Insulating rubber comes as a savior. Did you know that electrostatic discharge (ESD) is responsible for up to 60% of electronic component failures during manufacturing? These invisible zaps can wreak havoc on delicate circuits, causing malfunctions and costly disruptions in production.
This article delves into the world of insulating rubber and its critical role in safeguarding electronics during manufacturing. We’ll explore the inherent properties of insulating rubber that make it a champion of ESD control, and delve into the latest innovations that are further enhancing safety and efficiency in the electronics production process.
Our journey will explore the fundamental properties of insulating rubber that make it an effective shield against ESD. We’ll then examine how these properties translate into tangible benefits for electronics manufacturers, including reduced component failures, improved production yields, and ultimately, enhanced product quality and reliability.
Finally, we’ll shine a light on the latest advancements in insulating rubber compounds and manufacturing techniques that are pushing the boundaries of ESD control and shaping the future of electronics manufacturing.
We at Tehnoguma cover industrial rubber in many fields the mining industry, food production, ergonomics technologies, roller technologies, and more. Read the whole article and become informed before taking decisions.
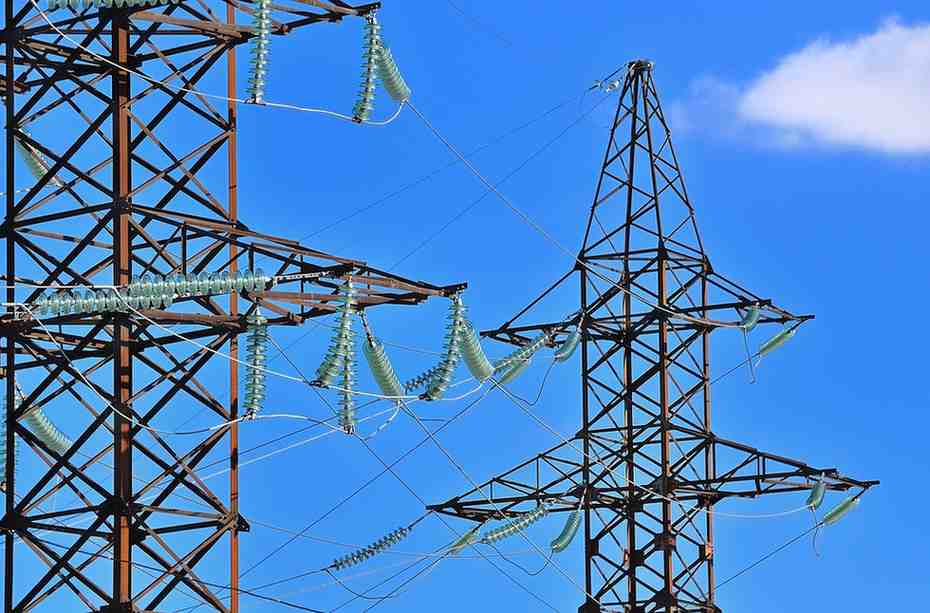
Insulating Rubber: Shielding Electronics from Zaps
The Silent Threat: Electrostatic Discharge (ESD)
In the busy world of making electronics, there is a hidden danger – electrostatic discharge (ESD). These little shocks, which occur when static electricity builds up and then suddenly escapes, might not seem like much but they can cause real harm. Figures show that ESD is behind as many as 60% of all faults found in electronic parts during manufacturing. Even one tiny zap can hurt sensitive circuits so badly that parts stop working properly; when this happens on production lines it costs lots of money because things have to be fixed or replaced.
The Guardian Is an Insulating Rubber
Luckily there is insulating rubber: a material that acts like a bodyguard for gadgets being made using it. Specifically designed types of rubber provide a protective barrier against ESD; with this layer in place, delicate components are safe from the dangers posed by static electricity throughout every stage of their creation.
Insulating Rubber Properties
The benefits of insulating rubber may seem like magic, but they’re actually due to its unique blend of scientific properties that are perfect for ESD control:
- High Electrical Resistance: Materials that conduct electricity let it flow through them easily. This is not the case with insulating rubber – because it has a high electrical resistance. In fact, most varieties have resistances greater than 10^8 ohms per centimeter. The resistance works like a roadblock: It stops electric current moving from sensitive electronic parts into or through the rubber. Can withstand big voltages! Top-quality insulating rubber can take a jolt of up to 30,000 volts (30 kV) without breaking down. That means using these materials reduces the risk of damaging components while you’re handling them or building them into things.
- Durability: This stuff has got to last! Manufacturers make insulating rubber tough so it can cope with being used every day under pretty harsh conditions. It also needs to be resistant enough not to wear out quickly and provide ongoing protection over long periods – such as throughout product assembly cycles..
- Flexibility: Things get moved around a lot in factories. They also often have bits that are close together, making intricate movements necessary during production processes. Fortunately being very flexible (unlike some rigid materials), insulating rubber molds itself well around shaped surfaces creating an effective barrier against ESD that looks as though it isn’t even there!
