Anti static conveyor rollers are the inevitable standard for secure industrial settings. Consider this scenario – an innocent spark jumps from a doorknob–but now imagine if that tiny arc could ignite flammable liquids or gases surrounding you; things that burn or explode easily such as petrol, propane gas (LPG), or methane. The human body is an excellent conductor of electricity so it wouldn’t matter if the doorknob was metal or not. If there were enough flammable materials in the air, the result could be catastrophic.
Don’t worry though, there’s something in your corner! Anti static conveyor rollers and wristbands prevent build-up by leaking any charge away as soon as it starts to form – a bit like how all cars are earthed using special cables at petrol stations. In the same way, they also provide a way for any built-up static electricity to discharge harmlessly; you may have noticed these sparks when taking off a jumper in wintertime. But fear not!
We at Tehnoguma cover multiple domains such as mining industry, food production, ergonomics technologies, roller technologies, and more.
A new arrival stands ready to join the fight; one which doesn’t involve making workers wear straps or suits connected via wires to metal poles just for doing their jobs safely around substances waiting quietly to turn them into human firelighters. Let’s dive into the world of anti static conveyor rollers.
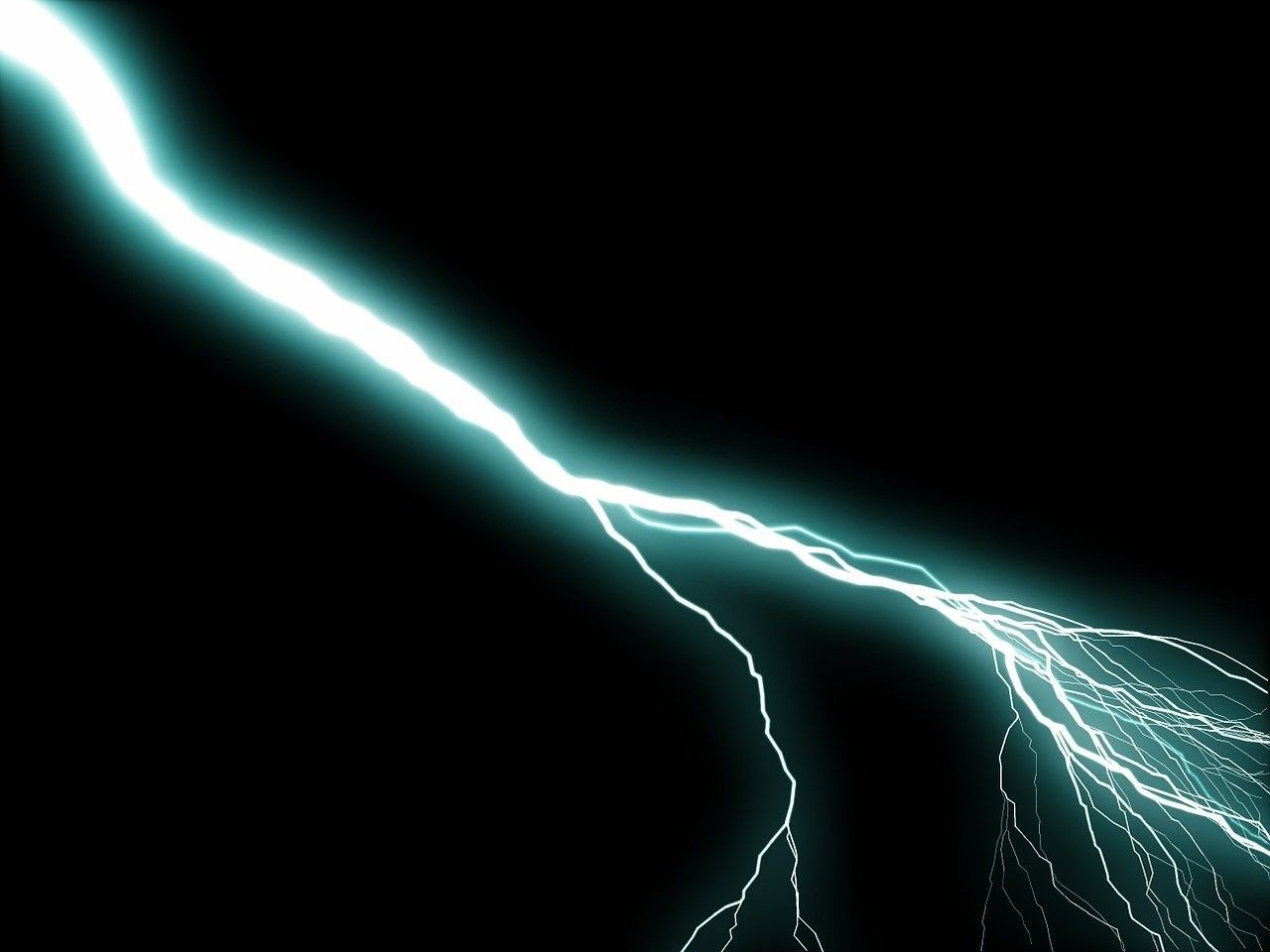
Static Electricity – The 3,000 Volt Menace in Flammable Material Handling
We all know how irritating static electricity can be. On a dry day, it’s what makes your clothes cling and gives you a tiny shock when you reach for a door handle. But did you realize this same phenomenon can deliver a whopping great spark measuring more than 3,000 volts? A spark that powerful is all it takes to start a fire or cause an explosion if you happen to be standing near flammable liquids, vapors, or dust when it discharges. A spark that powerful can set fire to a building or cause an explosion if it makes contact with flammable (able to burn) liquids, vapors (things that are gases at room temperature), or dust particles in the air.
