Mining operations are tough on equipment. Every scoop, crush, or haul inflicts harsh conditions and wear and tear via abrasion and impact. That’s where rubber compounding comes in. This article—written for equipment manufacturers, procurement managers, and mining engineers—discusses the role of rubber compounds in dealing with these issues so that machinery lasts longer and performs better. We will demystify some technical aspects of rubber formulations while showing how they can improve both performance and longevity in mining settings.
With Tehnoguma we cover multiple industries mining industry, food production, ergonomics technologies, roller technologies, and more. Read to the end to become informed with the details you need and make the best decision for your needs.
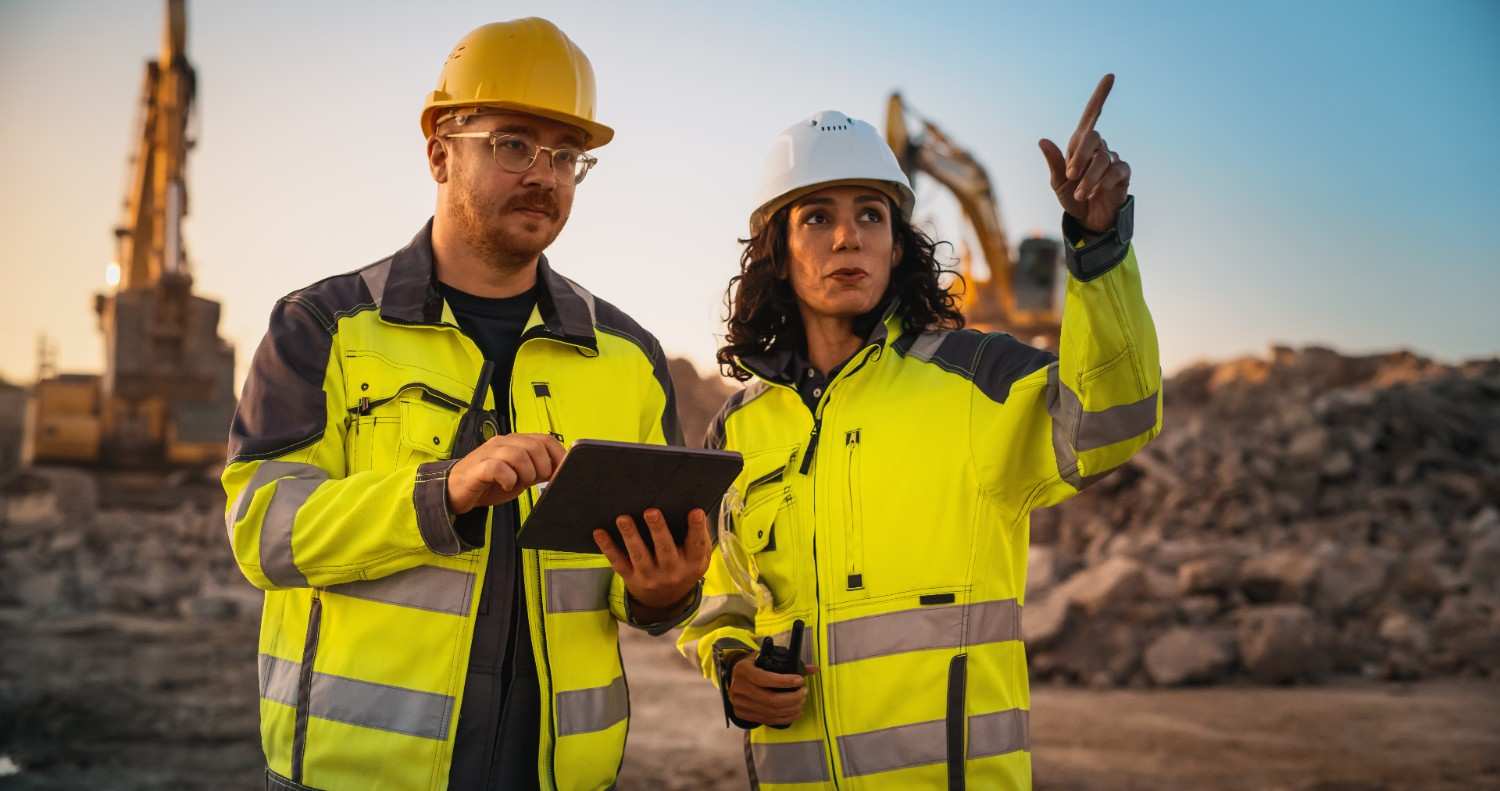
What is Rubber Compounding?