- Anti-static Characteristics: Some types of insulating rubber come with additives to make them extra good at staying static-free. Because if static does build up on the surface then it reaches a level where it could jump onto (and thereby damage) electronic parts those clever extra chemicals will help prevent this from happening by safely dissipating charge built-up—ACDC style!
Rubber vs. The Rest: A Comparison of ESD Control Materials
Although there are other materials used for ESD control, insulating rubber is the best. Here’s why:
Material | Advantages | Disadvantages |
Insulating Rubber | High electrical resistance, durable, flexible, anti-static options | May require periodic cleaning to maintain effectiveness |
Metal Grounding Straps | Excellent conductivity, affordable | Can be cumbersome and restrict movement, risk of accidental short circuits if not properly grounded |
Conductive Foam | Conforms well to uneven surfaces, lightweight | May not be as durable as rubber, and can lose conductivity over time |
When manufacturers use insulating rubber in their production lines, they get a valuable partner in the fight against electrostatic discharge. Insulating rubber has many qualities that make it perfect for the job: It is resistant to electricity, tough, flexible, and anti-static. These qualities combine to create a kind of shield around delicate electronics.
This shield helps ensure that production runs smoothly and that components do not fail; meaning fewer items are returned and firms can be more confident about the overall quality of their products.
So important has insulating rubber become in the sector that its unique blend of abilities now sees it described as a ‘superhero’ product: one that protects electronic goods from the brief bursts of energy that can cause so much damage– even though these bursts are invisible and cannot be felt. Read and explore more on Anti Static Conveyor Rollers In Flammable Material Handling.
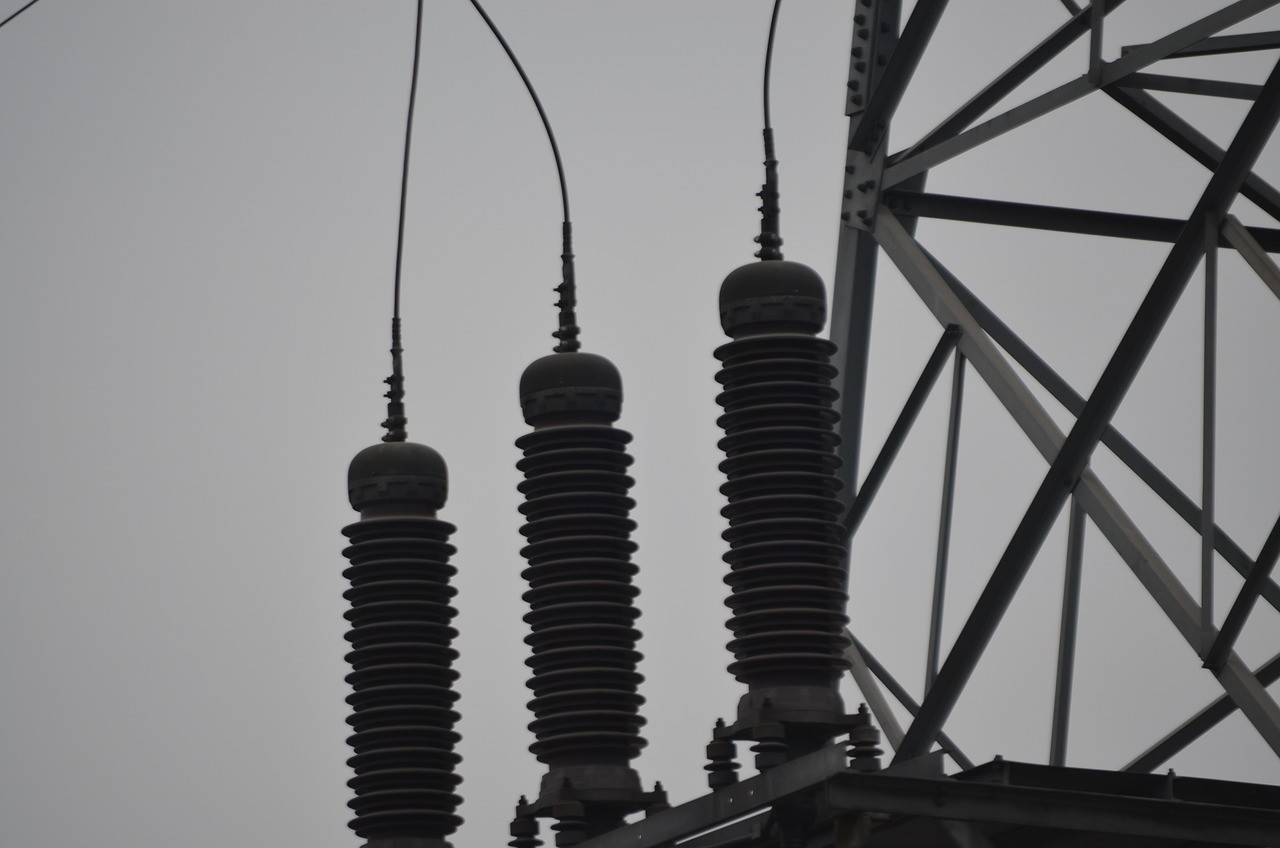
Innovations in Insulating Rubber: Pushing the Boundaries of ESD Control
The world of insulating rubber does not stand still. Manufacturers continue to push the envelope, working with new formulations and developing fresh techniques that enhance ESD control capabilities still further. Here we provide an overview of recent advances:
Advanced Anti-Static Champions
- Carbon Nanotube Composites: These advanced mixtures contain carbon nanotubes – tiny cylinders with unique electrical properties. Within the rubbery material, a network of these microscopic cylinders forms that is very good at conducting electricity. As a result, any build-up of static charge is effectively dispersed so it doesn’t reach levels where an ESD event can occur. Put simply: compared to standard rubber compounds, they provide significantly better protection against ESD.