How does it happen?
How come fluid rollers spinning round and round as clothes whiz down them don’t burst into flames? The answer lies in the principles of friction; which we all understand at least partially because even schoolchildren know you can generate a decent spark by rubbing things together. Static electricity doesn’t only build up when there are direct contact rubbers though. If two objects that have previously been in contact are separated charge separation can also occur. In fact, according to the National Fire Protection Association, static electricity is a major cause of fires in many different industries.
Static Electricity Scenarios
To gain a further understanding of how static electricity can pose a fire risk when dealing with flammable materials, consider this situation:
- Friction Frenzy: Picture conveyor belts whizzing along at over 100 meters per minute, continuously rubbing against things like plastic film (which doesn’t conduct electricity well) or textiles. This rubbing causes one surface to become negatively charged and the other positively charged creating static (a build-up of electrical charge). The Triboelectric Series ranks materials according to their ability to generate static electricity via this contact phenomenon; so if you know beforehand which pair will create more charge through friction alone, precautions can be taken. For instance, when non-conductive rubs up against conductive material such as steel there may be more than 20000 volts produced.
- No Contact, No Problem: It’s not just about two objects making contact and then separating -even pulling them apart can cause static electricity to be produced. If they do separate after being nearby, there is a good chance each will ‘steal’ some electrons from the other–leaving one with an overall negative charge and the opposite. How quickly surfaces are separated along with how much total area was in contact also has an effect: Slower partings of larger pieces of goods may result in higher voltages.
- Induction & Invisible Forces: Static charges have an uncanny habit of being able to jump or “arc” between two points even if they never actually touch each other! Should an item with an electric current running through it come near another object that is grounded (has no charge), then just by being close enough some of the charge might move across. Although these charges usually hang around for milliseconds, they could potentially cause a spark if conditions were right–say during periods of low humidity following a brisk walk across the floor mat.