In a world where digging ore could destroy your mining gear, rubber compounding is a lifesaver. It might not be magical, but it’s a kind of alchemy that transforms ordinary materials into customized warriors–rubber warriors–capable of withstanding the harshest conditions underground.
Why is Rubber Compounding Crucial? The Numbers Speak for Themselves.
Just look at the facts. Research shows that steel equipment without rubber lining can wear away by as much as 10mm every year in abrasive environments. The result? Miners need to replace things constantly, which costs a fortune in lost productivity because operations have to stop all the time. This is where rubber compounding rides to the rescue. Developing compounds with outstanding resistance to wear and tear, enables machinery to last much longer than you’d ever dare hope. Properly formulated rubber linings may reduce annual wear rates by an astonishing 90%, meaning equipment endures 5 to 10 times more use. That represents a huge efficiency gain and serious money saved for mining companies everywhere.
A Historical Perspective: Rubber’s Longstanding Role in Mining
Rubber and mining have a longstanding relationship. Centuries ago, people discovered that natural rubber was both stretchy and tough – an ideal combination for conveyor belts, chute linings, and mill feed hoppers. Those early users helped create the type of compound that is essential to mining today.
Building the Champion: Key Ingredients of a Mining-Ready Rubber Compound
Consider this comparison: Just as a cake needs certain ingredients, and a cocktail requires precise mixing, there are key elements needed if you want to combat wear and tear in mines. Here we’ll take a closer look at what goes into making a successful recipe:
- Polymers: The Foundation (and the Muscle) – These are the building blocks of the compound, providing strength along with elasticity and flexibility. Different polymers are used in mining, each bringing something special to the mix:
- Natural Rubber: The traditional choice, valued for its high elasticity and resistance to tearing (you’ll find it in conveyor belts).
- Styrene-Butadiene Rubber (SBR): A cheaper alternative that works well across the board–good value for money when general-purpose wear is an issue.
- Nitrile Butadiene Rubber (NBR): Likes nothing better than getting dirty with oils and greases; performs brilliantly in these environments plus those involving abrasion (chute linings spring to mind).
- Ethylene Propylene Diene Monomer (EPDM): Can cope with the rough and the smooth! Excellent resistance qualities to harsh weather conditions have led to its use in outdoor mill feed hoppers where there may also be chemicals with which other rubbers struggle.
- Fillers: The Reinforcements – They don’t just take up space Think of these reinforcements as being like tiny soldiers who help strengthen overall ranks. Incorporating fillers such as carbon black, silica, and clays boosts wear resistance (a material’s ability to withstand surface deterioration caused by rubbing or friction) while also bringing down costs by volume. However, both the type and quantity of filler used will have a significant effect on various properties exhibited by the final compound.
- Curing Agents: The Backbone Builders – These essential components kick-start vulcanization–a process during which rubber molecules form cross-links (essentially bonds) that cannot be broken without the application of heat. By creating more of these cross-links, curing agents vastly increase strength durability over non-vulcanized rubbers i.e. those which have only been heated molded but not had further heat applied afterwards.
- Additives: The Fine-Tuners – Giving nature a helping hand Specialised ingredients known as collectively additives do not feature prominently within the article because their roles tend towards fine-tuning things behind the scenes–helping each compound reach optimum performance levels from the moment it is put to work. For instance, antioxidants fight against degradation caused by heat, and light flexing; anti-ozonants protect from attack by atmospheric ozone; while plasticizers give flexibility or improve workability at time processing.
Far combining and selecting carefully from these four different groups of ingredient categories listed above, rubber technologists can create compounds specifically designed to conquer the wear and tear challenges of each unique mining environment.