- Permanently Static Dissipative (PSd) Rubbers: This innovative material takes things a step further. PSDs boast permanently embedded conductive elements. Conventional anti-static additives are added to give items electrical conductivity (‘Psd’), they may move away from their intended location over time – meaning the item no longer performs as well. PSD rubber doesn’t have this problem; its conductive elements are part and parcel of the product and will therefore last as long as it does! With PsD rubber you can wave goodbye to frequent cleaning or changing of components just because they’ve stopped working properly. It could mean lower maintenance costs and greater efficiency in manufacturing too.
Durability and Flexibility: The Unshakeable Duo
Manufacturing environments are rough. Insulating rubber must be up to daily challenges — and recent developments mean it is now both tougher and more flexible than ever.
- Double-Layered Rubbers: These clever materials have a dual inner layer designed for high electrical resistance and an outer layer designed for durability (long life) as well as resistance to wear (tear). Because they have two layers with different jobs, Double-Layered Rubbers can provide a product made from them with good ESD protection while also making sure that it lasts a long time.
Thermoplastic Elastomers (TPEs): With these advanced materials, you get the benefits of using both plastics and rubber at once! One thing about TPEs is they are very flexible – so they can bend in all sorts of ways. This means they are great if you need something that will fit tightly around different shapes or in small spaces on a production line. TPEs are also worth considering if you want tough stuff that won’t be harmed by chemicals: because they do not break down when exposed to chemicals every day for a long period. (For the tech-minded: New kinds of insulating rubber made from TPEs perform well in conditions ranging from -40°F to 212°F!)
Electrical Resistance: Reaching New Heights
ESD control’s foundation is how well a material blocks electrical current. Recent advances in insulative rubber mean it can resist electricity like never before:
- High-Resistivity Compounds: New formulations utilize advanced fillers and additives to achieve electrical resistivity levels ranging from 10^6 ohm-cm (10^3 kΩ∙cm) to a staggering 10^9 ohm-cm (10^6 kΩ∙cm). This makes ESD protection more effective at safeguarding sensitive electronic parts – imagine a chain-link fence compared to one made from mesh wire.
- Surface Conductivity Treatments: Surface conductivity treatments take things a step further by applying a very thin layer of conductive substances onto the surface of the insulative rubber. This creates pathways for electricity that help control static charges better still.
The Takeaway
The progress made in developing insulating rubber compounds isn’t just good science – it means things electronics manufacturers can measure in dollars and cents. A better ability to resist static electricity, along with being both stronger and more flexible, as well as having unusually high resistance to electrical flow; all these factors together make for safer production systems where things work better. If companies adopt this new technology there are several benefits: fewer problems caused by electrostatic discharge (ESD); higher standards of products; plus an advantage over rivals in today’s fast-changing marketplace.