So keep an eye out because while you can’t see static electricity buildup on the surface doesn’t mean it’s harmless. It may accumulate without being noticed from ordinary activities, and when it eventually does release — the results can be catastrophic. Enter anti static conveyor rollers: the final line of defense. But that is a tale for another day!
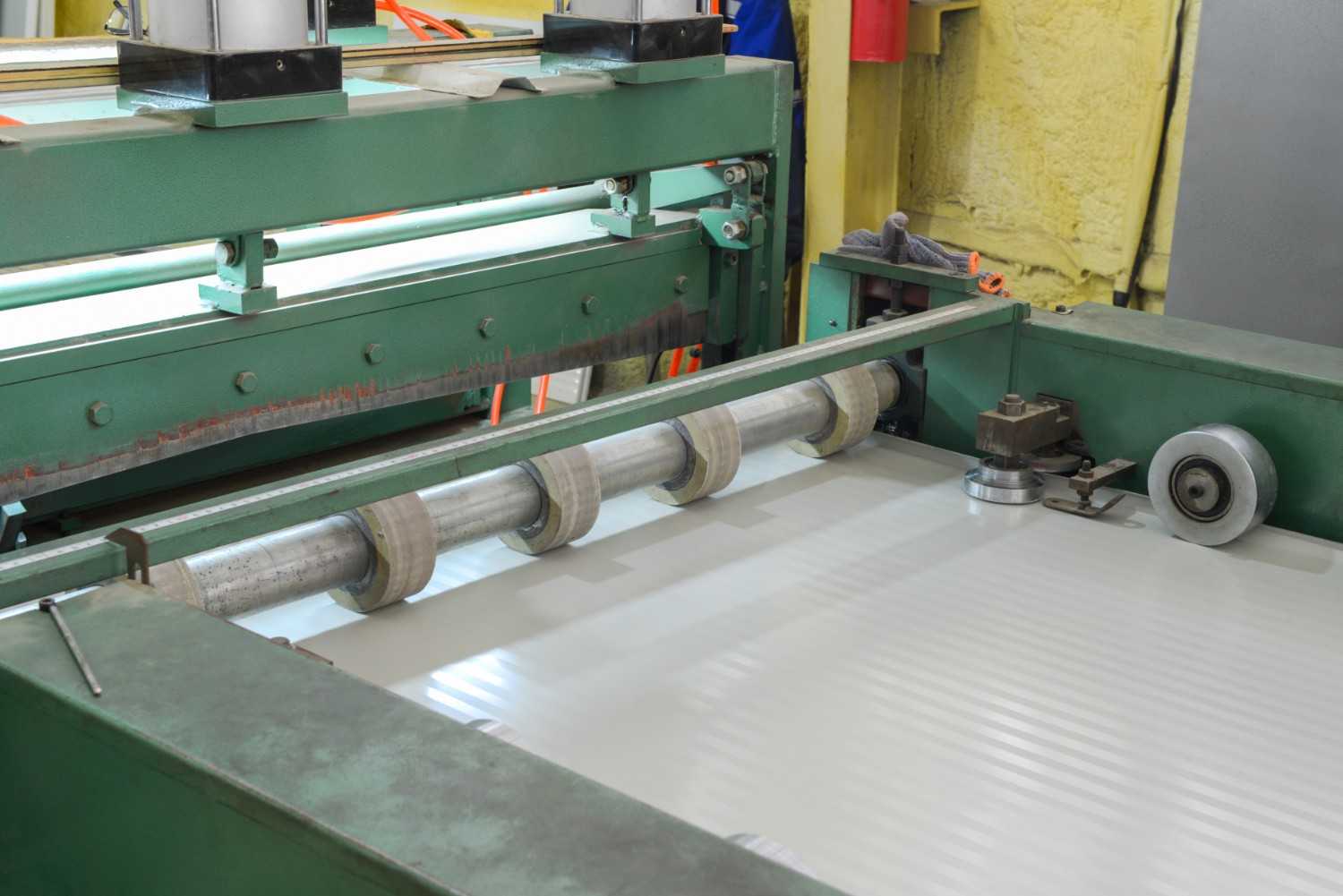
The Devastating Effects of Static Discharge in Handling Flammable Materials
Although you can’t see static electricity, you sure can see what happens when it makes contact with flammable materials. Anti static conveyor rollers battle this by conducting it safely. Here’s a closer look at just some dangers.
- Industries on the Edge: Regarding static electricity dangers, facilities that deal with flammable materials are right there on the front line. This includes industries such as those working with flammable liquids like petrol (gasoline), solvents; flammable gases (propane, natural gas), dusts that are generated during processes such as woodworking or grain processing—and any place else too! Handling these substances raises the possibility that a spark from static electricity could cause fire or explosion.
- Explosion Equation: A small spark might not seem like much but if it’s got lots of energy–as some sparks do things can go very wrong indeed. The fuel-air mixture has an incredibly low minimum ignition energy (MIE) when there is already a sparkly atmosphere. Taking as little more than one millijoule jump between two points at opposite ends side by side can set off such an explosion. A blast caused by this sort of spark will release between 10 and 100 mJs worth of energy. A personal note on explosions here: If they happen close enough their wavefront–or shockwave–may hit someone.
- Putting People In Peril: It’s a hazard to staff and building machinery. Static charges flowing through air give off heat light — we see it as sparks all the time. Domestic pets’ fur stands up if you give them petting a lot charge yourself. Very occasionally shocks may ignite synthetic clothing fabrics causing burns injuries either directly via current passing across/through the body or indirectly. Every material has its own ‘curtain temperature’ point where starts to burn independently sustained flames; humans typically need naked flame north of 600 C-plus to withstand several minutes yet house tent-made types of textiles will often flare up and melt within seconds of touching cigarette ash, etc.
All of this shows why effective methods for controlling static electricity are vital wherever flammable substances are being used/processed/stored/etc. Moving to anti static conveyor rollers discussed next paragraph turns out to be a particularly good way to prevent invisible foes from causing damage injury death by fire/explosion.
