Rubber roller hardness is crucial in many industries especially in the printing industry defining the quality of the print. The realm of commercial printing is fierce. Many components need to come together perfectly for optimal results. While end users lavish attention on high-resolution printers and carefully crafted inks, one crucial piece is often overlooked: rubber rollers. Though these parts may appear basic, they have multifaceted roles within the world of printers. When a page is printed, for instance, its colors and text need to be razor-sharp — an impossible outcome unless the rollers can apply ink to plates evenly (so the plates can then transfer it to paper). This is predicted by the rubber roller hardness level.
Moreover, the force with which rollers press against plates must remain constant. Rollers also perform sundry other tasks. After rotating forwards, for example, they must rotate backward; they must additionally stay free of debris such as specks of dust or fragments of paper. This dirt-busting role falls to sticky-out bits. Yet rubber roller hardness is arguably their most important attribute when it comes to quality printing jobs – ones producing materials you’d actually want to read closely.
Hardness here refers to the roller’s resistance to penetration; this is typically measured using something called Shore A durometer scale. Should a roller be too soft there could be fuzzy-edged letters rather than nice clear ones; should it err on the hard side then colors might appear wrong.
This article attempts to illuminate a facet fascinating area: explore what rubber roller harness does (including effects of various quality measures); provide some scientific materials-science background on why picking material with the right hardness is crucial to achieving desired outcomes. We hope the overview provides useful background information for subsequent sections; please let us know what you think!
When it comes to industrial rubber Tehnoguma covers the mining industry, food production, ergonomics technologies, roller technologies, and more. Read this article and find out what to do to get the best results in terms of rubber roller hardness and printing quality input.

Functionality and Diversity: Rubber Roller Hardness in Printing
Rubber roller hardness is what you have to deal with in order to adjust the quality of your prints. They do many jobs that affect print quality. For example:
- Ink Transfer and Distribution: Ink doesn’t magically appear on paper. It travels from a reservoir onto one roller, then onto another roller. Both rollers need to be just the right hardness: if not, the ink might go on too thickly… or not at all.
- Pressure Control and Paper Handling: Ever heard of ‘ghost’ images? This is when something was supposed to look one way (e.g., black cat) but also has parts that look different from the rest (pink cat toy). Rubber rollers help prevent this sort of thing by pressing the paper and ink together with controlled force. And they help feed the paper through the printer smoothly (important for keeping everything in line) while it’s still a bit wet from having been rolled on two times already!
- Dampening System Management: If you’ve ever tried to paint water over a greasy surface, you’ll know they don’t mix. Printing is a bit similar: areas that should be color-free have to stay that way – and they’re only able to do so because dampeners roll over them first thing after each rotation; these special rubber-coated rollers pick up water from one tray and deposit it onto another evenly enough.
A Symphony of Materials: Tailoring Rubber Selection for Specific Printing Needs
Rubber rollers need to be both hard and made from the right rubber material if they are to do a good job. Different kinds of rubber do different things when used in printing press rollers:
- Natural Rubber: This does a bit of everything because it is both springy and strong. It is used for impression rollers (which need to push paper against type) and some ink distribution rollers too.
- Synthetic Rubbers: These can cope with a wider range of tasks than natural rubber. Nitrile rubber, for example, resists oil. EPDM rubber stays cool even when going very fast – which makes it great for high-speed printing
- Silicone Rubber: This stuff stands up to chemicals well and is safe for use around food. Printing companies use silicone rollers on jobs that must not fail for these reasons. But hardness is also important when choosing rubber for rollers. Printers select blends based on how hard they need their rollers to be as well as what else they have to do and how fast.
As a result, there isn’t just one type of rubber that works best; by picking carefully firms can make sure their rollers perform well and produce high-quality print jobs. You can read and learn more on Printing Rubber Rollers: Hardness & Printing Quality.
The Numbers Game: How Shore A Hardness Dictates Printing Perfection
Although rubber rollers must function correctly to achieve good results, when it comes to print quality there is one specific thing that matters: how hard they are. This can be measured – and compared with other materials – using an instrument called a Shore A durometer, which gives a value between 0 (for something extremely soft) and 100 (very hard indeed). Knowing the Shore A hardness of your rubber rollers could help you improve various aspects of print quality.