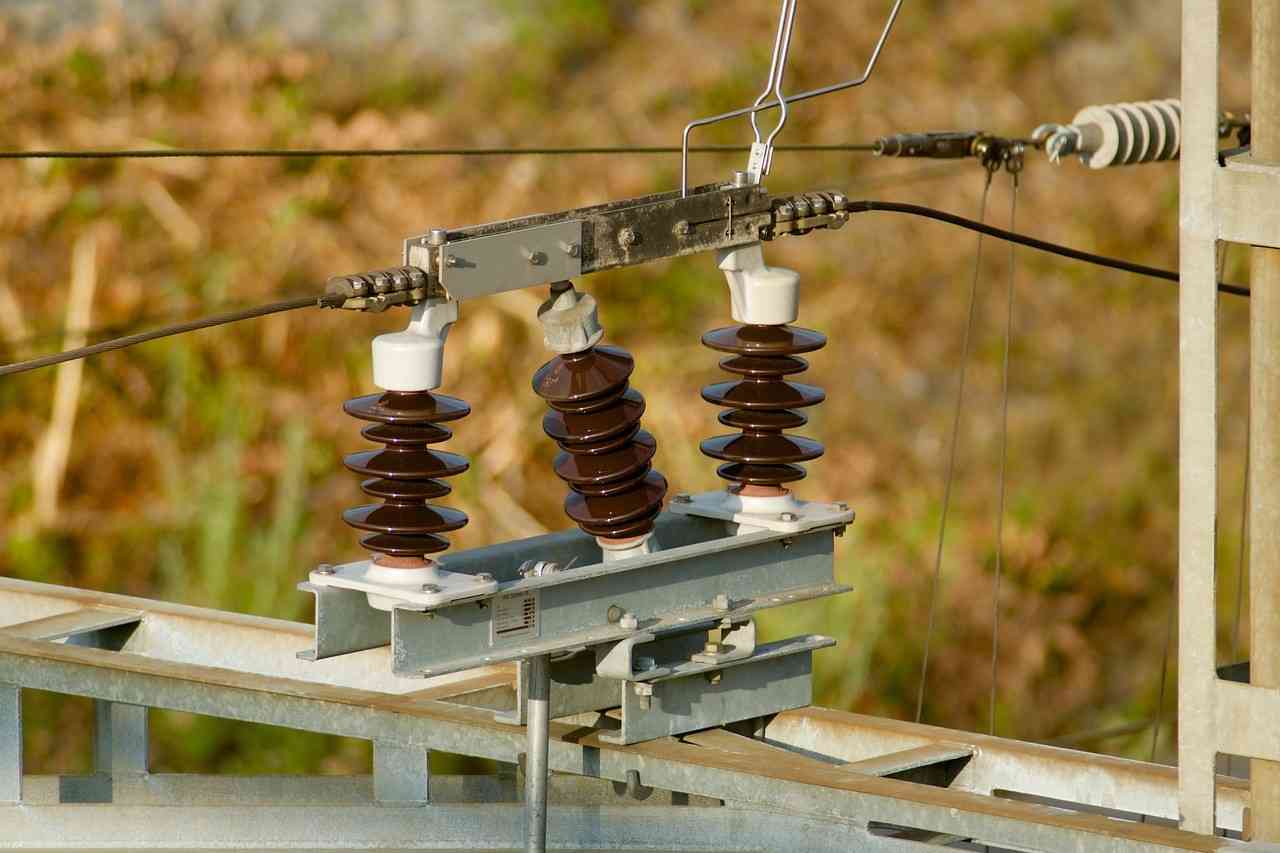
Reaping the Rewards: Benefits of Insulating Rubber in Electronics Manufacturing
The progress made in developing insulating rubber compounds isn’t just good science – it means things electronics manufacturers can measure in dollars and cents. A better ability to resist static electricity, along with being both stronger and more flexible, as well as having unusually high resistance to electrical flow; all these factors together make for safer production systems where things work better. If companies adopt this new technology there are several benefits
Electronic Frontier: Protecting Components
Imagine a world where microscopic zaps wreak havoc on your production line. This is the reality without proper ESD control. Insulating rubber steps in as the knight in shining armor, protecting sensitive electronic components from the silent threat of ESD:
- Shielding from Electrostatic Discharges: Insulating rubber’s resistance to electricity creates a barrier: it stops electrical current flow that otherwise might harm sensitive electronics. Malfunctions, data loss, or complete failures – equipment-damaging problems known generically as ESD – are much less likely when insulating rubber is used.
- Real World Example: One company that implemented an effective control program found its component failure rate dropped by 50% according to figures released at the end of last year; this kind of success could mean both fewer returns for repairs under warranty as well as higher levels satisfaction among clients who buy products which don’t break so frequently anymore!
Safety First: Protecting Workers
ESD poses dangers beyond damaging electric circuits. It can also endanger individuals’ health by subjecting them to electrical shocks – uncomfortable at best and harmful in rare instances. Rubber insulators help safeguard people in several important ways. On assembly lines, workers may stand on mats made from the material or wear wrist straps that are grounded.
Such devices counter the buildup of static charge on the body, thereby preventing a flow of electricity that could cause a shock to breakable parts a person is handling.
By offering this kind of protection insulating rubber goods foster both job safety (by making sure men and women feel well enough to concentrate on what they are doing) as well as overall well-being – there is also some evidence they cut down on workplace accidents generally.
The Bottom Line: Cost-Effectiveness
Ultimately, all manufacturing decisions come down to money. Insulating rubber may cost more initially but using it can prove cheaper overall:
- Reduced Component Failures: Fewer Things Go Wrong: Handle components with care (ESD control) by using insulating rubber and you should see a lot less of them fail. This means you will throw fewer away because they have not worked properly, spend less on making things again—and make bigger profits.