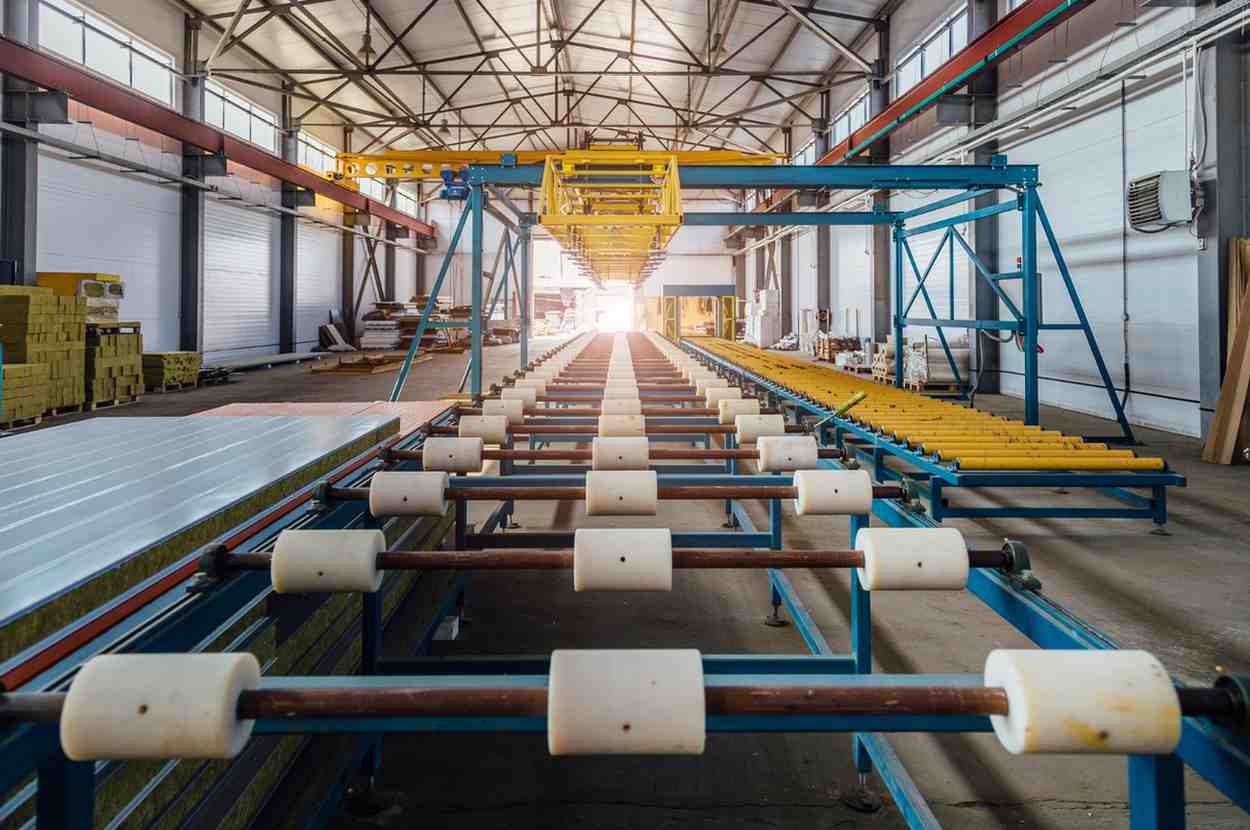
Prevention of Static Buildup by Anti Static Conveyor Rollers
We know that static electricity can cause fires when handling flammable materials. Enter anti static conveyor rollers–simple devices that stop this happening by making sure there’s no spark between the conveyor belt and what’s on it. Here’s how they work. Inside each roller are things that conduct electricity; let’s call them “conductive ingredients”. These little bits of material provide a pathway for an electric charge to flow. So when a charge builds up on the roller because it has rubbed against something and become charged, there’s a path through the roller itself for this charge to travel along. Its journey ends when it reaches the ground. Although both types do the same job overall, there are two sorts of anti-static rollers:
- Static-dissipative rollers: think of these as being like a river–albeit a very slow one! Their electrical resistance falls within the range of 10^6–10^9 ohms. This means that if there is a charge on them, over time it will gradually be dissipated.
- Conductive Rollers (CD): When you need an instant reaction, turn to conductive rollers. Their surface resistivity is less than 10^6 ohms–so they provide a quick route for static charges. The charges pass rapidly along the roller and go straight to earth: which makes CD rollers perfect for applications where there’s a lot of static around!
Next time you observe a conveyor belt moving items along, think about the hidden protectors that are hard at work below: The antistatic rollers. These little devices make sure nothing catches fire from the common spark of static electricity!
Advanced Considerations for Anti-Static Rollers
Anti-static rollers are essential for preventing static buildup and discharge in flammable material handling areas. To ensure these rollers work well and safely, you must also think about the following factors as well:
- Grounding: This often-forgotten aspect is vital for good static control. It helps to regard grounding as an off-ramp for static charges. Normally, a grounding cable or strap links each anti-static roller to some grounded point on the conveyor frame. It’s essential to check regularly that these connections are clean and secure so that any built-up static can escape. (Loose or corroded connections won’t do the job properly).
- Roller maintenance: Keeping everything shipshape Hero rollers do need looking after if they’re going to keep on top of static: Make sure their surfaces stay clean–dirt or grit could stop them working. Also, test surface resistivity from time to time: Instructions should tell you how often and what readings to look for.
- Environmental considerations: Why humidity levels matter We mentioned environmental factors briefly in part one but here we’ll go into more depth about one issue:
- Humidity: If there is a lot of moisture in the air this can cause problems with SD rollers because water conducts electricity quite well too! Consider using CD rollers instead of SD rollers in environments where static discharge speed is more important.
- Temperature: Fluctuations in temperature can also affect how well anti-static rollers work. Materials in the rollers might not conduct electricity the same way if it gets very hot or cold. Choosing rollers with the right temperature resistance for your environment helps make sure they do their job.
- Using a mix of roller types: Sometimes you may find a combination of SD and CD rollers works best. One example is if you put conductive rollers near places where static builds up, but have dissipative rollers everywhere else along the conveyor. This lets you target the problem areas — providing an overall solution.
If you think about all these things when deciding where to place them (as well as other factors like how fast charges need to be removed), then their ability to control static will be optimized for use with flammable materials: making anti static conveyor rollers coming as a safer and more efficient variant.