Demystifying the Shore A Scale: A Printer’s Guide
Suppose you had a tiny finger and could make it press down on a rubber roller. The Shore A durometer would tell you how much the material underneath resisted this pressure. In short: the harder its surface, the higher the roller’s Shore A reading will be – and the better the results when you use it for printing:
- 0-30 Shore A (Very Soft): These rollers are incredibly elastic and fantastic when it comes to absorbing shocks and vibrations. Although they are not generally recommended for direct ink transfer, there could be some cases where people find them useful with specific printing machinery for very delicate materials.
- 30-50 Shore A (Soft to Medium): Rollers within this range offer a mix of flexibility and rigidity that makes them perfect for dampening systems: they soak up water well while still being firm enough to move against a surface. An even spread of moisture from such rollers contributes significantly towards achieving the right balance between ink and water on a plate.
- 50-70 Shore A (Medium to Hard): Many printers consider using rollers of this hardness grade because they strike a balance between softness and firmness that suits lots of different jobs. A typical example is an impression roller or distribution roller which needs to apply uniform pressure as it delivers ink – but also releases dots from its surface without smudging them.
- 70-100 Shore A (Hard to Very Hard): If you need a roller to cope with rough surfaces or gritty substances day in and day out then hard rollers will probably suit best. However, there is little forgiveness should one of these very rigid tools accidentally catch an edge when working over fine details or artworks onto sensitive materials: damage could result.
The Art of Nuance: How Hardness Impacts Color Accuracy and Image Sharpness
The interplay between roller hardness and ink transfer directly affects color accuracy and image sharpness. Here’s how:
- Color Accuracy: Softer rollers tend to release ink more readily. While this can be beneficial for achieving a solid ink laydown, it can also lead to excessive ink buildup on the printing plate, potentially causing color variations. Conversely, overly hard rollers may struggle to release ink effectively, resulting in a pale or uneven print.
- Image Sharpness: Precise pressure during printing is essential for maintaining sharp image details. Rollers with the appropriate hardness ensure consistent and controlled contact with the printing plate, preventing image blurring or ghosting. Softer rollers might not provide sufficient pressure, leading to a loss of detail, while excessively hard rollers can damage the printing plate or cause unwanted embossing effects.
Cases in Point: The Registration Tango
When it comes to quality in printing, getting registration right – the perfect alignment of multiple elements or colors on a page – is crucial. One thing that affects this? How hard your rollers are
- Mismatched Hardness: If rollers don’t match up… Let’s say an impression roller (the softer kind) is working alongside a distribution roller of the harder variety. When pressure is applied, the soft roller may compress slightly. This could mean the image going from plate to blanket does so inaccurately by a tiny fraction – and such minuscule misalignments often show as registration blips on final prints.
- The Perfect Match: Or you could pair them perfectly! Printers who choose rollers with similar hardness levels can be confident that force is spread evenly across blankets and plates. There is less chance of things being squashed out of shape or warped during this stage – both common causes for concern when seeking precise registration and an unblemished finish.