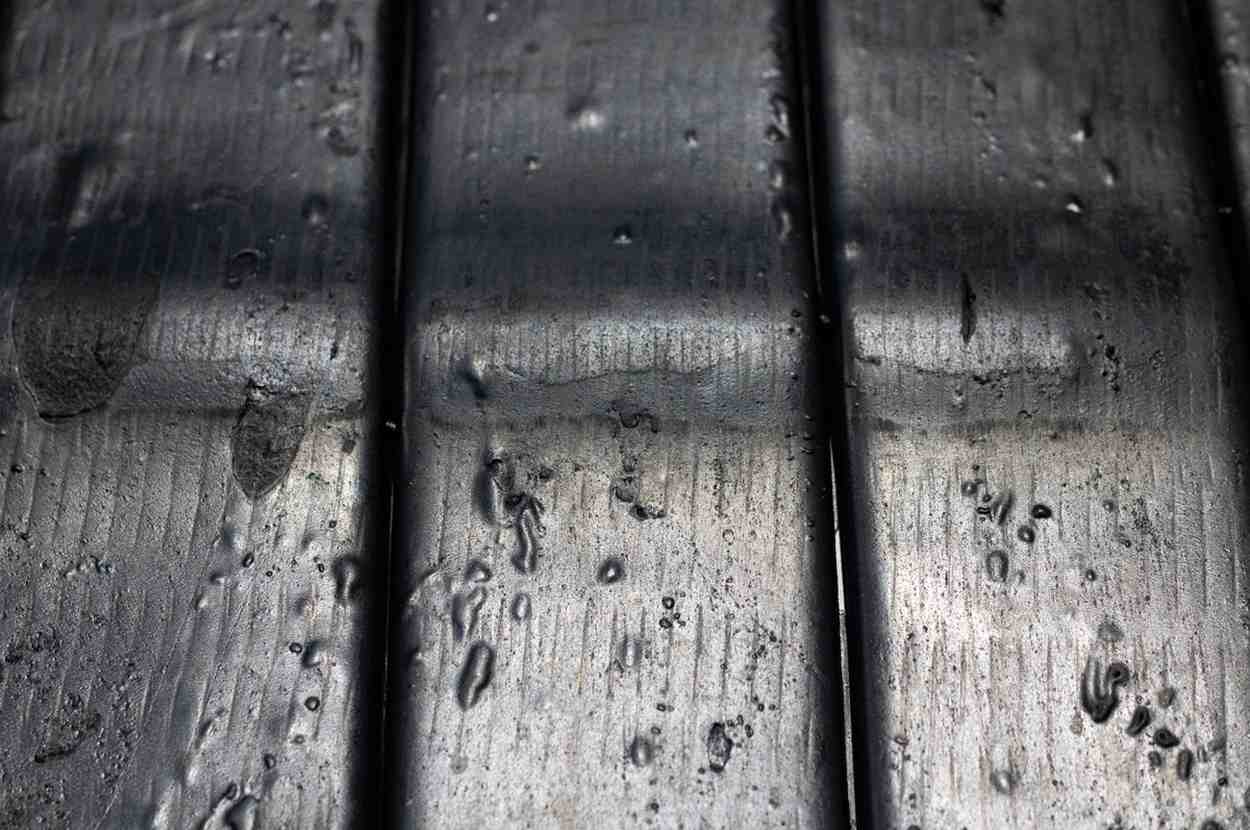
The Process of Rubber Compounding – From Recipe to Reality
Now that we understand the key ingredients, let’s delve into the fascinating process that transforms them into a powerful weapon against wear and tear: rubber compounding.
Formulating the Perfect Blend: Selection and Science
The journey begins with meticulous formulation. Compounders, like skilled chefs, carefully select the type and quantity of each raw material based on the desired final properties. This selection process considers factors like the type of mining equipment, the specific wear and tear challenges encountered, and the operating environment. Material selection data and years of experience play a crucial role in creating an effective recipe.
Mixing the Dough: Bringing the Ingredients Together
Once the recipe is finalized, it’s time to get physical! The raw materials are precisely weighed and then combined in massive mixers. Here are two common mixing methods:
- Internal Mixers: Imagine a giant, enclosed blender. These high-powered machines use intense heat and pressure to break down, disperse, and thoroughly blend the ingredients. This intensive mixing ensures a uniform and consistent compound.
- Two-Roll Mills: These consist of two large, counter-rotating rolls. The raw materials are fed between the rolls, where the shearing action incorporates them into a homogeneous mix. This method offers more control over the mixing process but may require multiple passes to achieve uniformity.
