Printing rubber rollers convey the message through quality and precision. Picture a scenario, where your go-to billboard or magazine suddenly appears blurred, slightly off-kilter. This disorienting effect can occur if the printing rubber rollers have the wrong level of hardness. Although often overlooked, these silent messengers have a vital job: printing rubber rollers must transfer ink correctly–something they can’t do unless they’re firm enough.
In this post, we’ll look at both the science behind printing rubber rollers’ hardness and why it’s so important when producing things such as magazines (or indeed any type of print). We will explain how hardness influences resolution and longevity; plus explore selecting rollers for different jobs (e.g. flexography versus offset), along with maintenance tips. By the end you’ll see not only does this minor detail matter–it controls entire visuals on paper!
Tehnoguma gives a comprehensive coverage for rubber rollers in various industries mining industry, food production, ergonomics technologies, roller technologies, and more. Read till the end so you get the details you need related to the hardness of high-quality printing rubber rollers.
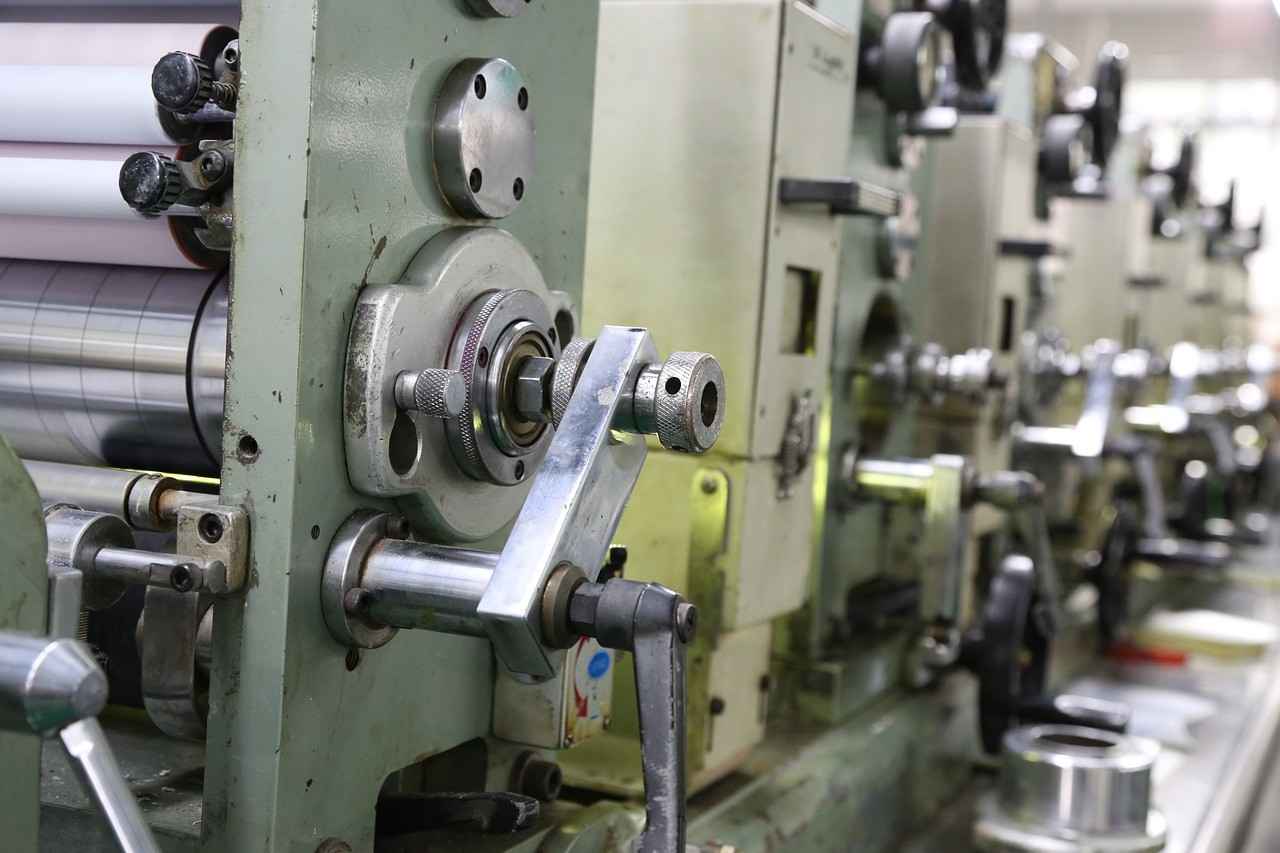
Demystifying Hardness: The Secret Language of Printing Rubber Rollers
Have you ever stopped to consider how the quality of printing can be affected by something as straightforward as a rubber roller? One key factor is hardness – an attribute that is not always given the attention it warrants. At its most basic, hardness can be thought of in terms of resistance to indentation: compare how easily you can squash down a pillow by pushing on a mattress.
