Conveyor belt splicing methods can make a big difference in any production facility. Let’s imagine this scenario – the factory floor thrums with activity. Then, a shriek pierces the air. The conveyor belt, the lifeblood of your operation, groans to a stop. Materials pile up, machines idle, and the clock starts ticking. Every minute the belt down translates to lost production, frustrated workers, and a dent in your bottom line.
The culprit? A faulty splice–the critical connection point that keeps your conveyor belt running smoothly. But fear not, fellow industrial warriors! This guide will equip you with the knowledge to conquer conveyor belt splicing methods and resolve downtimes. We’ll delve into the world of conveyor belt splicing methods, exploring both mechanical splices for quick fixes and vulcanized splices for long-lasting strength. Buckle up, and let’s ensure your production line keeps humming along!
Tehnoguma, with its products and services, supplies industrial rubber to different industries such as the mining industry, food production, ergonomics technologies, roller technologies, and more. Tehnoguma covers a comprehensive industrial rubber supply. Now, let’s see how you can use these different conveyor belt splicing methods to improve efficiency and performance.
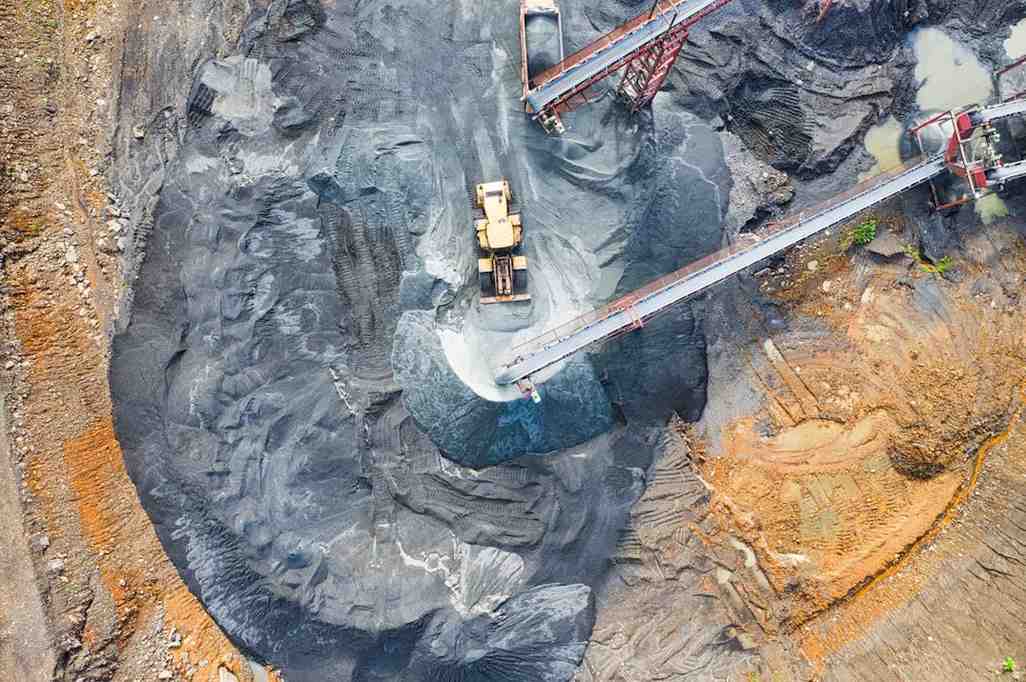
Decoding the Conveyor Belt’s Anatomy: The Hidden Complexity of Splicing
Conveyor belt splicing methods will give the best performance results for your machinery. Though it appears basic, a conveyor belt is a feat of engineering. To choose the right way to join one belt to another, you must know how it is built–so let’s go under the surface:
Like Muscles in an Arm: Fabric Layers and Body
If you were to cut one open (please don’t), you would find that most belts have layers of strong fabric such as nylon or polyester making up their “body”. Just like muscles, these give belts strength (technically called tensile properties). Depending on how many layers there are, belts can carry different amounts of goods. All these layers are held together by a cover of rubber which also does the protecting bit.