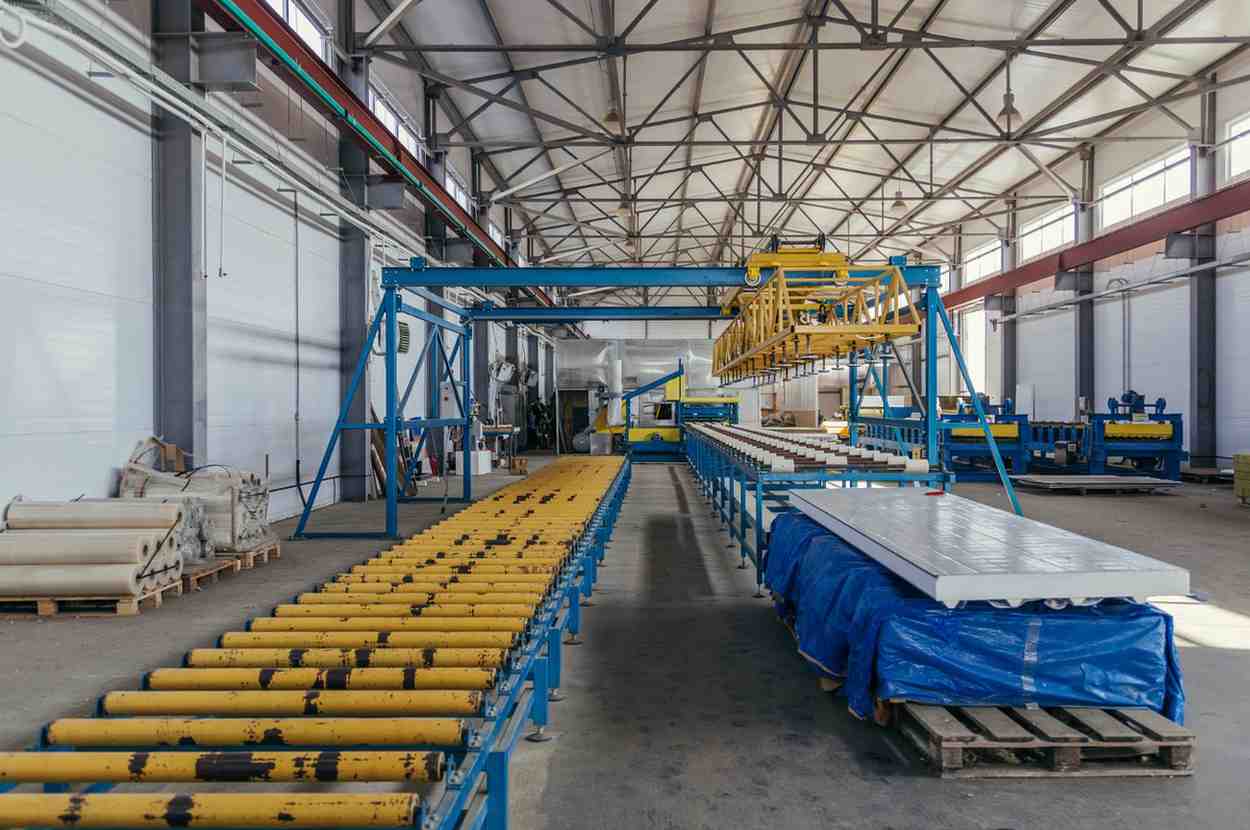
The Chain Reaction of Downtime: Why Proper Splicing Is Vital
In manufacturing’s fast lane, conveyors keep things moving. But if one stops working ─ even temporarily ─ the whole operation can grind to a halt. And that’s bad news for business! Let’s take a look at some numbers that show just how costly downtime from conveyor belt issues can be.
The Cost Of Downtime
A study conducted in 2020 for Manufacturing Engineering Magazine called “The True Cost of Downtime” makes sobering reading: an hour’s unplanned stoppage might set firms back anywhere between $10,000 and $75,000. Such sums illustrate not only the financial pressures faced by companies large and small when belts suddenly cease turning; they also hint at complexities within sectors such as automotive manufacture ─ where an hour-long hiatus along an assembly line could lead to vastly bigger losses than those seen after 60 minutes’ inactivity at a plant producing industrial sand alone. Nor are such impacts limited solely to immediate monetary concerns (though regular readers of this blog will be aware of how keenly we dislike those): because whenever production halts because of malfunctioning machinery there will probably follow costs associated with idle staff plus disgruntled clients who don’t receive orders when expected because something has gone wrong further up-stream–an aside.
The Cost Of Safety
In industries where safety is a top priority–such as mining or petrochemical processing–the repercussions of conveyor belt stoppages are magnified. It’s not just about the financial hit from lost production either; there could be safety hazards too, with dangerous outcomes. Take coal mines as an example. If a conveyor belt were to grind to a halt, then coal dust (which is known to cause respiratory problems) might hang in the air, putting miners’ health at risk.
