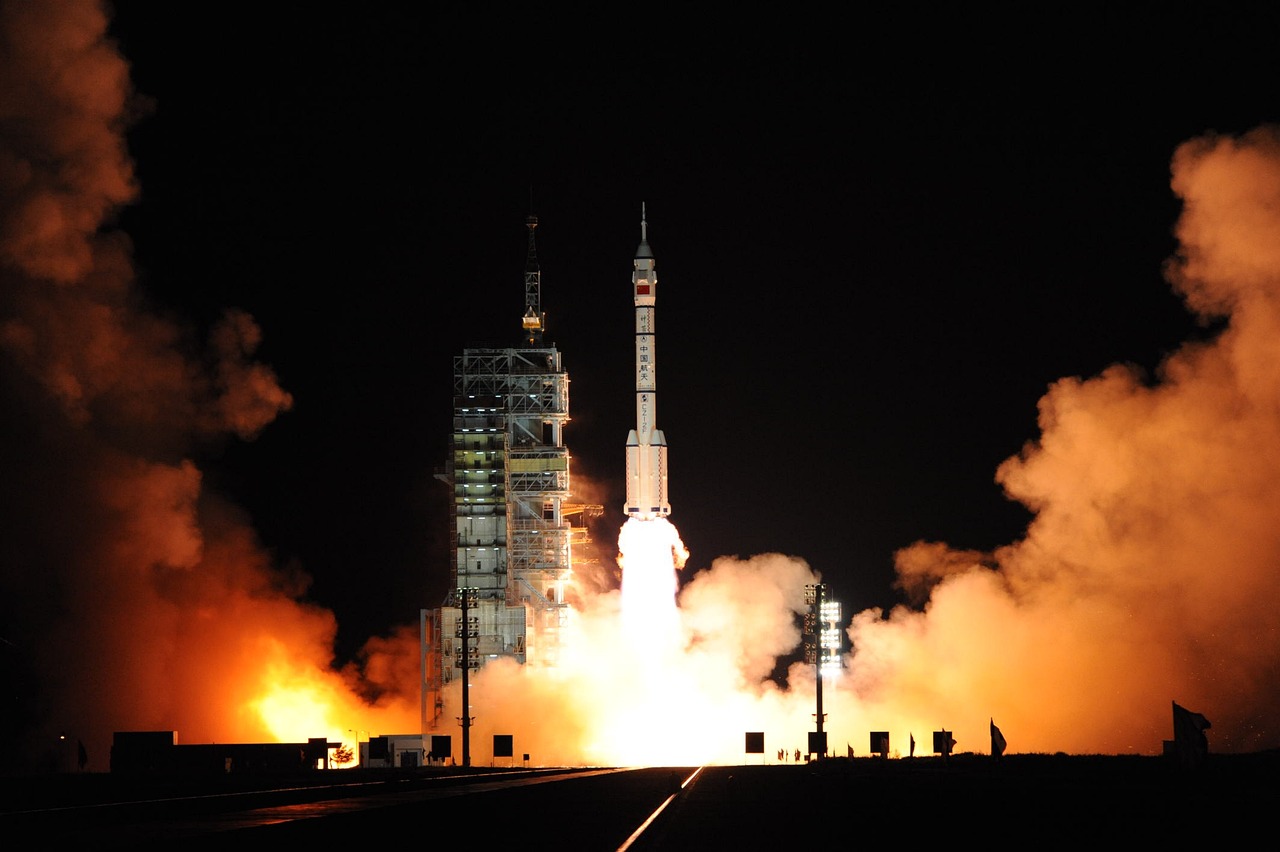
Custom Polyurethane Parts: Tailored Properties for Aerospace
When it comes to custom polyurethane parts, the key is more than just creating something unique — it’s being able to fine-tune material properties exactly. This is what makes them ideal for aerospace applications with specific challenges. In this article, we’ll look at these clever components in detail and explain some of the science: especially how their properties can be adjusted for individual requirements in the aerospace sector.