Protective Layers: Rubber Coverings
Just as our muscles are protected by skin, a belt has rubber ‘covers’ top and bottom that do a similar job. What makes the covers varies according to where they will be used. For instance, those going over rollers at a coal mine may need to resist abrasion; ones zipping along carrying freshly baked bread from a bakery oven have to be heat resistant. Knowing about components such as these is vital when choosing how best to join two belts together. One method worth considering is its strength efficiency plus how long maintenance staff will take to splice (join) not only covers but also all-important body parts.
A Comparison of Conveyor Belt Splicing Methods & Techniques
When a conveyor belt stops moving, every second counts. To keep downtime to a minimum and get an operation back up to speed fast, choosing the right repair option is essential. Here we take an in-depth look at two major players in splicing methods: vulcanization and mechanical splicing. Mechanical Splicing equals quick fixes with staying power? If vulcanization is surgery, mechanical splicing is first aid. It won’t hold up forever under heavy use – but it will do the job for minor damage fast.
Types of Mechanical Splice
There are three primary kinds:
- Staple Splices
- Finger Splices
- Bolt Splices
Tough Cookies Metal splice plates are bolted onto the overlapping ends of a belt to clamp them together effectively. These provide the greatest strength out of all mechanical splices, meaning they are particularly useful for belts under medium tension that need an extra boost.
What Are The Pros & Cons?
Conveyor belt splicing methods are beneficial in total. However, there are some negatives though – precisely these types take the most time and effort to install because the plates have to be perfectly aligned; it also adds bulk and weight. You would consider using these in situations such as emergency repairs (to get things moving again quickly before making proper fixes); and non-essential jobs where there isn’t lots of stress or wear.
Advantages include how fast they go on—much speedier than vulcanized ones meaning less downtime if something goes wrong with your system plus a lower risk of production delays overall. According to industry research, a skilled operative could fit them in half an hour each! That being said there are downsides too: their connection weakens belts so they will break more easily at this point if pushed too hard; over time materials wear out from use requiring frequent checks/replacements; don’t choose. These are bolted like clamps across two joined belt sections: good when power is needed.
For Mechanical Splice Success, Follow These Guidelines:
With the conveyor belt splicing methods, you can expect optimal performance and efficiency. However, proper preparation of belts is essential for mechanical splices to work well. This involves making sure belt ends are cut cleanly and squared off so they fit together nicely. It’s also important that you follow instructions from the manufacturer–there are different ways to install splices depending on what type you’re using! Using the right tools and fasteners is vital too. Investing in good quality splicing tools will help prevent failures from occurring once your system is up and running; it’ll also mean fewer repairs needed overall.
If you understand both the strengths and weaknesses of these systems, then decisions about when (or when not) use them become much clearer as part of an overall strategy for looking after conveyor belts. Vulcanized joins provide a better solution for high-strength permanent repairs; but more about these next!