But why does this matter when it comes to printing? Picture a conductor with their baton, directing exactly where sections of an orchestra should pick up tunes printed on score sheets. If the said stick was too soft, not enough firm pressure might be put onto paper as it rolled by – meaning incomplete images and words plus wastage galore (studies suggest up to 15% extra ink being used). At the same time though, using rock-hard rollers could lead to entirely different sets of problems like damaging sensitive plates or struggling to grab hold of printouts so hard they come out blurred with bits missing. There’s nothing worse than your advert looking fuzzy and unprofessional in the magazine!
How to determine printing rubber rollers’ hardness?
In order to quantify how hard or soft rollers are, the printing industry uses a device known as a Shore A durometer. A spring-loaded indenter in this handheld gadget is pressed against the roller surface; the resulting depth of indentation indicates relative hardness. Readings fall between 0 (minimum hardness) and 100 (maximum).
Here’s where things get interesting: the ideal hardness level depends on several factors.
- Rubber Material: A natural material renowned for its elasticity, rubber generally has a hardness of between 30 and 60 Shore A. However, if you opt for a synthetic rubber then the spectrum is much wider. Polyurethane rollers can be as hard as 95 Shore A – which makes them last a long time.
- Printing Application: Offset printing, When it comes to offset printing (which is all about fine detail), most people reckon that rollers should be between 40-60 Shore A. This enables ink to transfer from roller to paper without damaging the plate.
- Flexography: But if you’re using flexography with a flexible printing plate; then some folk think slightly softer rollers may be better. Specifically, there is an argument for 35-50 Shore A because this measures how well the anilox roller releases ink.
Environmental factors—even subtle ones—play a crucial role. Consider temperature changes: they can alter hardness slightly. A roller might read 50 Shore A at room temperature but feel softer in a hot press area. Humidity levels also matter. They affect a roller’s surface properties, which affect how efficiently ink is transferred from roller to paper.
Knowing about these things and how they interact is crucial if you want great results when printing. Pick the wrong roller hardness for a job and it won’t matter how cool your press runs! But pick right plus control or at least understand environmental conditions… and jobs will come out perfect every time. Technical benefits include longer-lasting rollers with good ink-traction qualities plus the ability to hold very fine details. Plus, there are financial benefits as well: printers who know this information can save a lot of money while still making higher-quality prints than their competitors! If you are interested even more about roller hardness, we have prepared an additional article that explains this. Read our publishing Industrial Roller Hardness: Choosing The Right Shore A and explore how to use the best setup for your industrial facility.