In our next section, we’ll discuss material handling and ink distribution further; both are processes heavily influenced by roller durometers.
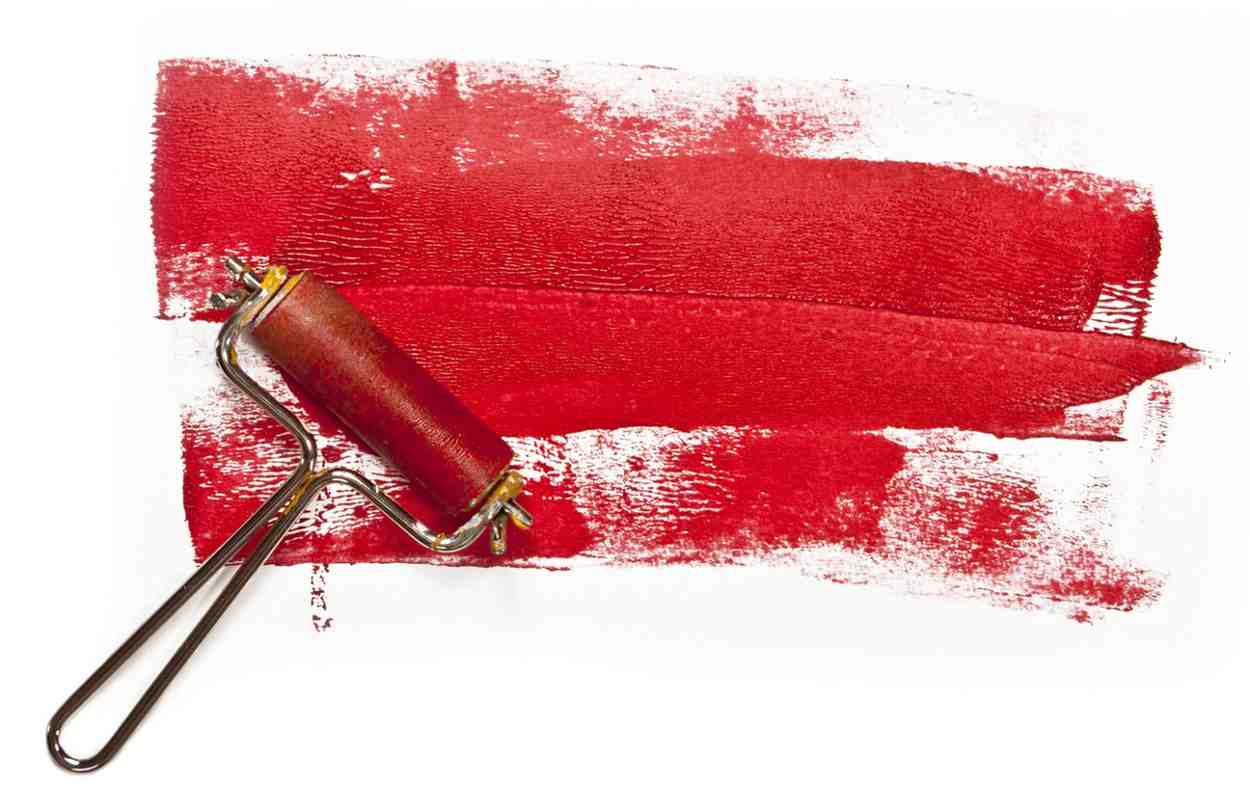
The Ripple Effect: How Rubber Roller Hardness Impacts Beyond the Obvious
Roller hardness has an impact that goes beyond color accuracy and image sharpness– it affects many factors which in turn affect overall printing quality.
The Delicate Dance of Material Handling and Ink Distribution
So although hardness is important for those first two characteristics; there’s also the feel of its movement across an entire page or how evenly one color spreads when applied alongside others:
- Paper Feeding and Web Tension: It is important to keep the paper feeding steady and maintain tension in the web during printing if you want your prints to be perfect. Rubber rollers need to have just the right amount of give – that is, be hard enough (50-70 Shore A) – so they can grip paper well without causing it to wrinkle or skew.
- Ink Transfer and Distribution: Getting ink onto paper involves more than one set of rollers, as we saw above. Here’s why their relative hardness matters: an ‘impression’ roller will squash an even layer of ink out from its surface; then a slightly harder ‘distribution’ roller picks this up and gives (transfers) it to the printing plate.
- Minimizing Print Defects: Using the wrong hardness of rubber in any roller could mean problems with your print. If they are too soft, for example, some areas might get squashed too much – leaving marks or even taking off previously dried ink (this is known as ‘piggy-backing’ in the trade). But if all the rollers are hard there is a risk prints will look patchy because not enough ink has been distributed at each point.
A Long-Term Investment: Durability and Maintenance Considerations
The correct hardness of rollers doesn’t just affect how good your prints are – it also affects how often you need to replace parts, as well as general upkeep. Here’s why:
- Durability and Wear Resistance: Harder rollers (rated 70-100 on the Shore A scale) tend to last longer if you use them with materials that might scuff them up like sandpaper. But if your printer deals mainly with delicate surfaces, these tough rollers could damage them. Picking the right hardness for each job helps avoid early wear & tear and keeps things going smoothly.
- Reduced Maintenance Costs: Choosing well-made rollers less often will mean lower bills for replacing worn-out parts plus doing maintenance. What’s more, rollers at the correct level of hardness should not get damaged as easily if someone pushes down on them too hard by mistake or does not handle them properly; so overall maintenance costs come down still further.
- Optimizing Performance Through Adjustments: Printers sometimes alter how hard their rollers are to get a certain effect. If you use softer impression rollers with thick materials there will be an even pressure across their surface. Sometimes it is possible to slightly change roller hardness to achieve different results, but such alterations ought only be made by experts in printing – and even then very carefully!
- The Art of Regular Maintenance: It doesn’t matter whether they’re soft or hard, if printer rollers are to work well they must receive regular care and attention. This means more than just cleaning them – although that is important too! Users should also check for signs of wear as well as ensure the rollers are correctly aligned. Carrying out these simple tasks can make a real difference; printers whose rollers are looked after properly not only produce better results for longer but may also require replacing less often overall.