Or if flammable substances like methane gas build-up because they haven’t been moved along, things could go bang–literally–if someone doesn’t act fast to shift them. Petrochemical firms face similar worries if belts carrying things like toxic chemicals or flammable liquid stop moving: you end up with a ticking time bomb. This is because it’s still possible for leaks or spills to take place, which may then put workers in danger and influence wildlife/ the surrounding landscape.
Such incidents can lead not only to fines being imposed but also to costly clean-up operations, as well as damage your standing within the industry. For tasks that need to be carried out swiftly when machinery has to be taken offline (such as belt repairs), it is therefore vital. Using methods that allow them to do a good job quickly — like modern splicing techniques combined with regular maintenance procedures designed to make wear-&-tear happen more slowly — is essential if such companies want both avoidable risks under control.
Effective Splicing: Your Weapon Against Downtime
If there is one thing companies can count on in the manufacturing industry, it’s that at some point their conveyor belts will break down. When this happens, a lot of time and money is lost–unless businesses have an effective splicing system in place. Splicing refers to the process of joining two pieces of belts together. By choosing the right method (mechanical for fast fixes, vulcanization for a more permanent solution) and making sure it is done properly with high-quality materials, firms can slash repair times and keep their belts running for longer stretches than would otherwise be possible. So it is paramount to have regular checks and implement the best standards to achieve effective splicing results for your machinery.
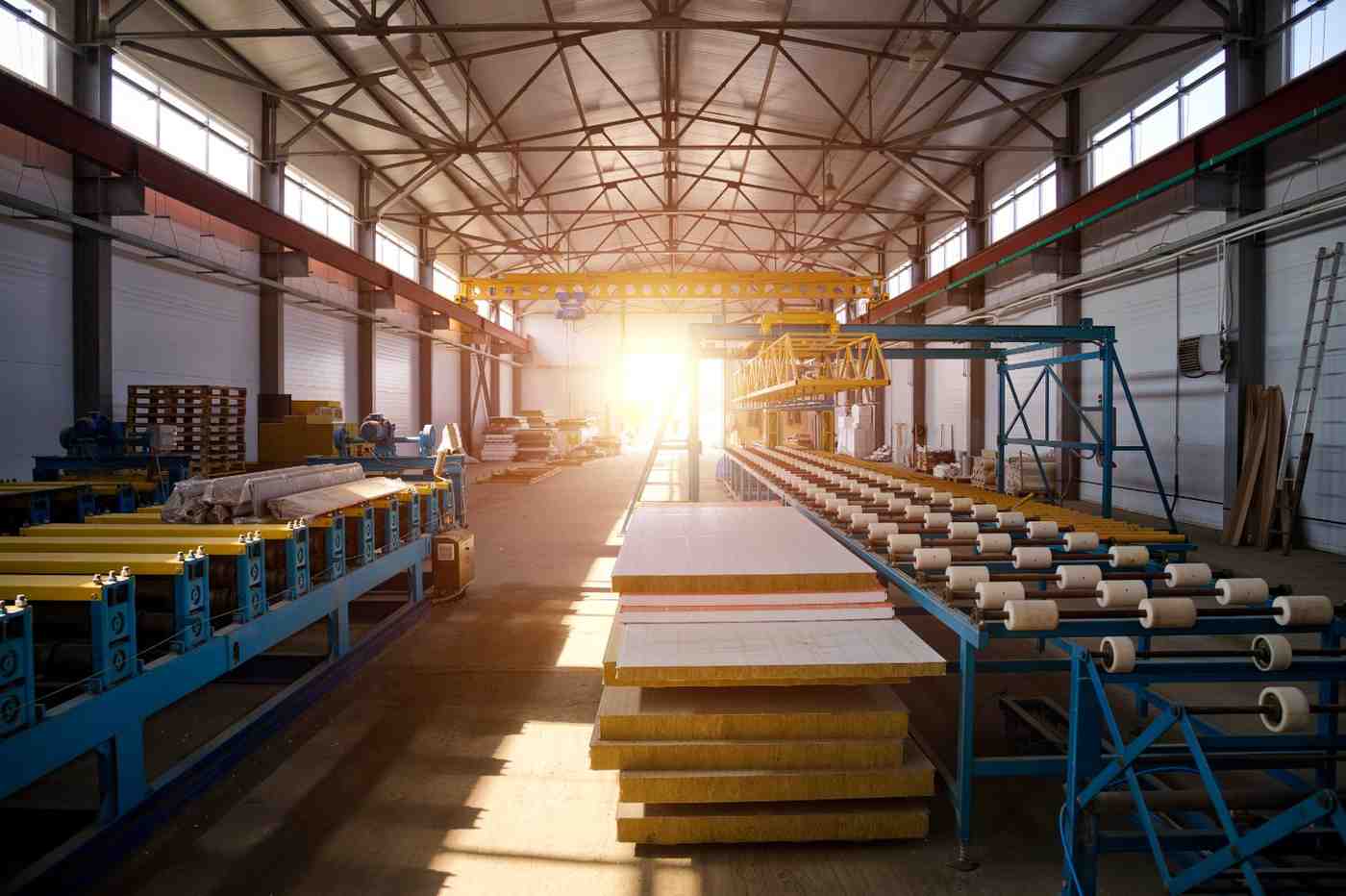
Advantages of Using Anti-Static Rollers in Handling Flammable Material
Incorporating anti-static rollers into your flammable material handling processes offers more than just a good return – it delivers numerous measurable pluses:
Boosted Safety Stats: A Numbers Game
In environments where flammable atmospheres can occur, discharges of static electricity have long been recognized as posing significant risks. According to figures from the National Fire Protection Association (NFPA), incidents that can be attributed to this phenomenon are a leading cause of fires across an array of industries. Static sparks have been recorded that carry more than 3,000 volts; all it takes to ignite substances with an energy level of 1 millijoule is three times less than this. However, by preventing the build-up and abrupt release of such charges, anti-static rollers radically diminish the chances of conflagrations and/or explosions taking place. This means not only creating a safer working environment but also one in which there may be fewer incidents that injure or kill employees.