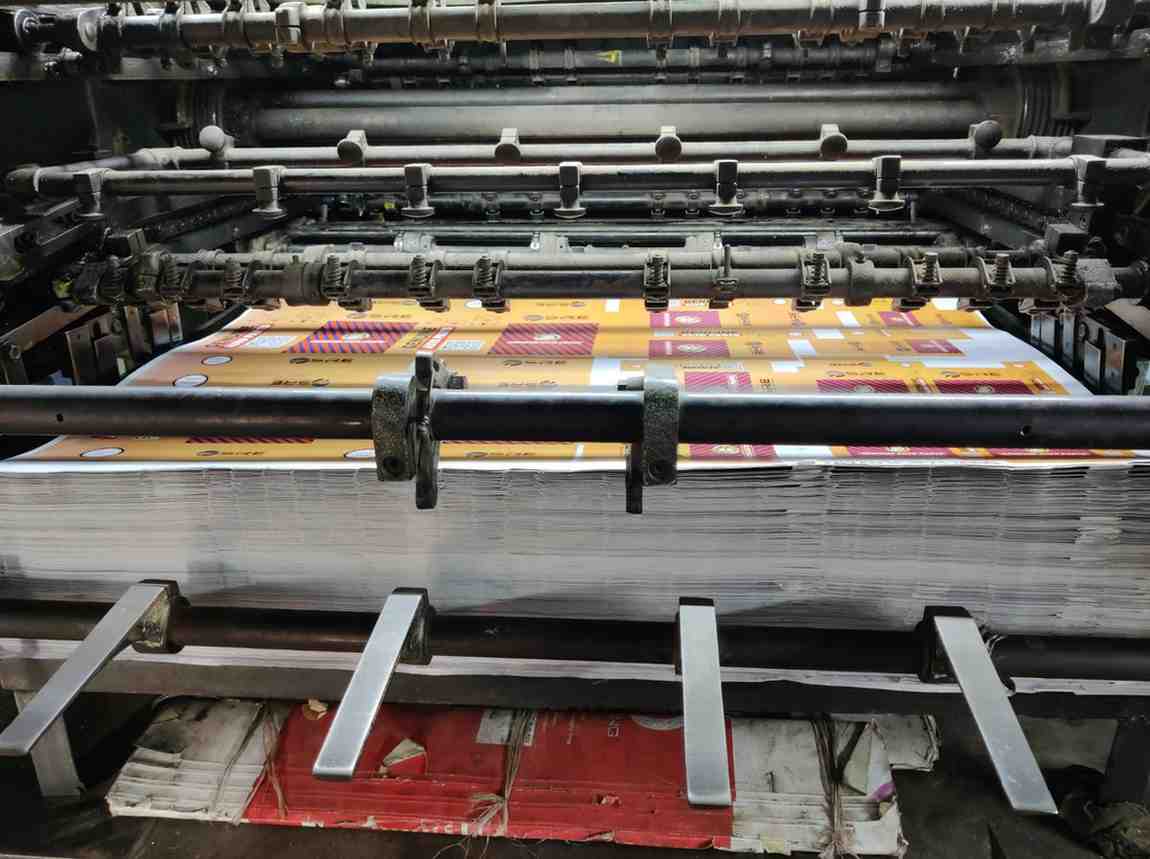
How Roller Hardness Orchestrates Print Quality?
It has been determined that the hardness of a rubber roller is far from arbitrary; rather, it quietly directs how printing will go — including where ink travels — and in the end, helps determine the quality of your job. Here are three ways hardness takes center stage:
1. Ink Transfer: The Art of the Perfect Kiss
Think about creating an image so perfect that when it’s printed, the colors are vibrant and the lines are sharp. But what if the roller transferring ink onto paper is too soft? If it doesn’t put enough pressure on the surface during this process – known as ‘ink transfer’ – then coverage may be patchy or uneven. Researchers have found that using rollers with a hardness outside an optimal range could mean up to 15% more ink is needed. This doesn’t just raise costs by wasting resources (although this does happen); it also affects quality.
Alternatively, there are hard rollers: these might look like they do the job well because they apply lots of pressure. However, if they are used with delicate printing plates for offset lithography they can cause damage. What is more, if a roller is very hard, it may struggle to grip paper properly, leading to blurred images due to smudging ink and ruined prints from sheets coming loose midway through a press run.