Below we’ll look at some recent developments around how these machines function – plus what lies ahead. You can also go through Industrial Roller Hardness: Choosing The Right Shore A and discover all related to rubber rollers hardness in different industries.
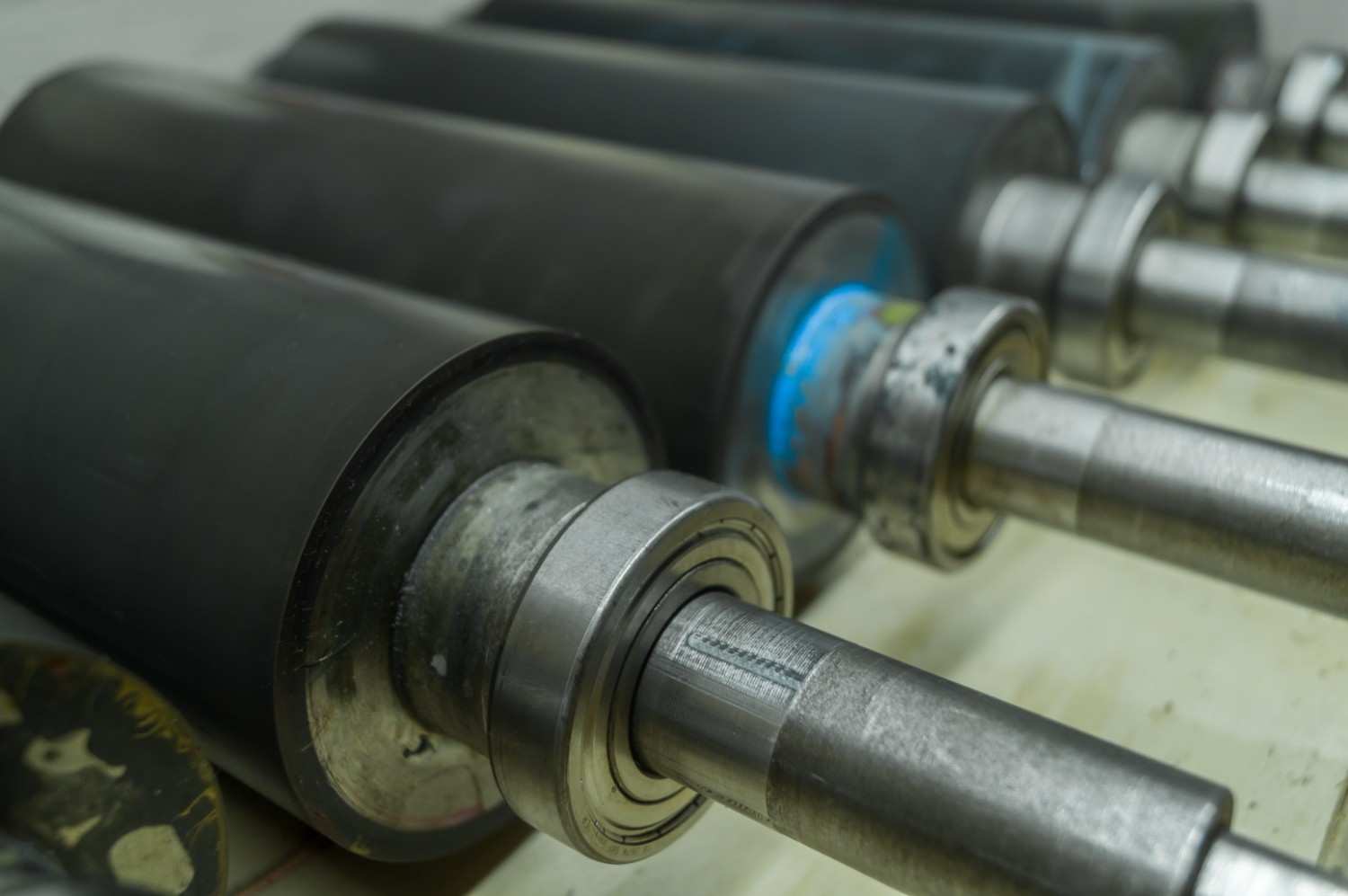
Printing in the Fast Lane: Technological Advancements and Industry Trends
The world of printing is constantly evolving, and roller technology is keeping pace. Here, we’ll explore some of the exciting advancements that are pushing the boundaries of print quality and efficiency.