- Minimized Downtime: If parts stop working because of ESD when you are making something else they hold up production. Using insulating rubber to prevent this from happening means you don’t have to take breaks so often—so items move along the production line smoothly. You can now make things quicker which is more efficient overall.
- Lower Maintenance Costs: Regular cleaning or replacing materials that control static may be necessary; these jobs are an expense for your business.
Cost-Benefit Analysis: Rubber vs. The Rest
Even though there are other ways to control ESD, using insulating rubber (IR) is best — its benefits outweigh the costs. When you break it down! things look like this:
Method | Advantages | Disadvantages |
Insulating Rubber | High electrical resistance, durable, flexible, long-lasting, reduces component failures | Requires initial investment |
Metal Grounding Straps | Affordable | Can be cumbersome, risk of accidental short circuits |
Conductive Foam | Conforms well, lightweight | May not be as durable, and loses conductivity over time |
The Verdict
Insulating rubber proves to be cost-effective for ESD control in many ways, especially over the long term. When factories use it to prevent damage to electronic parts, they find that: Repairs and replacements are fewer; so they save money there. The line doesn’t have to stop as often for maintenance.
When maintenance is necessary, costs less. Workers like it because it keeps them safe—and because items produced while using it are less likely to malfunction later on.
Manufacturers who want all these benefits for their assembly lines should team up with companies that can supply innovative compounds. With these materials, businesses can foster both profits and protection; a dual payoff that few things other than rubber can provide.
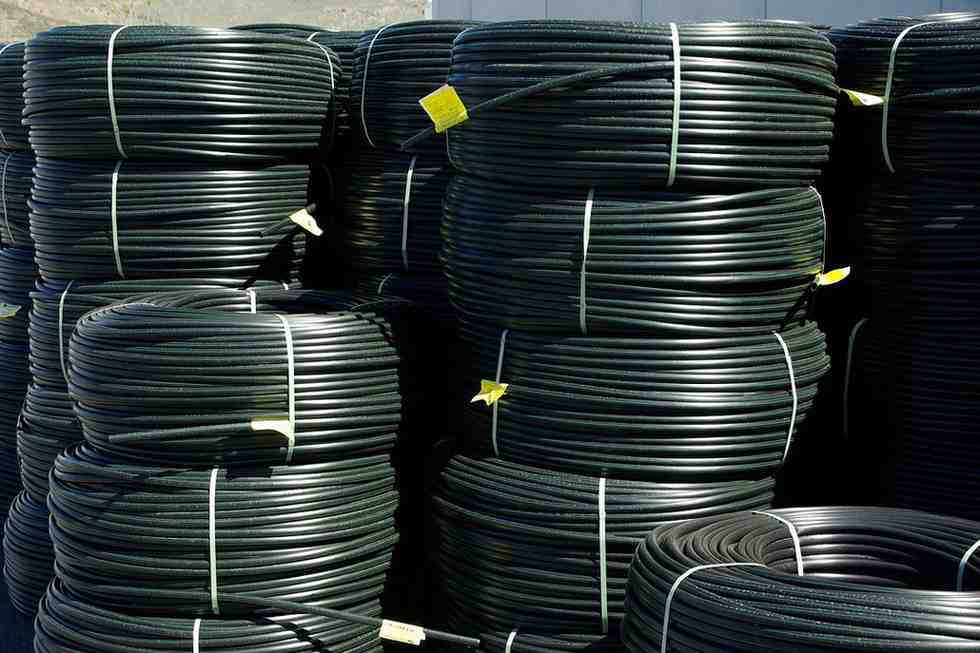
Applications of Insulating Rubber in Electronics Manufacturing
Insulating rubber has many uses in electronics manufacture. Its special qualities mean it can be used for lots of things, all with the same aim: protecting against ESD from every angle:
The Foundation of Safety: Anti-Static Mats and Flooring
Picture a production line where any single step might cause a harmful ESD event. Anti-static mats and flooring made from insulating rubber are there to help:
- By Dissipating Static Charges: These specially formulated mats and flooring dissipate the static charges that build up in workers’ bodies and the environment — preventing these charges from transferring to sensitive electronic components and thereby helping to reduce the risk of ESD damage significantly.
- Real World Example: One top electronics manufacturer saw a 25% drop in ESD-related component failures after installing anti-static floors throughout its facilities. This represented a real betterment of product quality as well as a major cost-saving effort.
A Second Skin: Insulating Gloves and Garments
ESD protection goes further than just the desk. Sometimes, employees unknowingly hold static charges – making them conductive. This is where anti-static garments and gloves are essential: They Stop Workers from Zapping themselves or Electronics! These specially designed clothes and gloves are made from insulating rubber – so they create a barrier. For instance: If someone wearing insulative gloves touches something with an electrical resistance (ESD) of 106 to 108 ohms, they won’t feel a thing! The charge will go into the ground harmlessly — rather than zapping sensitive electronics or giving the wearer a shock.