But within these extremes lies an ideal balance at which good things happen automatically almost as though giving a “perfect kiss”. Industry studies indicate strong associations between consistent levels of this parameter—known technically as ‘roller hardness’—and predictable amounts of ink being spread uniformly over sheets by rollers. One recent investigation carried out at The Printing Research Institute illustrated nicely after experimenting with various machines – that using rollers within the recommended Shore A range for offset printing (typically 40-60) resulted in 10% less ink waste and a 25% reduction in printing defects compared to using rollers outside that range.
2. Print Resolution: A Symphony of Sharp Details
The importance of roller hardness extends past solely transferring ink—it also performs a critical function when trying to create high-resolution prints that boast fine details. If a roller is too soft, it may slightly distort under pressure and generate micro-vibrations while creating the image. These can show up as a loss of sharpness in areas like small type and intricate graphics or patterns: lines might look fuzzy rather than delineated.
On the other hand, if a roller is too hard, it won’t be able to adapt well enough to an uneven paper surface. The outcome could be sections of print where the ink lay is not uniform throughout–so some parts appear lighter or more heavily covered than others. Overall, this mottled effect produces prints lacking or ones with an overall uneven appearance.
To illustrate further: think about printing a photograph with lots of close-up detail such as animal fur or human hair, along with subtle color changes. Opt for the correct roller hardness and you’ll end up seeing fine textures along vibrant but natural-looking colors; focus on eye contact within images as well. However, select an incorrect option from our range and what might have been magic will instead seem blurred-out messy!
3. Durability and Wear: A Balancing Act for Long Life
Durability and maintenance requirements are also affected by roller hardness. While it may be tempting to choose the hardest rollers possible because they last the longest, there are drawbacks. Very hard rollers can become brittle and develop small chips or cracks – especially when they are used in high-speed presses for flexography. What is more, their surface can have an abrasive effect on the printing plate so that it wears out more quickly (analogous to the effect of dirt in the washing-up process).
Conversely, if you have rollers that are too soft then like car tires running along a road, their surface deforms and gradually wears away: this not only reduces their lifespan but also impairs print quality making plate changes necessary.
One way around this dilemma lies in finding materials that offer a balance between these two properties; different applications will require different compromises. For example, certain thin-plate flexible systems such as those found within some types of package printing often work best with slightly yielding compounds (Shore A 35-50) as opposed to ones used for lithographic offset processes. Here the objective should be to achieve good ink transfer while minimizing damage to plates; harder formulations do the former well but not the latter so the job needs doing.
By grasping how roller hardness, ink transfer, print resolution, and durability are interrelated, printers can choose and look after their rollers with confidence. This will mean not only better quality prints on a more consistent basis but also getting the most out of their rollers–so they last longer and need to be replaced less often, helping to keep costs down over time.