Revolutionizing Manufacturing: Consistency and Durability Redefined
Traditionally, achieving consistent hardness across a rubber roller has relied heavily on meticulous manufacturing processes. However, innovative techniques are changing the game:
- Laser-Etched Rollers: This cutting-edge technology utilizes lasers to create precise surface patterns on rollers. These patterns not only enhance grip and ink distribution but can also be strategically designed to achieve specific hardness variations within the roller itself. This allows for even more nuanced control over printing effects.
- Advanced Compounding Techniques: The development of new rubber compounds with improved homogeneity ensures consistent hardness throughout the roller material. This minimizes the risk of inconsistencies that could impact print quality.
- Nanocomposite Rollers: The incorporation of nanoparticles into rubber formulations is creating a new generation of rollers with exceptional wear resistance and durability. These rollers can withstand higher printing speeds and handle more abrasive materials without compromising performance.
The Rise of the Smart Roller: Dynamic Adjustments for Optimal Printing
Printing in the future could see rollers becoming more than just passive parts of a machine. They may become smart technology that works with people to get the job done. Here is an idea of what these clever rollers might be able to do:
- Embedded Sensors: What if your printer rollers could tell how hard they were working in real-time? With tiny built-in sensors, this would be possible. If the roller started to get a bit harder or softer while it was printing, the sensor would pick up the change. It could then send this information wirelessly to a central computer system that controls the whole printing process.
- Dynamic Hardness Adjustments: The central computer could then use the information from the sensor to change how hard or soft the roller was pressing on the paper while the inked image is being put on it. This might mean heating or cooling some parts of the roller system, or making air pressure alterations within different chambers along which each roller shaft rotates.
- Predictive Maintenance: Smart rollers might also contribute to preventive maintenance initiatives. If the devices tracked variables such as wear and tear, they could anticipate potential problems – and give operators a heads-up before issues arose. Such foresight would help minimize downtime and keep printing quality more stable over time
Although still evolving, these capabilities have enormous promise: They could upend the printing industry by boosting efficiency and quality in ways never before possible. Imagine combining real-time adjustments with two qualities already associated with rollers – consistently hard surfaces that last a long time. A productive new era might be on its way. In the next section, we wrap up this overview.
We’ll suggest practical applications and recommend how to choose rollers with the right hardness level for specific jobs.
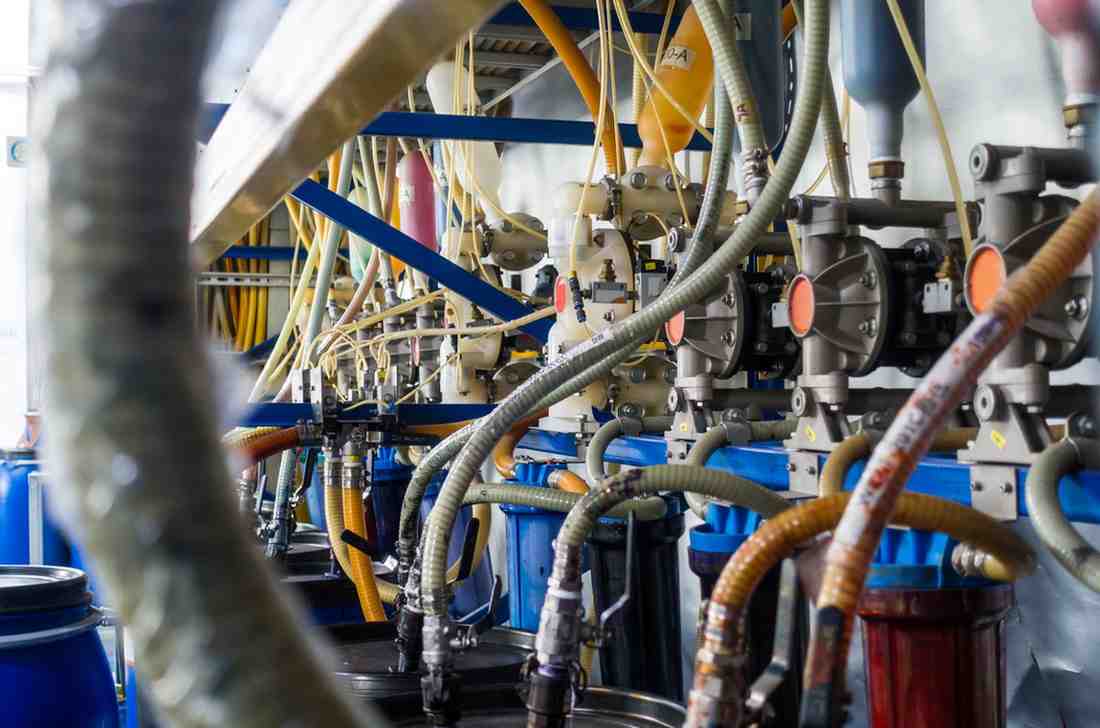
Tailored Rubber Roller Hardness for Industry-Specific Needs
The effect of roller hardness goes beyond theory; it leads to tangible benefits in a wide range of printing applications. Here we look at some examples from particular industries:
Packaging Perfection: Balancing Speed and Durability
The packaging industry needs to be able to print quickly while still producing clear graphics and colors that don’t smudge or bleed. In this sector, hard rollers come into their own:
- High-Speed Printing: When it comes to production lines that need things done quickly, rollers rated 50-70 Shore A are usually best. They’re a good compromise between being hard enough to keep the pressure constant and soft enough to cope with small changes in thickness.