The Mechanical Muscle: Strength, Elasticity, and Hardness – Engineered for Flight
The “Mechanical Muscle”, part form this article discusses how Polyurethane can be created with different mechanical properties needed for aerospace engineering:
- Tensile Strength: Aluminium alloys are used to make some parts of airplanes – such as their landing gear. When these parts touch the ground they do so with great force. Engineers can make polyurethanes that cope with over 70 megapascals (MPa) of tensile strength; some aluminum alloys used in aerospace engineering cannot do better than this. By using these high-strength polyurethanes, manufacturers can produce components that must withstand intense forces upon landing while being comparatively lightweight.
- Elasticity: Polyurethanes are also flexible – a useful thing for materials on aircraft under vibration or stress. When researchers compared traditional metal bushes with polyurethane ones in tests simulating conditions on an airplane, they found that the plastic versions reduced transmission of movement by up to 80%. This means important kit aboard planes (for example sensitive electronics) lasts longer because it does not move around so much.
- Hardness: One type of new material might feel soft like rubber while another could be rock hard. There are many possible formulations in between: designers pick those that best suit their needs. To illustrate this point consider two hypothetical components both made from polyurethane: a seal for the pipe valve that stops fluid leakage and a track along which the wing slides in and out.
Thermal Stability: Conquering the Extremes of Flight
Traditional materials can struggle in the tough thermal conditions of aerospace travel. Polyurethane is not one of these materials:
- High-Altitude Performance: Temperatures on a typical flight can drop to a numbing -80°C. However, polyurethanes designed to remain flexible at low temperatures stay supple and operational under these extreme conditions. This is vital for critical flight control systems such as rudders and ailerons – and means they work equally well at high altitudes.
- Heat Dissipation: Some parts of an aircraft can become very hot; engine mounts, for example. Polyurethane formulations with a good ability to conduct heat can help here by shifting warmth away from sensitive areas.
Data from Airbus indicates that polyurethane mounts may have around 30% better thermal conductivity than traditional rubber ones. This can mean lower temperatures for crucial engine components while on duty — so they do not overheat.
Chemical Resistance: Unfazed by Harsh Aerospace Fluids
Exposure to jet fuel, hydraulic fluids, and de-icing fluids is common for many aerospace parts. Polyurethane provides outstanding resistance to these substances
- Fuel Resistance: Some materials break down when exposed to jet fuel for long periods – but not polyurethane. With specially formulated types of polyurethane, seals, and gaskets in contact with fuel can remain unchanged (in terms of swelling or mechanical properties) after extended use. This helps keep aircraft fuel systems working as they should be!
- Hydraulic Fluid Compatibility: Aircraft rely on hydraulic systems to move their wings and wheels. If leaks spring up in these essential control systems, there could be big trouble. One way to prevent such leaks is by using polyurethane components that work well with many types of hydraulic fluid; because they don’t break down easily, parts such as seals made from this material often outperform traditional alternatives by a factor of three or more say, industry experts.
Innovation Takes Flight: Advanced Polyurethane Formulations
Material science is continuously expanding the potential of polyurethane in aerospace applications:
- Flame Retardancy: Additives including halogenated compounds can be blended with polyurethanes to meet Federal Aviation Administration (FAA) FAR 25. 853 regulations for flame retardant materials–essential for many parts inside aircraft cabins and engine bays.
- Weight Reduction: As every aerospace engineer knows, cutting weight means boosting performance. New kinds of polyurethane are now being developed with micro-cellular structures; these could cut an item’s weight by 50% while providing mechanical properties similar to those currently used.
The Future of Flight: Polyurethane Soars to New Heights
Researchers are continuously discovering new potentials for polyurethane within the aerospace industry. They have found ways to create formulas that are even stronger compared to their weight than before, besides providing parts with self-healing capabilities so they last longer.
There is also ongoing work on giving the material conductive properties: Imagine custom polyurethane components that could be used to de-ice planes!
These advances mean there will be lots more scope ahead for using tailor-made polyurethane parts in aerospace projects – and we’ll investigate what some of these real-world applications look like in section two when we take off with them on board various missions.