Increased Productivity Levels: The Cost Of Downtime
Having to halt activities due to unexpected events will always have financial implications — but they can be particularly severe when fire and explosions cause unplanned-for stops. In addition to any refurbishment or replacement costs, there may also be lengthy interruptions in normal business practice whilst authorities investigate the incident(s) plus possible legal bills should people sue you claiming damages to their health from goods manufactured at your plant; if you have to pay compensation to workers who’ve been injured as well this soon mounts up.
Fire Damage Control: Heat Reduction
If a blaze did break out on an installation where flammable materials were being moved things could prove very expensive indeed. Anti-static rollers are a great investment if you want to manage risk effectively and get back more than you put in. This is because they stop awful things from happening that cost money – like when delicate materials get damaged by electricity! Stuff such as films and fabrics can be ruined by a single spark at just the wrong moment (if there is static in them). Using anti-static rollers reduces the chances of this occurring; meaning your goods will arrive in perfect condition, rather than being wasted due to punctures or tears.
Reduced Costs: A Penny Saved is a Penny Earned
While it may cost money upfront to use anti-static rollers, this is nothing compared with how much cash you might lose if there is a fire or explosion. Such incidents can lead not just to damage bills and having to replace equipment – they may also cause you to halt production, recall products, and face lawsuits from people who have been hurt. Investing in anti-static rollers is a good way of managing risk (or trying to make sure that accidents don’t happen) which should provide a return on investment many times over if their presence stops even one costly incident from taking place.
Material Protection: Safeguarding Your Valuables
Items such as film and fabric used in processes involving flammable materials can be harmed by static. Discharge of very high voltage electricity can make small holes in these products or tear them; this means not only that the goods will be wasted but also that more will have to be written off financially. Minimizing the build-up of static with anti-static rollers helps stop such damage from occurring, meaning valuable products reach their destination undamaged.
Compliance With Regulations: Staying On The Right Side Of Law
In lots of sectors, there are rules about how flammable substances should be dealt with. These regulations might come from bodies such as OSHA or NFPA and often say that precautions must be taken to prevent fires and protect workers from harm; including making sure items do not build up electric charge as standard rollers can cause them too.If you follow the guidelines you won’t get into trouble (or be fined for breaking the law); plus people will know exactly what needs doing which makes everything run more efficiently overall.
Taking all these factors on board when deciding whether or not to use anti-static rollers – which have many benefits over regular ones – could end up saving both cash (through avoiding accidents) as well having a positive effect on things like workflow.
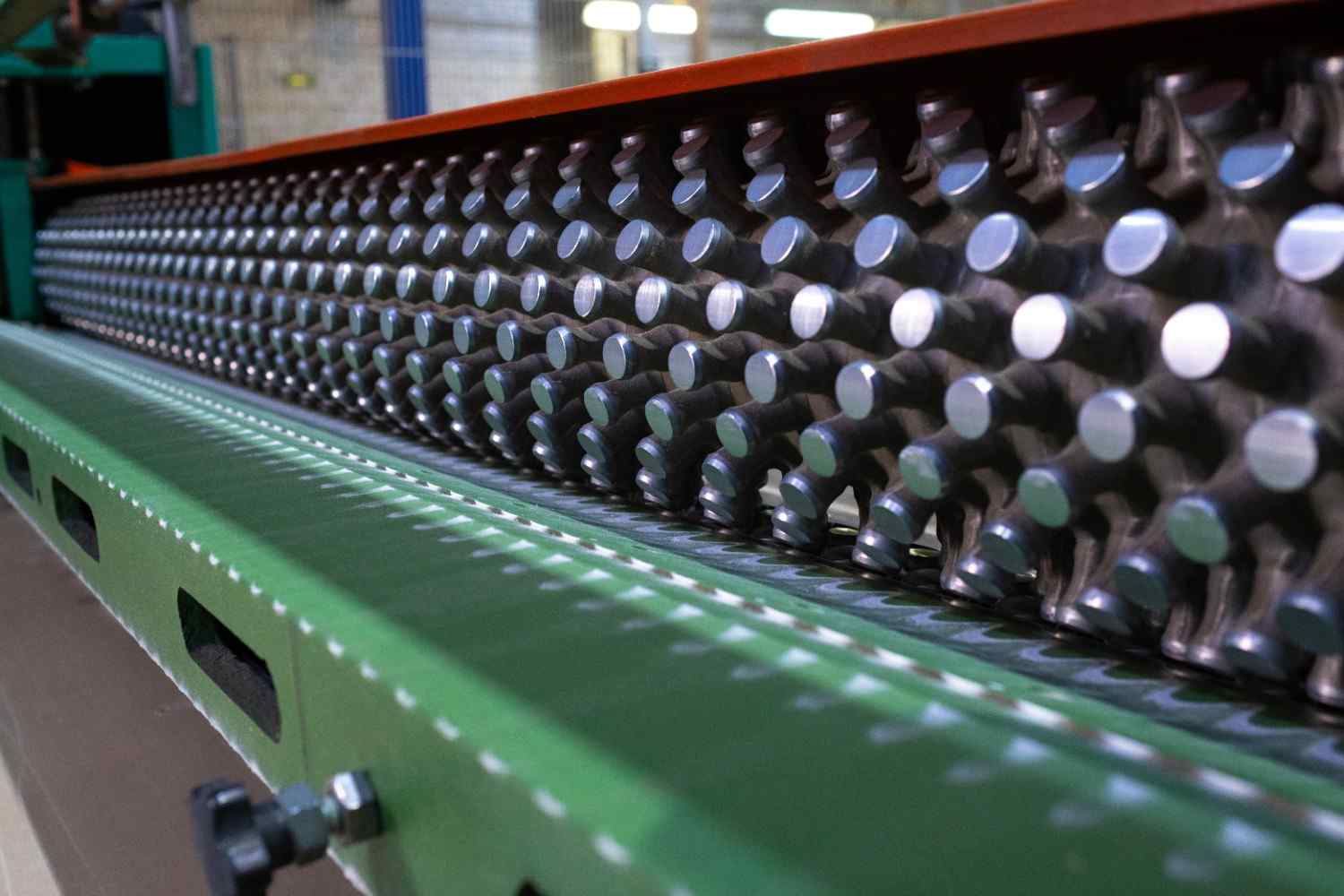
Tehnoguma Roller Solutions–Static Control Experts