The choice of mixing method depends on the specific compound formulation and the desired level of control.
The Secret Ingredient: Vulcanization – The Powerhouse Transformation
Think of vulcanization as the magic spell that activates the true potential of the rubber compound. It’s a chemical process that involves forming permanent cross-links between the polymer chains. This transformation dramatically improves the strength, elasticity, and durability of the rubber. Without vulcanization, the compound would remain weak and susceptible to tearing and wear.
There are two main vulcanization methods:
- Sulfur Curing: The traditional and most widely used method. Sulfur reacts with the rubber at elevated temperatures, creating the essential cross-links.
- Peroxide Curing: This method offers faster cure times and is often used for specialty applications where high heat resistance is required.
Ensuring Quality: The Guardian at the Gate
Rigorous quality control is paramount throughout the compounding process. Samples are taken at various stages and subjected to a battery of tests, including:
- Tensile Strength: Measures the force required to break the cured rubber compound. Higher tensile strength indicates better resistance to tearing and pulling forces.
- Elongation: Evaluate how much the rubber can stretch before breaking. A good balance between strength and elongation is crucial for many mining applications.
- Hardness: Indicates the resistance of the compound to indentation. The optimal hardness depends on the specific wear mechanism encountered (abrasion, impact, etc.).
These tests ensure the final compound meets the desired specifications and can withstand the harsh realities of the mining environment.
By following these meticulous steps, compounders transform raw materials into powerful solutions for extending the life and performance of mining equipment. In the next section, we’ll explore the critical role of wear resistance in the mining industry.
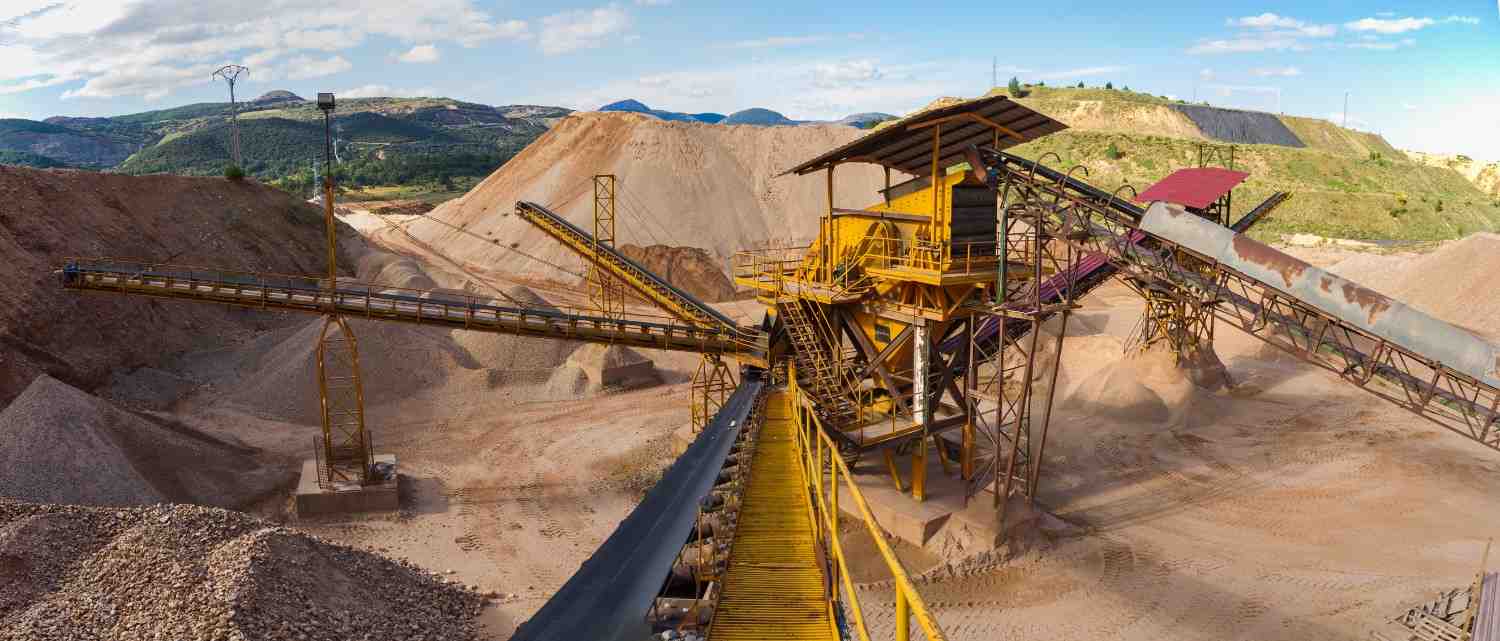
Importance of Wear Resistance – The Achilles’ Heel of Mining Equipment
The relentless battle against wear and tear is a constant struggle in the mining industry. Unlike a mythical hero, mining equipment doesn’t have an invulnerable heel. Instead, its Achilles’ heel lies in its susceptibility to wear caused by a brutal combination of factors:
- Abrasion: Imagine millions of tons of rock grinding against your equipment. This constant friction is a major source of wear, especially for components like conveyor belts, chutes, and mill liners.