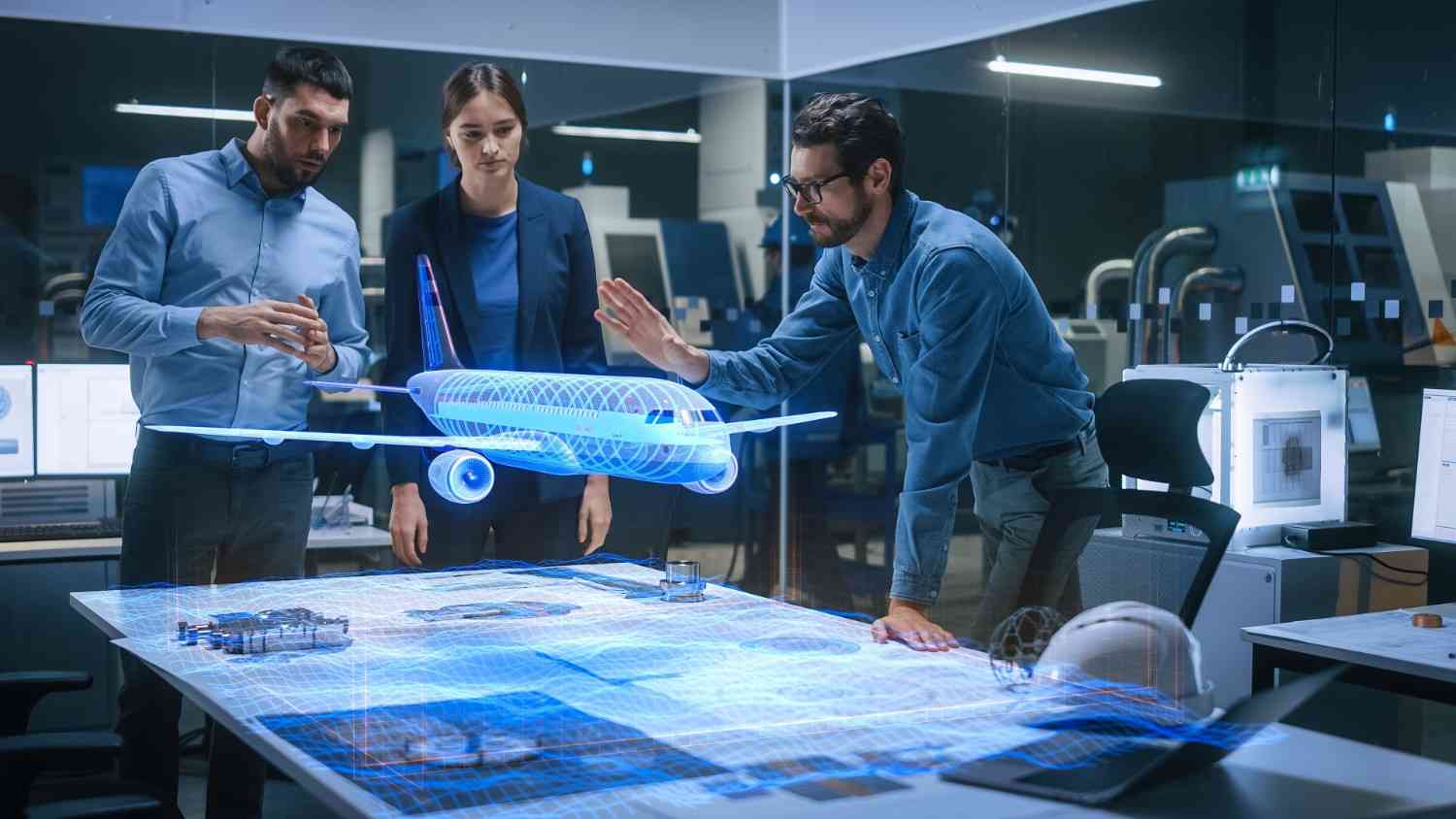
Taking Flight with Precision – Real-World Applications of Custom Polyurethane Parts
The distinctive properties of polyurethane aren’t just a talking point; they’re having a real impact on how we create aerospace components. Let’s take a look at some examples:
Landing Gear Bushings for a Commercial Aircraft
When a commercial plane lands, its landing gear takes an almighty hammering. Traditional metal bushings in the landing gear also take a battering – but if we replace these with custom-made polyurethane bushings, they last much longer (which saves money on maintenance).
That’s because our specially formulated polyurethane has both high tensile strength (75 MPa) and elasticity: when you combine these two factors, you get a material that absorbs forces very efficiently indeed – and therefore doesn’t transmit so much stress into the aircraft’s structure.