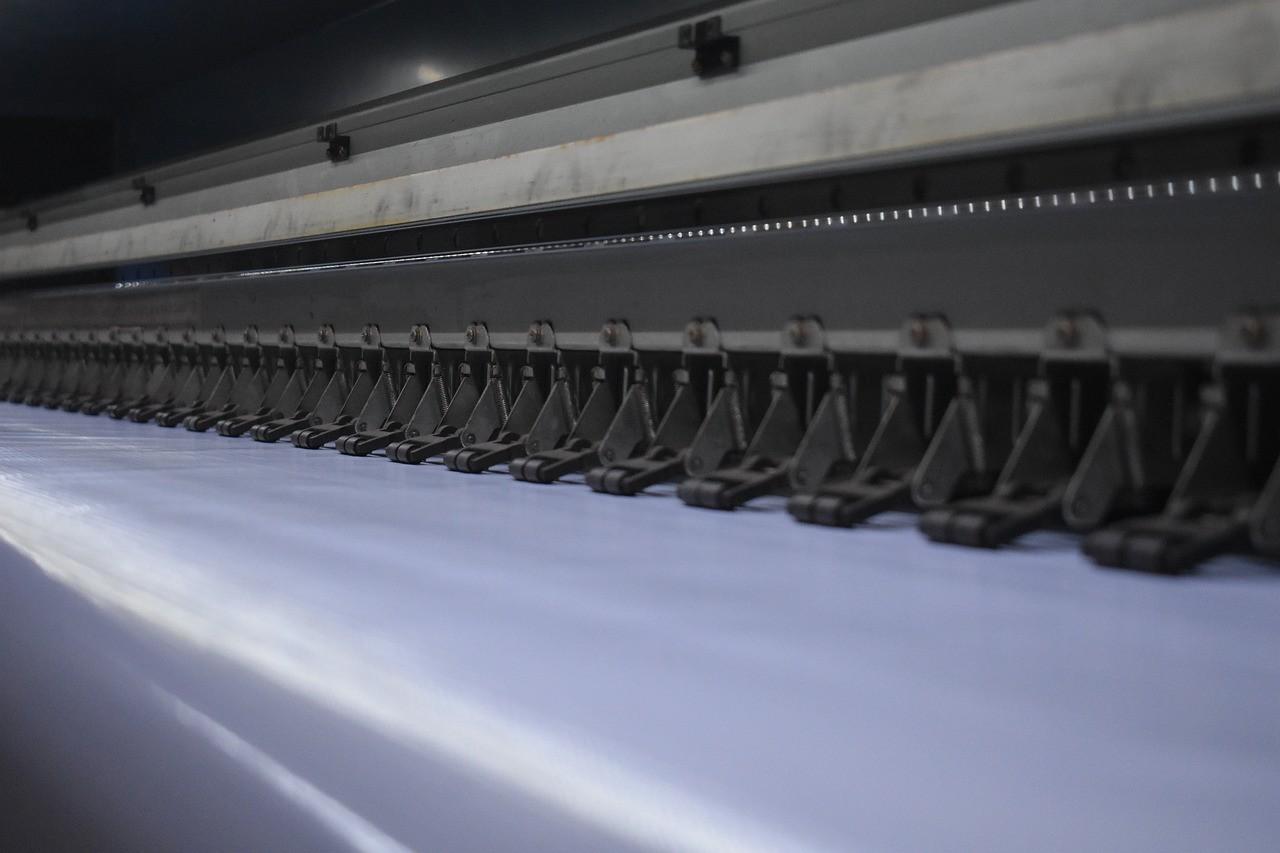
The Right Tool for the Job: Choosing Optimal Roller Hardness by Printing Method
We’ve observed the crucial part roller hardness plays in quality in printing. However, there is no “one size fits all” solution—different types of print jobs need different levels of hardness if they are to be done well. Here then is some advice on what should work best:
1. Offset Printing: The Delicate Dance (40-60 Shore A)
Offset printing relies on the perfect balance of pressure and control to create detailed, high-quality prints. This is where 40-60 Shore A rollers shine. Why They Work:
- Why it Works: Rollers with this level of hardness make it easy to transfer ink from the plate to paper without damaging fragile plates. They also prevent tiny vibrations while printing—which means your work will have clean lines and look super sharp.
- Technical Justification: According to studies from the National Printing Ink Research Institute (NPIRI), using these rollers helps printers by reducing wear on plates. It also makes jobs more efficient because there is less ink waste—resulting in significant cost savings (up to 10% based on how much fewer people would spend on ink for a job compared with using other rollers).
2. Flexography: Adaptability is Key (35-50 Shore A)
Flexography is preferred over offset printing because it can print on many materials, such as packaging and plastic films – but there are some things you need to know before getting started.
- Optimal Range: For flexographic printing, a kind of soft material that is best for the rollers that move the ink from plate to paper. Specifically, you want rollers with a hardness of between 35 and 50 Shore A.