- Impact: Blasting and the movement of large rocks subject equipment to heavy impacts. These impacts can cause cracks, fractures, and significant material wear.
- Corrosion: Exposure to water, chemicals, and minerals can lead to corrosion, weakening the equipment and accelerating wear.
Rubber Compounding: When the Wrong Material Costs Dearly
The consequences of inadequate wear resistance can be severe. Here’s a real-world example: a mine using unlined steel chutes experienced rapid wear, leading to frequent breakdowns and replacements. This resulted in $100,000 per month in downtime and repair costs. A switch to properly formulated, high abrasion-resistant rubber linings drastically reduced wear rates, resulting in significant cost savings and improved operational efficiency.
Rubber Compounding: The Wear-Fighting Champion
Rubber compounds aren’t just sitting ducks in this fight. Here’s how they address wear resistance:
- High Abrasion Resistance: Certain rubber formulations incorporate special fillers and reinforcements that significantly improve their resistance to wear caused by friction. Studies show that properly compounded rubber linings can outperform unlined steel by a factor of 10 or more.
- Impact Absorption: The inherent elasticity of rubber allows it to absorb and distribute impact energy, reducing the risk of damage to equipment from falling rocks or blasting.
- Corrosion Resistance: Specific rubber types, like NBR, offer excellent resistance to various chemicals and minerals commonly encountered in mining environments. This helps to protect the underlying equipment from corrosion-related wear.
Rubber Compounding: The Power of Extended Lifespan
The benefits of wear-resistant rubber compounds are undeniable. Data suggests that equipment lined with these compounds can last 5-10 times longer compared to unlined alternatives. This translates to:
- Reduced Downtime: Less frequent equipment breakdowns mean more time spent productively mining.
- Lower Maintenance Costs: Fewer replacements and repairs lead to significant cost savings.
- Improved Productivity: With equipment operating reliably, overall mining productivity increases.
The Rubber Compounding Arsenal: Specialized Solutions for Specific Challenges
Not all wear is created equal. To address this, compounders have developed a variety of specialized rubber compounds, each with its strengths:
- High Abrasion-Resistant (HAR) Rubber: The workhorse of wear resistance, formulated to withstand extreme levels of abrasion in applications like chutes and mill linings.
- Impact-Resistant Rubber: Designed to absorb and distribute impact energy, protecting equipment from damage in areas like dump pockets and loading zones.
- Chemical-Resistant Rubber: Offers superior resistance to specific chemicals and minerals commonly found in mining environments.
By understanding the specific wear challenges faced by each piece of equipment, engineers can select the optimal rubber compound to maximize its lifespan and performance. In the next section, we’ll explore how innovative compounding techniques can further enhance durability in mining equipment.
Pushing the Limits – How Innovative Rubber Compounding Enhances Durability
The quest for ever-increasing durability in mining equipment is a continuous race. While traditional rubber compounds offer significant benefits, advancements in compounding techniques are pushing the boundaries of what’s possible.
The Durability Duel: Understanding the Enemy
Before we explore the latest innovations, let’s identify the key factors that can compromise equipment durability:
- Mechanical Stress: The constant strain of heavy loads, repetitive movements, and high pressure all contribute to wear and tear on equipment components.
- Environmental Factors: Temperature extremes, exposure to sunlight, ozone, and harsh chemicals can accelerate degradation and weaken the rubber compound.