Tehnoguma understands how important it is to have static control measures in place when dealing with flammable materials; we do not just supply rollers, we partner with you to create safer and more efficient working environments. Our range of high-quality anti-static rollers shows the depth of our commitment to this area: whether customers need Static Dissipative (SD) products that slowly release an electric charge or Conductive (CD) items that channel it away very quickly, we can help. Selecting the right product is only the beginning–we also offer advice on designing effective grounding systems (essential for good static control) along with suggestions for keeping rollers in top condition so they last longer and perform better saving users money in the long run. But we provide more than just goods plus guidance…Complete Static Control Solutions from Tehnoguma. We will work closely with your team to assess its precise requirements before developing a bespoke deployment strategy for anti-static conveyor rollers across your site(s). This might involve: installing equipment at key touchpoints. and conducting scheduled maintenance checks to ensure everything is working optimally. By partnering with Tehnoguma — experts who specialize solely in preventing fire explosions caused when electricity jumps from one object to another directly through the air — clients benefit from having an ally who understands all their needs regardless if the material being handled is fuel chemical solvents or any other flammable substance. We care for our clients and their results. If you want to discover more on conveyor belts read Conveyor Belt Maintenance Tips: Revamp Efficiency & Lifespan and explore what you need to know. Don’t miss out on Industrial Rubber Rollers: Know their Role and Procedures and see what procedures are involved. Maybe you are interested more in the technicalities and want to go deeper on Industrial Roller Hardness: Choosing The Right Shore A. If you have issues with the alignment of your rollers read Roller Alignment: Tips for Extended Conveyor Belt Life so you can get first-hand information. We also suggest that you go through Conveyor Belt Splicing Methods For Secure and Reliable Bonds and learn the best practices for the techniques included for belt splicing.
Conclusion
Although you can’t see it, static electricity is a major danger when working with materials that catch fire easily. The good news is there’s something simple you can do to protect yourself and your co-workers. Putting in anti-static rollers and other useful devices makes handling flammable substances a lot safer. It’s worth being active about controlling static because it pays off. Your investment will not only reduce the risk of accidents but also help things run better overall. This could mean anything from a job getting done more quickly to saving money on damaged goods.
If this makes sense to you why not get in touch with Tehnoguma and solve your requirements and cost dilemmas? We have lots of experience in helping people pick the right equipment for their needs. With our anti – static rollers on board, your team can work efficiently, effectively, and without harm.
Don’t forget to check our markets & services section so you can discover our comprehensive coverage across industries. Remain up to date by returning daily to our industrial rubber news section where you will get the latest news, advancements, and discoveries in the industry.