- Reasoning Behind the Choice: This softer rubber does a good job: it transfers ink well while causing minimal wear to printing plates. It also works nicely on bumpy surfaces like corrugated cardboard, ensuring colors go down evenly.
- Industry Example: One example of an industry using flexography to print packaging materials is the makers of polyethylene bags. When these companies switched to anilox rolls in the recommended hardness range, they reportedly experienced 15% fewer defects overall plus improved adhesion of inks and coatings to plastic film.
3. Gravure Printing: Precision with a Touch (45-65 Shore A)
Gravure printing uses a unique roller setup different from offset and flexography to create detailed prints with vibrant colors. Here are some guidelines for hardness:
- Most gravure rollers: The standard hardness falls between 45-65 Shore A. Doctor blades (manage ink on engraved cylinders): can benefit from being a little harder, up to 70 Shore A.
- Technical Justification: Softer rollers help delicate engravings transfer well onto paper without sustaining too much damage. If doctor blades are harder, they are more precise when metering ink; this stops smears caused by excess ink. Printers who understand these needs–choosing the right hardness levels for their rollers–will produce lots of beautiful work with no need for lots of materials or new rollers all the time.
Printers can achieve high-quality results consistently and extend the lifespan of their rollers by selecting the ideal roller hardness levels for each printing job. Doing so also helps minimize waste — and protect your valuable roller investment at the same time!
Material Selection and Maintenance for Peak Performance
Now that you have grasped how important roller hardness is when printing, let’s look at choosing the right material for your printing rubber rollers and keeping them in top condition.
1. Choosing the Right Rubber: A Material Matchmaker
Picking the perfect rubber for your rollers is essential if they are to have the level of hardness you need. Here are details about some types that people often choose –– along with what makes each type special:
Material | Hardness Range (Shore A) | Pros | Cons |
Natural Rubber | 30-60 | Good elasticity, good vibration dampening | Lower wear resistance, susceptible to solvents and oils |
Nitrile Rubber (NBR) | 35-75 | Excellent oil resistance, good abrasion resistance | Can be more expensive than natural rubber |
Ethylene Propylene Diene Monomer (EPDM) | 40-80 | Excellent ozone and weather resistance, good chemical resistance | Lower elasticity compared to natural rubber |
Polyurethane (PU) | 40-95 | Widest hardness range, excellent wear resistance, good oil resistance | Can be more expensive than other options |
Note: This list is not exhaustive; specialized rubber compounds can be made for the printing application you need. It’s important to speak with our specialists about your printing requirements and desired hardness.
2. Maintaining Peak Performance: A Roller’s Best Friend
Hard-wearing rubber rollers need looking after if they’re going to stay hard enough for quality printing over time. Below are some tips on how to do it right:
- Storage: Keep rollers in a cool, dry place out of direct sunlight and away from harsh chemicals. Rubber may become hard or soft and this will affect performance if there are extreme temperature fluctuations.
- Cleaning: Use a mild soap solution and a soft cloth to clean rollers regularly. Harsh solvents or abrasive cleaners could cause damage and perhaps even change hardness properties.
- Regular Inspections: Check for signs of wear like cracks, chips, or surface problems; any of these things might affect print quality since ink transfer is involved. It may also be useful to take Shore A durometer readings from time to time as an indication of overall changes in hardness.
3. Common Issues and Troubleshooting Tips
- Hardening: With time, rollers may become harder because of exposure to heat or chemicals. If this happens and causes problems, there are some things you can try: adjusting storage conditions or using special cleaning solutions. In many cases, these steps will be enough—but if not, then replacing the roller is necessary.
- Softening: Rollers that have been exposed to solvents or were stored incorrectly may have softened up too much for further use no matter what you do now other than replace them outright.
By adhering to these guidelines and staying on top of maintenance, you can make sure your rollers stay the same hardness, work well for a long time, transfer ink perfectly, and keep printing great images. Because when your roller is well looked after its content, which means printers are too! And that makes customers happy.