The Innovation Armory: Next-Gen Techniques for Enhanced Durability
Fortunately, the fight for durability isn’t one-sided. Here’s how innovative compounding techniques are raising the bar:
- Nanomaterials on the Battlefield: The incorporation of nanoparticles into rubber compounds is a revolutionary advancement. These microscopic reinforcements significantly enhance strength, abrasion resistance, and tear resistance, leading to longer equipment lifespan.
- Polymer Blends: A United Front: By strategically blending different types of polymers, compounders can create synergistic effects. This allows them to tailor the compound to possess specific properties, like exceptional flexibility at low temperatures or superior resistance to specific chemicals.
Data Tells the Story: The Real-World Impact of Innovation
The benefits of these advancements are backed by data. Studies have shown that equipment utilizing compounds with nanomaterials can experience a 20-30% increase in lifespan compared to traditional formulations. Additionally, advanced polymer blends can significantly reduce maintenance costs by minimizing cracking and wear caused by extreme temperatures or harsh chemicals.
Durability Revolutionized
Let’s look at a real-world example. Mine X, plagued by frequent conveyor belt replacements because of wear and tear, implemented a new compounding strategy utilizing a nano-reinforced rubber formulation. The results were impressive:
- Before: Conveyor belts needed replacement every 6 months, resulting in $50,000 in downtime and repair costs per replacement.
- After: The new nano-reinforced belts lasted 18 months between replacements, leading to a 75% reduction in downtime and repair costs.
This case study exemplifies the transformative power of innovative compounding techniques in extending equipment life and optimizing mining operations.
In the final section, we’ll explore the economic and operational benefits of utilizing advanced rubber compounds in mining equipment.
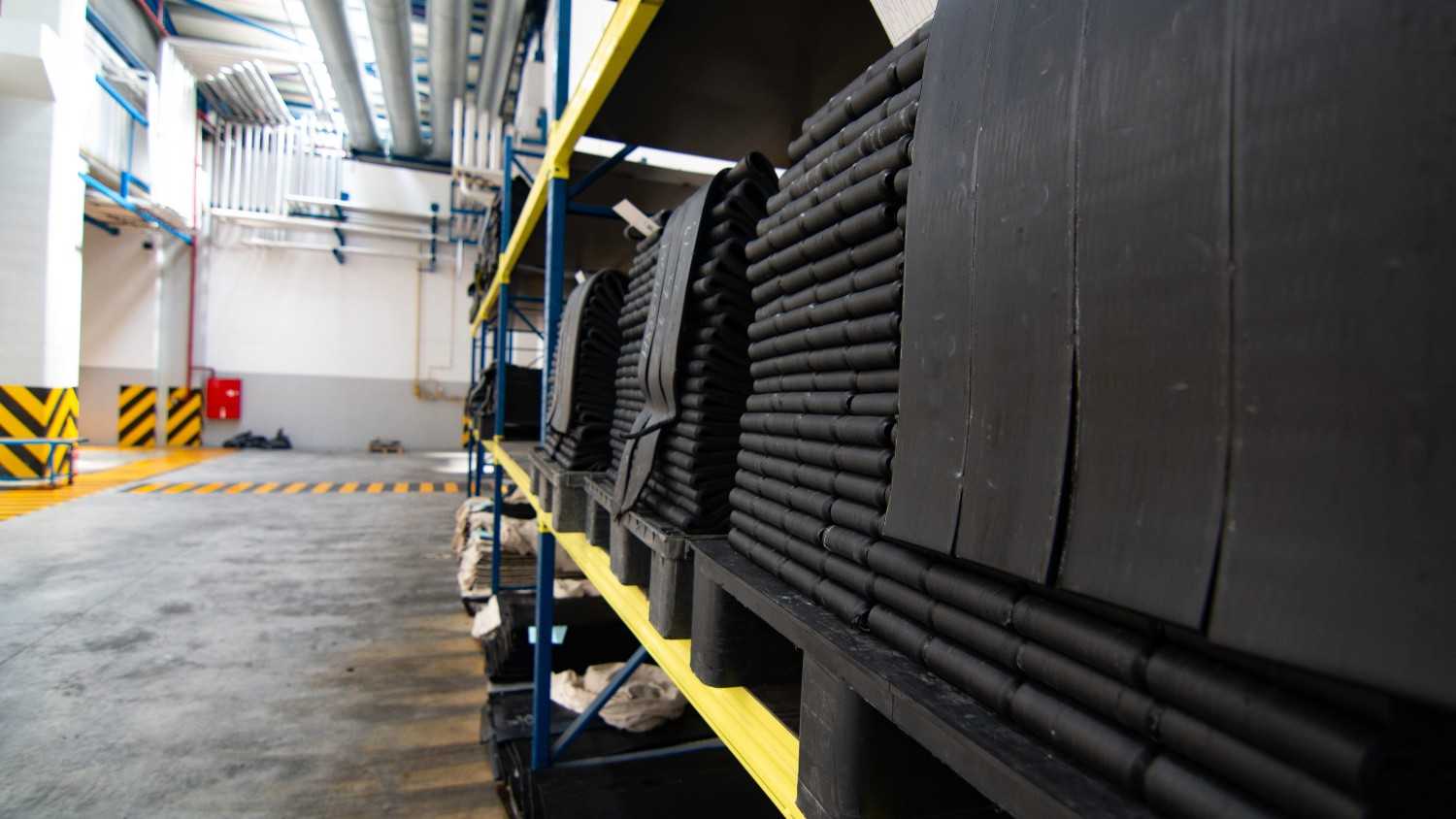
Economic and Operational Benefits of Advanced Rubber Compounding
While the initial investment in advanced rubber compounds might seem higher, the long-term benefits for mining operations are undeniable. Let’s delve into the economic and operational advantages these innovative solutions offer.
Cost Efficiency: A Long-Term Game Changer
The initial cost of a rubber compound shouldn’t be viewed in isolation. Consider it an investment in the future health of your equipment. Here’s how advanced compounds deliver significant cost savings:
- Lower Long-Term Costs: While the upfront cost per unit weight might be slightly higher, the extended lifespan of advanced compounds translates to fewer replacements, drastically reducing overall equipment costs.