- Durable for Abrasive Materials: Some materials used for packaging – such as cardboard or corrugated board – can be a bit abrasive which means they gradually wear away at things. In these situations, printers benefit from using rollers that are a little harder (60-70 Shore A) because then they last longer without producing lower-quality prints.
Enhanced Efficiency in Corrugated Box Printing
A top manufacturer of corrugated boxes was having problems with print quality that varied too much, and its rollers needed replacing often because they wore out from use. To address these issues, the company adopted a new system featuring:
- Impression rollers: 60 Shore A hardness impression rollers provide uniform pressure and produce clearer images.
- Distribution rollers: 65 Shore A hardness distribution rollers that spread ink more consistently, reducing buildup.
The result? Significantly better overall-quality prints, less downtime spent switching rollers –– and greater productivity per printing shift.
Publishing Finesse: Achieving Flawless Color and Crisp Text
The publishing industry places a high value on precise color reproduction and sharp text rendering. Roller hardness plays a role in achieving both: To strike the right balance between detailed images and vivid colors when producing top-notch books and magazines, printers tend to favor rollers with these capabilities:
- Balancing Color Accuracy and Detail: Printers who produce high-end books and magazines tend to favor rollers with a hardness rating of 40-50 Shore A. This combination enables controlled ink application, yet just enough flexibility to capture the sharp edges of tiny text and graphics.
- Dampening System Optimization: Getting the water-ink ratio exactly right is critical for top-quality reproduction. Here, using rollers rated at 30-40 Shore A provides excellent water retention and release – so colors ‘pop’ and text remains legible.
Achieving Award-Winning Print Quality in Book Publishing
An esteemed publisher wanted to improve how its coffee table books looked in print. The solution? Special rollers:
- Impression rollers: with 45 Shore A hardness to give reliable pressure and make sure colors came out exactly right;
- Distribution rollers: with 50 Shore A hardness so ink went on evenly (but without losing any fine details);
- Dampening rollers: had 35 Shore A hardness which took up water well but still managed an even balance between this liquid & the inks used.
The outcome? Print jobs worthy of prizes – they had super-sharp images, fab finishing touches plus colors that popped off each page! There is now a higher standard when it comes to what this firm calls ‘publications.’
As we shall see from the examples that follow, choosing bespoke roller hardness can bring big benefits. If printers take time to understand individual requirements for every printing task; and select the most appropriate rollers – then the quality of finished prints will be better overall (as will efficiency levels meaning lower costs too). How do you know which hardness is right for which job though? Next up some tips along with other things worth knowing if want your kit to achieve an optimum level!
Choosing the Right Rubber Roller Hardness
Choosing the best roller hardness depends on fully understanding what you need from your printing – and here are some important things to think about:
Printing Requirements
- Substrate: Softer rollers (Shore A 30-40) will handle fragile materials like tissue paper gently, while harder rollers (Shore A 50-70) give better results on tougher stuff like cardboard.
- Ink Type: The ink you’re using also matters if you want good results. Quick-drying inks may need softer rollers (Shore A 40-50) so they transfer properly; by contrast, hard rollers (Shore A 50-60) can stop slow-drying inks from smudging.
- Print Quality Goals: Think about what you want your finished print to look like. If it’s really important that colors are strong or typefaces are very clear with lots of detail, then a slightly softer roller (Shore A 40-50) might be best. On the other hand, images that call for block color and high levels of opacity often benefit from harder rollers: try Shore A 50-60.