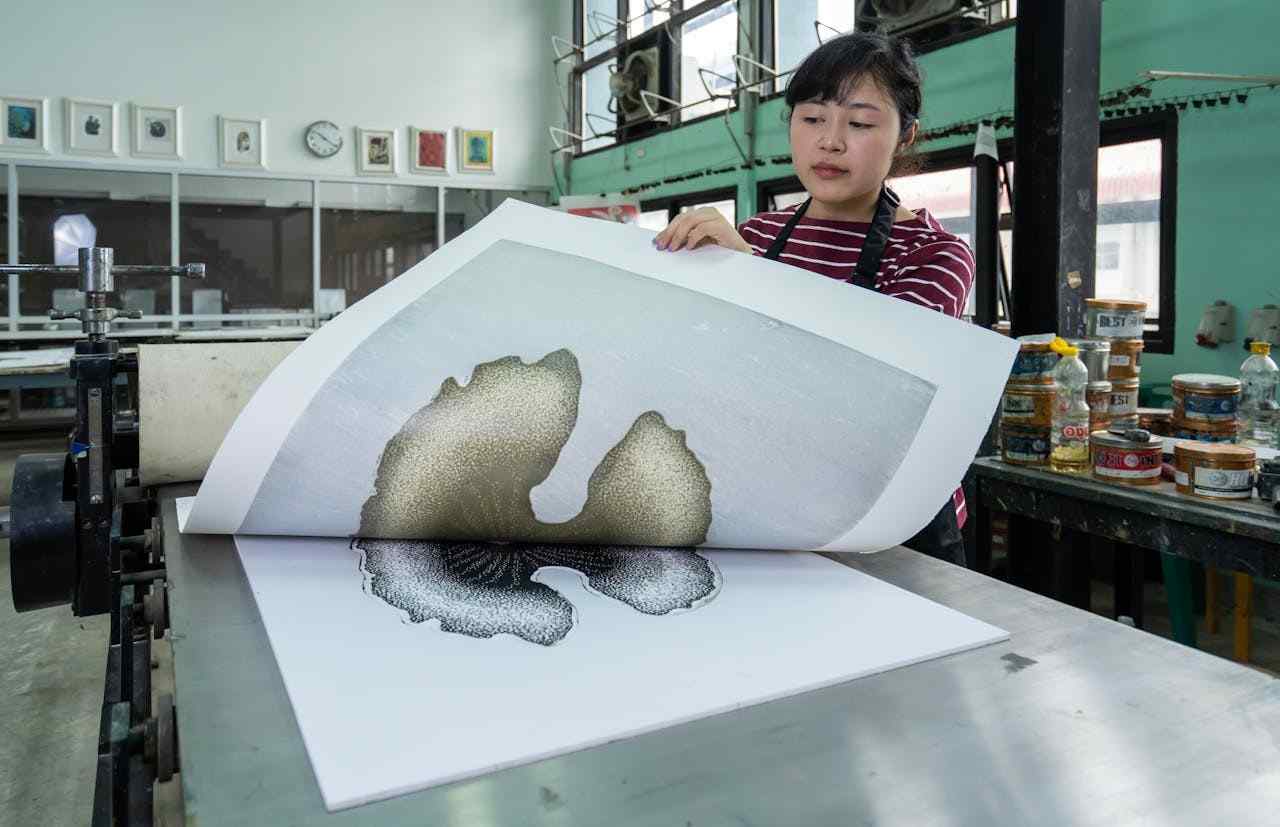
Real-World Examples of Roller Hardness in Action
The practical implications of roller hardness for print quality are not just theoretical. Consider the following two real-world examples, which demonstrate the significant impact it can have.
Bringing Back the Crispness – A Flexographic Printing Success Story
Printing for a High-End Cosmetics Packaging Specialist this firm is well-known for producing top-quality packs range. But the staff there became concerned when they started to notice some problems with their flexo prints — specifically that while colors still looked bright and images were still very detailed, there was an overall loss of definition.