Guardians in Transit: Protective Covers and Enclosures
The battle against ESD doesn’t stop at the manufacturing stage. Electronic parts are susceptible even when they are being stored or transported. To protect goods while they are in transit (being moved) and storage, manufacturers use materials such as insulating rubber to make protective covers and enclosures. These goods are designed to create a barrier that stops static charges from the environment from damaging them. This kind of protection ensures that items arrive safely and work perfectly. For example, computer components may be kept inside anti-static bags made of insulating rubber — and their transportation may also involve specially molded crates or boxes using the same type of material to protect the equipment concerned.
By utilizing insulating rubber in various ways, manufacturers of electronics can develop a complete strategy for controlling ESD. Insulating rubber protects electronic equipment throughout the manufacturing process — from anti-static mats that provide basic safeguarding to insulating gloves and barriers that offer more complete protection.
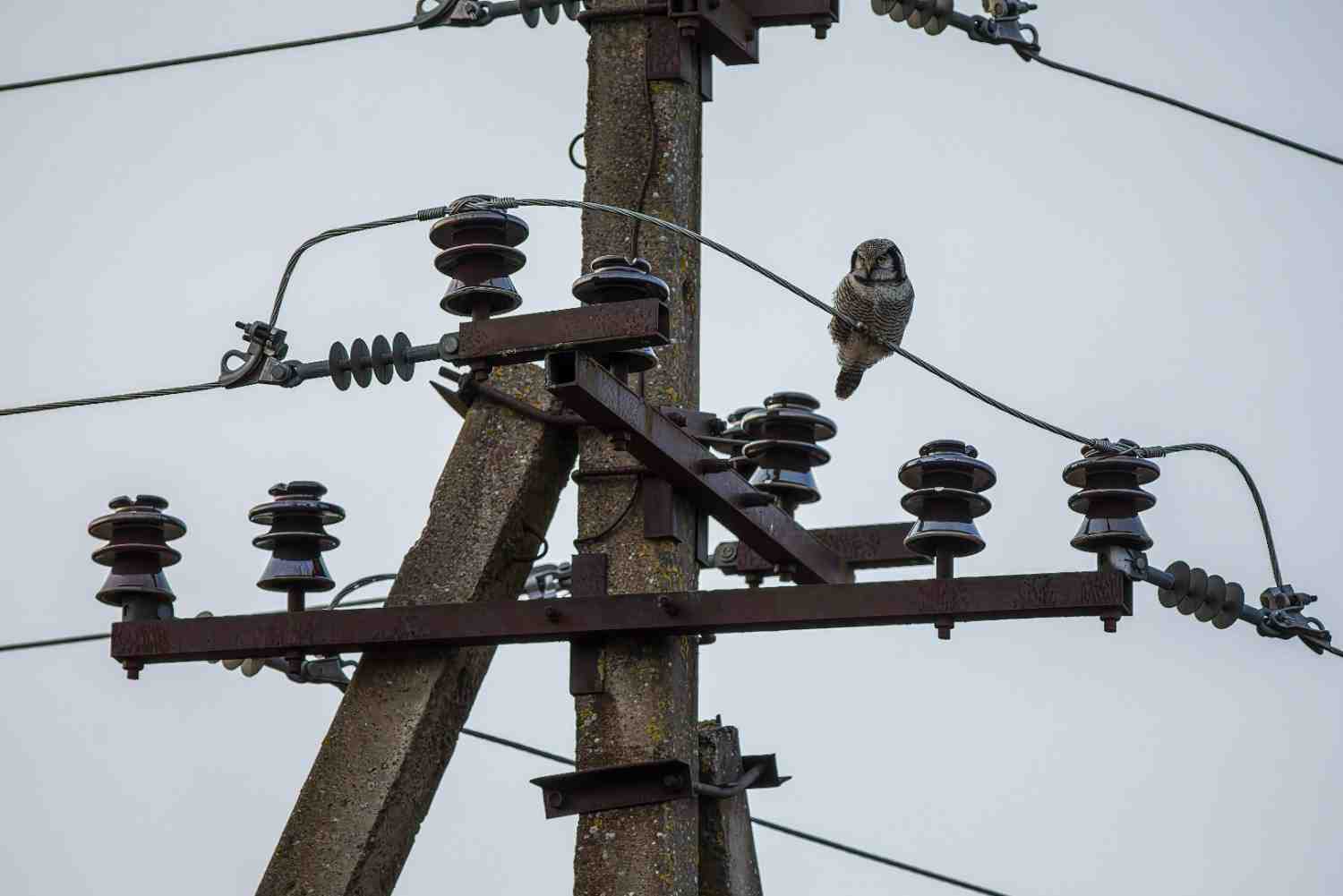
Real-World Victories in ESD Control with Insulating Rubber
In actual manufacturing settings, the practical benefits of using cutting-edge insulating rubber are clear to see. Below are details from two case studies which demonstrate how materials like these can make a real difference:
From Frustration to Efficiency – A Smartphone Manufacturer’s Journey
Challenge: A major smartphone maker was having an ongoing issue – lots of components failing when they were being put together. Further examination showed that the problem was electrostatic discharge (ESD) making the assembly line stop because things weren’t working. This was causing delays (things being late), extra money to be spent, and annoyance among staff — some of whom had not much to do (if anything at all) while production halted for checks/repairs!