Environmental Conditions
- Temperature and Humidity: Extreme temperature or humidity changes can affect how well rollers work. It’s important to talk to your equipment supplier to make sure the rollers you choose will stay hard enough as they get warmer or colder in use.
Collaboration is Key
Achieving optimal roller hardness requires collaboration from both suppliers and users. Here are several suggestions on how to do this:
- Consult your Equipment Supplier: They are experts in their field and will be able to tell you which hardness range is best for your printer model as well as suggest suitable materials for the rollers.
- Manufacturer Recommendations: Printers often come with different types of rollers available- so it’s worth looking into what each one does before deciding on buying new ones based solely on this factor; Ask them too how hard these products should ideally be used within specific machine types (eg lithographic).
- Consider Custom Solutions: For highly specialized printing needs, some manufacturers offer custom roller solutions with tailored hardness profiles. This can be particularly beneficial for achieving unique printing effects or handling challenging materials.
Take your time to review these aspects and work with industry professionals – they will help you choose the best roller hardness for your printing needs. Don’t forget: If you make the right choice, you’ll get a return on your investment because good rollers will give you an edge over competitors as well as high print standards.
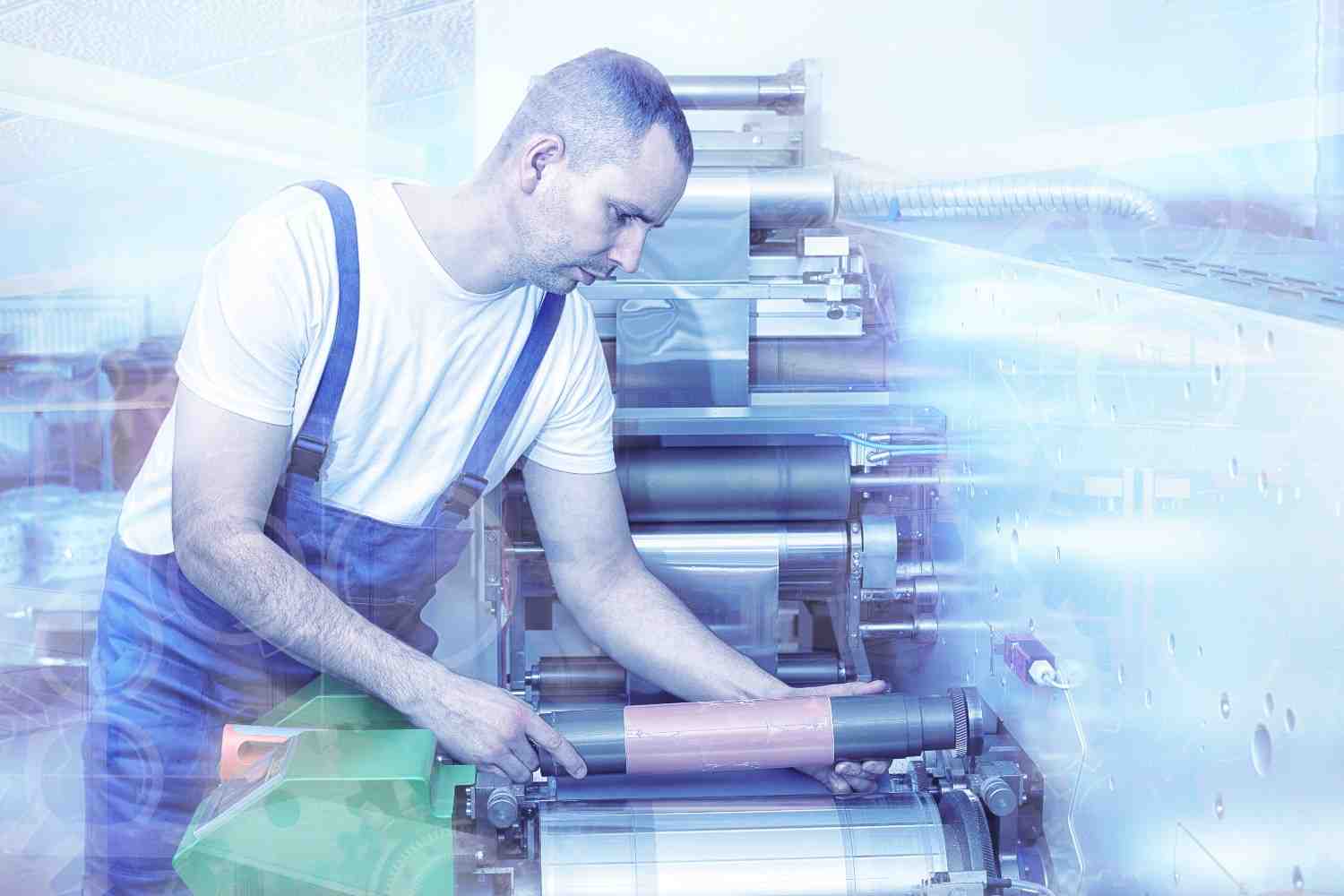
Rubber Roller Hardness: Quality Control and Testing Methods
In today’s fast-moving world one of the most important things when it comes to printing is having rollers that stay the same hardness – and don’t wear unevenly. We’re going to look at some tests which can be done both during production (quality control) and afterward so you know your rollers are still in tip-top shape.