Results:
- 3x Increase in Lifespan: Lifespan triples with polyurethane bushings vs. conventional metal bushings — essential maintenance downtime drops sharply, and replacement costs fall significantly.
- Improved Vibration Dampening: 70% less vibrations are felt when using polyurethane instead of metal bushings. Think about it: Not only will your passengers enjoy a smoother ride but all those delicate instruments aboard will have less wear and tear to cope with!
Beyond Bushings: A Universe of Applications
Custom polyurethane parts have a wide range of uses in aerospace:
- Seals: Whether they are keeping lubricants in or dirt out, polyurethane seals are custom-engineered to perform under extreme conditions.
- Gaskets: To maintain the right amount of pressure in hydraulic and pneumatic systems, custom polyurethane gaskets provide a flexible yet secure seal between two surfaces that mate.
- Composite Tooling: Polyurethane tooling is both tough and light making it ideal when complex composite parts for aircraft need to be made quickly.
All this and more: Because they can be made to be lightweight, reduce noise, and increase safety and efficiency there is almost no end to how these parts can be used in space — sorry, we mean aerospace!
Performance Metrics: Quantifying the Benefits
The advantages of custom polyurethane parts are easily measurable:
- Longevity: Research shows that in many aerospace uses, polyurethane lasts 2-5 times longer than usual materials. This means huge savings over an aircraft’s lifespan.
- Reduced Maintenance: If parts don’t need replacing as often because of wear and tear, maintenance timetables can be more efficient. Aircraft can then spend more time in the air–being used for what they are supposed to do!
- Weight Reduction: Making things out of lightweight polyurethane can also help to make aircraft lighter overall. This means they need less fuel and/or can carry more payload (passengers, bombs, etc).
Aerospace manufacturers have found that by using custom polyurethane parts they can build better-performing aircraft which cost less to run. They get new ideas from seeing how existing planes and rockets perform when made from this super material. In our final section, we will summarise all these points–plus say why wouldn’t you try it on your next project! If you want to know more about Polyurethane and its applications, you can read Polyurethane Applications: Exploring Advantages and Common Uses
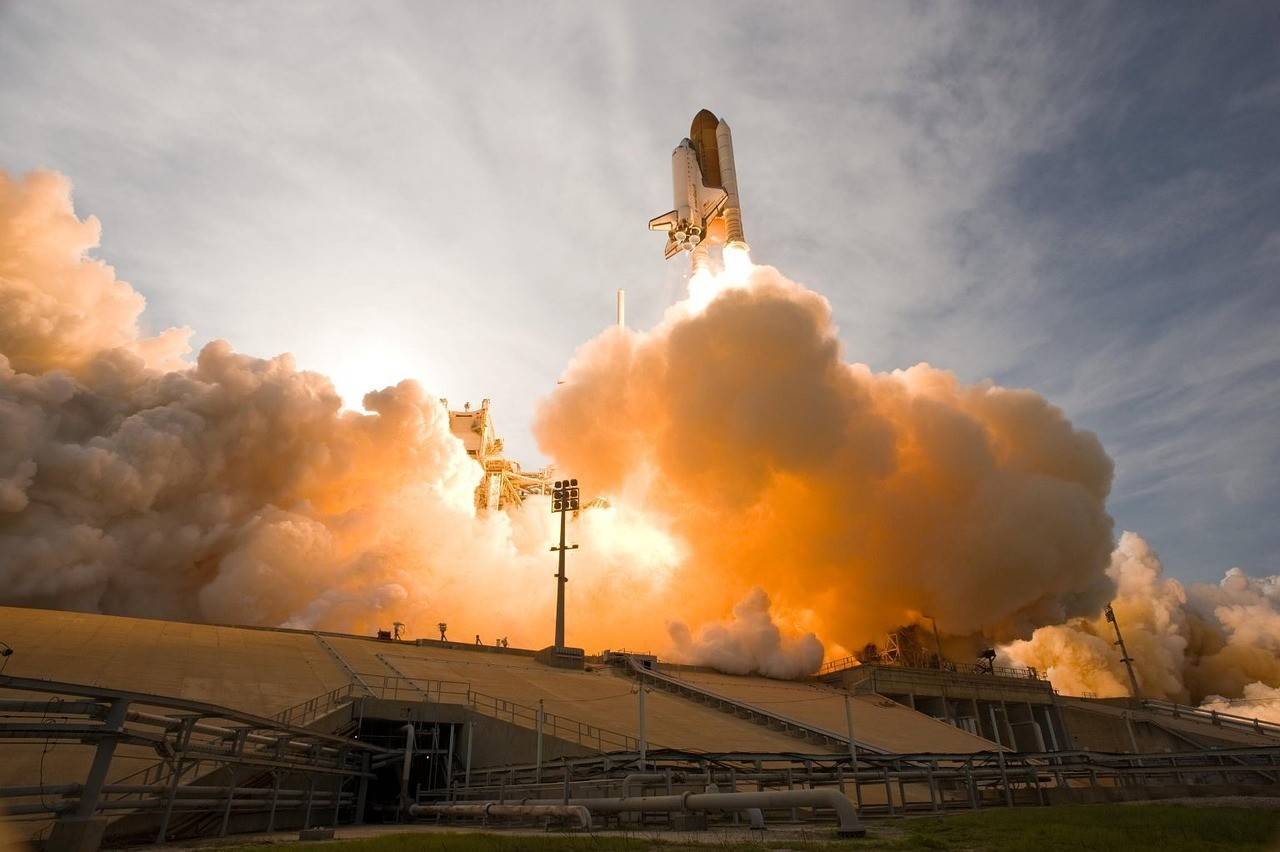
Soaring High on Savings – Economic and Operational Advantages of Polyurethane
Custom polyurethane parts hold an appeal that goes beyond their impressive technical attributes; let’s explore the economic benefits to aerospace manufacturers.
Cost Efficiency: A Long-Term Investment
While at first glance these bespoke components may have a higher initial purchase price compared with standard alternatives, closer inspection shows they offer excellent value for money over time:
- Reduced Maintenance & Replacement Costs: Because polyurethane is so durable, fewer repairs are needed when its parts break down – saving both time on maintenance AND money for replacements. Studies show there may be up to a 40% cost saving over an item’s lifetime compared with things made from standard materials. Take another look at those costs though!
- Life Cycle Cost Analysis: Analysis factors in all expenses related to an object from purchase through use/maintenance ending disposal. When you do the math custom polyurethanes often come out ahead once again: You can own something nicer for less money overall.
Operational Reliability: Taking Flight with Confidence
In aerospace, being safe and reliable is everything. Polyurethane can help make aircraft even more dependable:
- Enhanced Component Reliability: Because polyurethane is good at standing up to rough chemicals and general wear and tear, using it means that things on planes are less likely to break while they’re up in the air–which of course makes them safer.
- Preventing Hydraulic System Failure: One company that makes commercial planes had an issue where the seal around an important hydraulic system kept failing because it couldn’t cope with the hydraulic fluid. When they swapped this seal for a specially designed polyurethane one, there were no more failures: meaning not only did they improve how often their planes worked but also stopped lots of passengers from having accidents.
Sustainability: A Commitment to the Future
The aerospace sector is placing more and more emphasis on being green. Polyurethanes provide a sustainable edge:
- Durable Materials, Less Waste: The longer something made of polyurethane is, the less often it needs to be replaced – cutting the amount of waste produced. This means that using these plastics leaves a smaller environmental footprint from aerospace activities than it would otherwise.
- Recycling Potential: Work is ongoing to develop ways of recycling items once they reach the end of their useful life — although this is at an early stage, progress is being made with some components. If successful, future manufacturing could become more of a closed-loop system if these possibilities are realized.
Conclusion
Aerospace engineering’s precision has been revolutionized by custom polyurethane parts. These components are vital for the flawless operation of crucial aircraft parts because of their exceptional features–the ability to be precisely tailored, dimensional stability, and resistance to extremes of temperature.
Polyurethane enables systems including control mechanisms and landing gear to work better and more reliably than ever before. The financial and environmental cases for using them are also strong: equipment lasts longer with less maintenance; when it is no longer needed, it may be possible to recycle it. For custom-made polyurethanes, there is only one name you need to know: Tehnoguma. Contact the company today to find out more about its range of solutions — and start turning your aerospace ideas into reality!
If you want to dig even more get in touch with our customer support, You can get a quote and meet your requirements for the best results.