Solution: The manufacturer collaborated with an expert in ESD control to create a thorough plan using high-tech insulating rubber parts. This involved:
- Swapping out regular floor mats for insulated rubber ones that are super-efficient at preventing static build-up.
- Giving workers specially designed gloves and wrist straps, also made from rubber compounds but with added ingredients to improve electrical resistance — so they don’t get shocked on the job.
- Changing over workstations so tools no longer touch metal surfaces directly (which can cause damage); now there are holders made out of an insulative type material as well as trays for holding onto components without zapping them by accident!
Results: Thanks to advanced insulating rubber parts, using this ESD control plan had some great results:
- Reduced Component Failures: Because of ESD, these fell by 40%. So there were fewer hold-ups in making things, they were better made – and it saved a lot of cash too!
- Enhanced Production Efficiency: Manufacturers saw all-around better flow through production lines when there weren’t so many ESD problems; they could meet what clients wanted with time to spare (be more effective) – and stay ahead on costs.
- Improved Worker Morale: Simply switching strategies meant less grumbling from workers fed up with stopping/starting jobs because something had gone wrong via an electric charge; it created a sunnier atmosphere for everyone – and they got more done.
Impact: In this case study, we see how using high-tech insulating rubber can completely change the game when making electronics. The smartphone industry giant made things faster, and better – and saw its profits soar! How? By putting static-reducing materials at the top of its checklist.
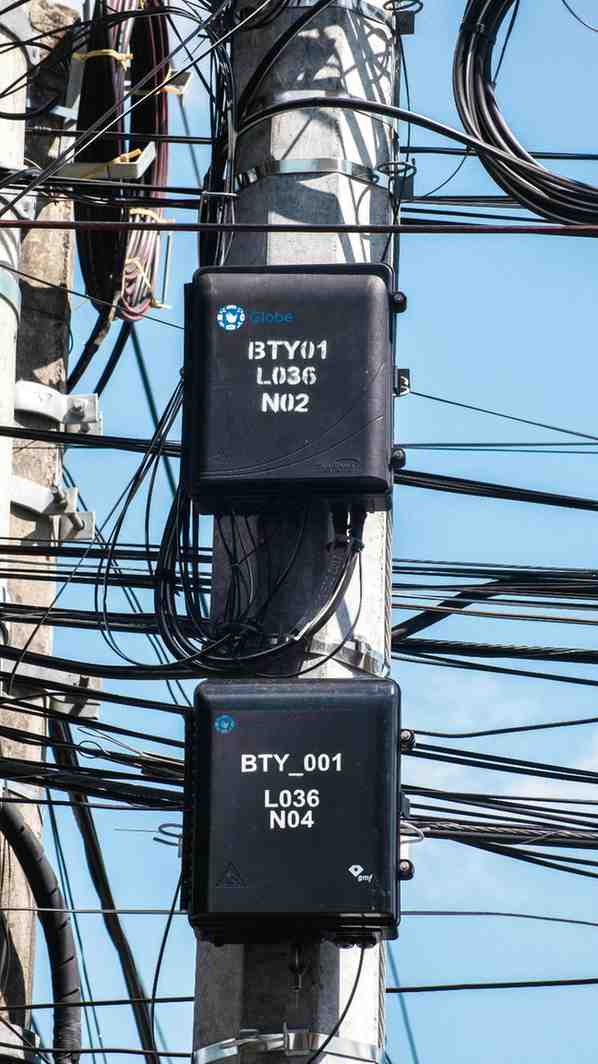
Speeding Up Semiconductors – A Chipmaker’s Success Story
Challenge: There was an ongoing issue at a semiconductor manufacturing plant where production would slow down because of Electrostatic Discharge (ESD) events. When this happened, it caused delays and led to wasted materials and increased costs.
Solution: The factory wanted to solve these problems so took a few different steps. It decided to focus on using advanced insulating rubber in various ways:
- Installing a custom-designed ESD control workstation equipped with an anti-static work surface made from high-resistivity insulating rubber.
- Implementing a system of conductive bins and transport containers crafted from insulating rubber compounds to prevent static charges from accumulating during chip handling.
- Training workers on proper ESD control procedures and ensuring they utilize the newly implemented rubberized components effectively.