The Importance of Quality Control
Regular checks to make sure your rollers have not gotten harder or softer since being put in the machine are important for a few different reasons:
- Maintaining Print Quality: Even small differences in roller hardness can affect color accuracy, image sharpness, and other important print quality factors a lot. If you check regularly and nothing’s wrong, you know your rollers are still okay — which means their output should be fine too.
- Maximizing Roller Lifespan: Hard-wearing rollers will last longer than soft ones. But how do you know what condition yours are in? Again, checking how hard they are regularly can help – if they’re starting to wear out it might be worth replacing them now rather than waiting until they stop working altogether (unless of course, you enjoy spending money on unnecessary equipment!).
- Ensuring Safety: Damaged rollers don’t just produce bad results; there could also be a safety issue if for example an old piece broke off while rolling and got jammed somewhere it shouldn’t be! A program of checks will pick up signs of wear before they become dangerous – or costly because they need repairing too.
Testing Methods for Consistent Performance
There are multiple reliable ways to evaluate roller hardness and make sure it meets industry standards
- Durometer Testing: This is how rubber hardness has always been measured in this field; a durometer uses a special tool to push into the roller surface and make a small dent. How far this tool goes in (depth of indentation) gives a number on the Shore A scale, which corresponds with ‘hardness’.
- Non-Destructive Techniques: New technology means we now have tests that can check whether something is hard enough without damaging it (such as rebound testers or ultrasonics). These methods are great when you need to do regular quality control checks but still sellotape things back together afterward!
- Performance Testing: Sometimes assessing print quality can also provide clues as to whether rollers are up to scratch or not. If colors don’t look right (e.g. an ‘unusual shade of green’) images/graphics aren’t sharp ‘enough’ or there are lots of blotchy bits for no apparent reason.
Industry Standards and Best Practices
It is common for industry organizations or individual printer makers to set roller hardness benchmarks. Here are some QC suggestions:
- Establish Testing Frequency: Establish how often you will test the durometer based on variables such as printing volume, ink characteristics, and substrate type.
- Maintain Detailed Records: Write down your test procedure, hardness readings, and any steps you take to correct a problem. This information may help later if you notice a pattern or need to look up past results.
- Invest in Training: Make sure your staff members know how to use the durometer correctly so that everyone gets the same results.
Using these control methods along with testing techniques will help you keep rollers at a constant hardness level. This is important because hard rollers print fine details well but can damage the plate; soft rollers do not print detail sharply but protect the plate.
Controls also will improve machine performance overall and make printing more cost-effective long term.
Conclusion
To sum it up on rubber rollers’ hardness, even though people don’t always think about it, how hard rubber rollers are? This becomes super important if you want your printing to look good and be as efficient as possible. If you understand the way hardness affects things like putting ink onto paper and spreading out pressure (as well as other factors), then choosing the right rollers–and making sure they stay in top condition once you’ve got them–can help make all this happen more easily/ better.
There’s some really interesting stuff going on with rollers right now too: New developments in manufacturing techniques plus the ability to build sensors that measure how hard something is while it’s working (and send these data back for analysis in real-time) may well change lots of things about how we do print–again!
Printers who’d like to take advantage of such possibilities might want: To talk to their suppliers about what could soon be available; keep an eye on quality control very closely during production; and find out more regarding any breakthroughs as soon as they become known. If all or anyone from this list pans out, then users will gain extra precision over jobs plus an ability never before had when using presses alone – namely being sure every single sheet looks perfect no matter what!”
Still have unclear spots. Reach out to our customer support and be led through your answers receiving the best deals for your needs.