- Reduced Downtime and Maintenance: With equipment lasting longer and experiencing less wear, there’s a dramatic decrease in downtime for repairs and replacements. This translates to more time spent productively mining and generating revenue.
Operational Efficiency: A Smoother Journey
The benefits go beyond just cost savings. Advanced rubber compounds contribute to a more efficient and streamlined mining operation:
- Increased Productivity: Reliable equipment that experiences fewer breakdowns means more consistent mining and a significant boost in overall productivity.
- Improved Safety: Equipment failure can pose serious safety hazards. Utilizing durable rubber compounds reduces the risk of breakdowns and potential injuries.
Sustainability: A Responsibility for the Future
The mining industry is increasingly focused on environmental responsibility. Advanced rubber compounds contribute to a more sustainable operation in two ways:
- Reduced Environmental Footprint: By extending equipment life, you minimize the need for frequent manufacturing and disposal of replacement parts. This reduces the overall environmental impact of your mining activities.
- Eco-Friendly Options: Manufacturers are continuously developing new rubber compounds made from recycled materials or bio-based resources. These eco-friendly options offer a sustainable alternative to traditional formulations.
By embracing advanced rubber compounding techniques, mining companies can achieve a win-win situation. They gain significant economic advantages, improve operational efficiency, and contribute to a more sustainable future for the industry.
Conclusion: The Future of Mining is Here
Advanced rubber compounding isn’t just about stronger equipment; it’s about a more profitable and sustainable future for your mine. These innovative solutions dramatically enhance wear resistance, extending equipment lifespan and slashing downtime. This translates to reduced costs, increased productivity, and improved safety. The mining industry is also embracing eco-friendly rubber compounds, minimizing environmental impact.
Tehnoguma can help you unlock this potential. Our team of experts is here to develop customized solutions that will revolutionize the way your mine operates. Contact us today and see how advanced rubber compounding can empower your future.
If you are interested in various equipment needed for the mining industry we also suggest that you go through the comprehensive article Rubber Screens: Sieving Success for Peak Mining Performance and see how we break up the technical details to achieve maximum performance and efficiency.
Still not sure about the details? No worries get in touch with our customer support so you get a quote and your requirements tailored to your needs.