Results: The strategic use of advanced insulating rubber yielded significant benefits for the semiconductor plant:
- Increased Production Efficiency: With a drastic reduction in ESD-related issues, the plant experienced a 30% increase in production efficiency. This allowed them to ramp up production and meet growing market demands.
- Reduced Waste: The plant significantly lowered production waste by minimizing ESD damage to delicate chips, leading to cost savings and a more sustainable manufacturing process.
- Improved Quality Control: Enhanced ESD control safeguards ensured the production of high-quality semiconductors, boosting the plant’s reputation within the industry.
Impact: These real-world examples showcase how important insulating rubber is for protecting delicate parts in complicated semiconductor production – and how using it has helped improve performance and efficiency.
Thanks to these special substances, the facility also cut waste; things that would have been scrapped are now good. Product quality has gone up too. In practice this means advanced insulating rubber isn’t just sitting there when smart electronics get made: it helps things run smoothly – which can also mean more profit!
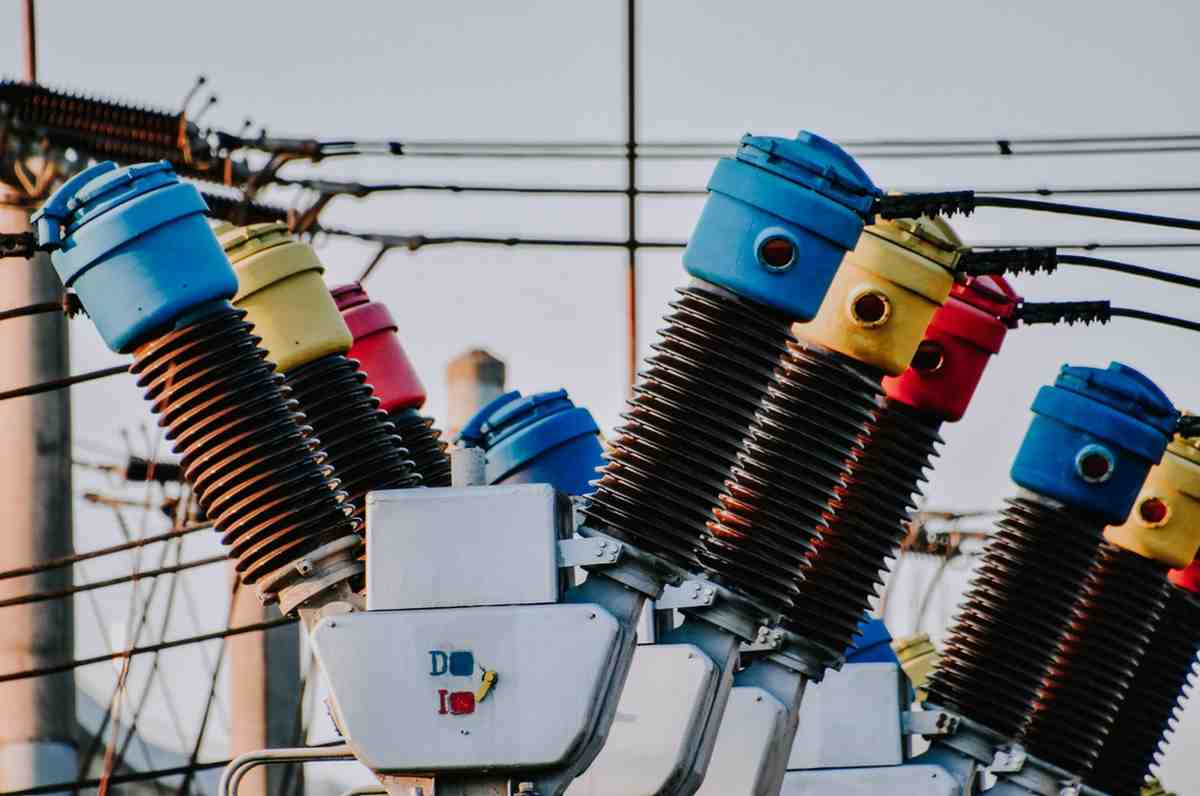
Conclusion
This article has explored the world of insulating rubber and its important role in protecting electronic devices. It has shown how static electricity — which can’t be seen but can cause chaos by damaging parts and halting production lines — is dealt with by using a form of rubber that resists high voltages; can be made into tough, flexible materials; and does not itself become charged.
Such products include matting or flooring that does not store energy; safety gloves that let wearers handle delicate components without risk of damage from shocks; and covers for machines or tools which are all part of what the industry calls an “ESD control program”.
Real-life examples have been used to illustrate the benefits of these hi-tech rubbers: Firms making mobile phones have seen battery failures fall by up to 40% while semiconductor plants report up to 30% less wastage because chips do more work before they break down.
Electronics companies, production managers, safety officers, and buyers all want reliable products: If adopting comprehensive strategies based on advanced insulating materials can help achieve this – as well as make things work better.
You can reach out to our customer support and get unrivaled deal and answers.