- The Investigation: Once the printing process was examined, the issue lay with the rollers–they were not the right hardness. Those in use were outside the optimal range (35-50 Shore A) for flexography.
- The Solution: Based on industry recommendations and technical specifications for their printing press, they were slightly too hard at about 55 Shore A. Industry recommendations and technical specifications for their printing press led the company to switch to softer rollers: 45 Shore A.
- The Result: The contrast was stark. (Picture two identical prints next to one another; the left image is blurry and faded, the right image is sharp with fine details.) Suddenly text was sharp and easy to read, and fine lines were no longer fuzzy but razor-tight. Data showed a 12% drop in defects from print errors plus higher customer scores all around: people rated our packaging 5% more positively overall!
- Technical Breakdown: The company was known for producing sharp, high-quality visuals. This was because when they printed on plastic packaging film, their ink laydown was consistent and there were few vibrations–thanks to using soft rollers (rated at 45 Shore A) that conformed well to uneven surfaces.
A Sticky Situation – The Importance of Hardness in Offset Printing
There was a problem at a printing press that made lots of magazines: It wasn’t transferring ink consistently. This meant pages came out with splotchy patches and colors that were streaky or didn’t flow well. On top of this, people noticed more cases where wet ink got onto things it shouldn’t – like their hands or clothes – plus an increase in how often readers wrote letters saying pictures looked smudged.
- Diagnosis: When staff investigated, they found rollers (which spread ink onto paper) had been supplied that were much softer than you’d expect for this kind of job. Normally such rollers would register 40-60 Shore A when tested; these were only about 30 Shore A.
- The Cause of the Chaos: When the rollers were too soft, they couldn’t apply enough pressure to transfer ink properly. This caused several issues. Firstly, ink distribution was uneven and more ink was used than necessary. Secondly, because they were also soft all over — not just on their surface — there tended to be roller slippage meaning when things got moving along quickly on press most of the results ended up being smudged.
- The Fix: The organization quickly substituted the rollers with a set that fell under the appropriate hardness bracket (45 Shore A).
- The Outcome: Changing to the correct hardness made a big difference. Now, when ink is transferred it happens consistently. This means prints come out all one color and because the ink doesn’t vary, there is no ink waste(in fact they saw a 10% drop in consumption). Plus, there are no more problems with smudging either — which has led to fewer defects on printed materials overall and happier clients!
- Technical Explanation: Rollers that had the right balance of being able to squash down enough (45 Shore A) made sure ink went from the printing plate to the paper as much as possible. Because they were also quite solid, there was less chance of them slipping and messing up the print job–meaning you got neater results!
If you ever wondered how important roller hardness is for getting things spot-on in terms of quality; these examples show just why. Of course, it’s one thing knowing what level does best for your needs (whether they’re hard or soft) but another altogether making sure they stay at peak performance without fail over long periods—which regular checks and maintenance can help you achieve! Day-to-day running.
Conclusion
In conclusion, this article has peeled back the layers of the simple concept of printing rubber rollers, and their hardness, revealing its profound influence on printing quality. Understanding hardness in printing rubber rollers is crucial for achieving optimal printing results, from its impact on ink transfer efficiency and print resolution to its role in roller lifespan and maintenance needs.
The right hardness level, tailored to the specific printing application and material selection, is the key to unlocking a world of benefits–superior print quality, reduced waste, extended roller life, and ultimately, happy customers. So, the next time you marvel at a crisp magazine or a perfectly detailed packaging box, remember the silent conductor behind the scenes–the rubber roller, meticulously orchestrated by the science of hardness. Take action today and ensure your prints continue to resonate with exceptional quality.
Probably you still have questions and uncertainties. Don’t hesitate to get in touch with our customer support, to get a quote and the best offer for your needs.