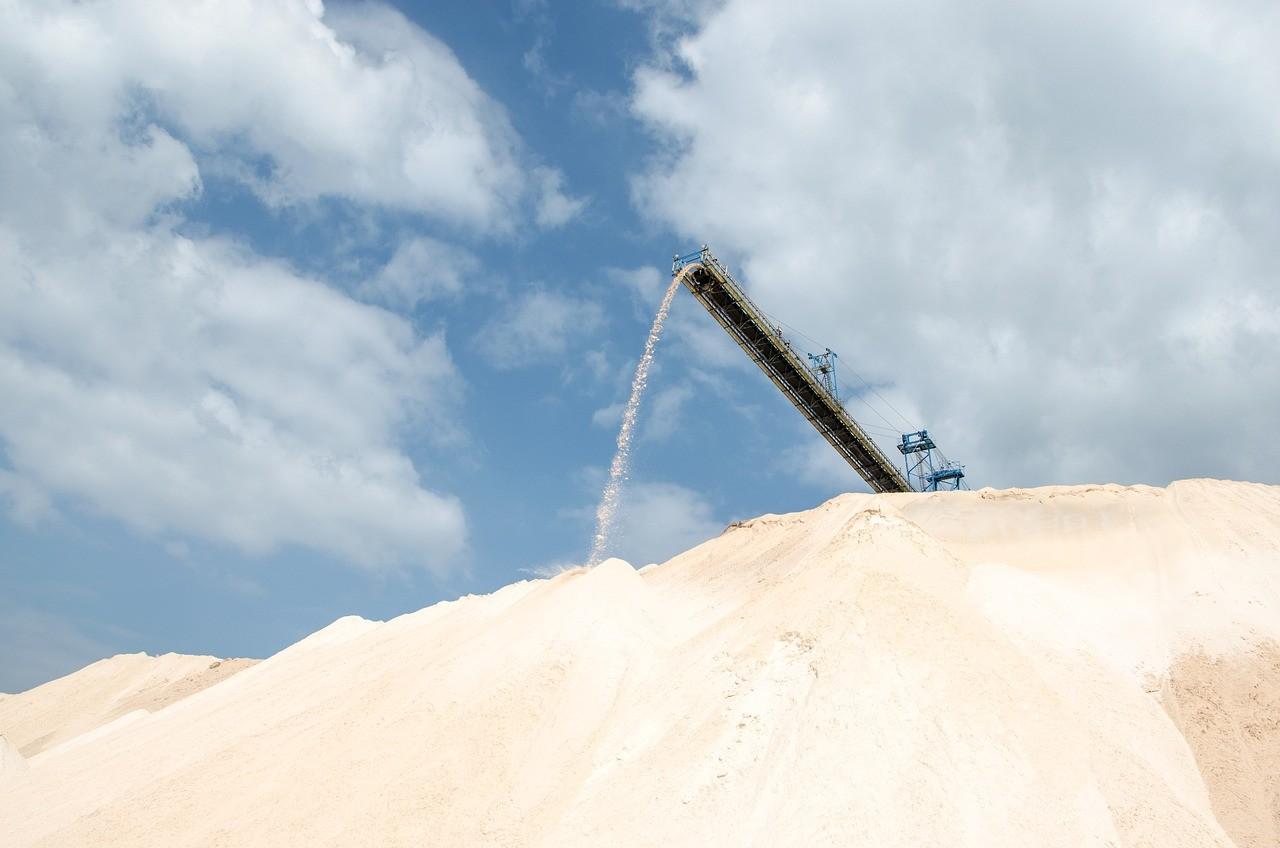
Conveyor Belt Splicing Methods: What Is Vulcanized Splicing?
When it comes to making durable, high-strength connections between conveyor belt sections, vulcanized splicing is hard to beat. Conveyor belt splicing methods are essential to keep everything in order. This vulcanized splicing technique uses heat, pressure and a special type of adhesive to join belt ends together so seamlessly you’d think they were one piece — kind of like welding with computers! A vulcanized splicing multi-step process requiring skill in each step must be done just right for the final product to work properly:
- Preparing Belts: Workers carefully square up roughen aka buff those edges These measures make bonding surfaces uniform, and clean giving the compound the best possible area to adhere to design assembly: Depending upon specifications manufacturer tension rating different designs may be chosen–step finger The selected applied overlapped precisely held in place with clamps.
- Next, Up: Now workers spread specific bonding agents onto newly trimmed areas and surfaces They use rubbery material including curing agents that help the rubber itself harden and pressurize things all components are put into a machine known as a vulcanizer their specialist jargon adds evenly applied heat low several hours at this stage new must form between steel-cord fabric layers many continuous plies
- Advantages Include: Vulcanised joints lots plus points end-users seeking to minimize downtime caused by repairs or replacements needing heavy industries carrying large amounts of raw materials manufactured goods also find them advantageous.
If these facts on conveyor belt splicing methods have whetted your appetite for more details on conveyor belts, why not read our previous comprehensive publishings like Conveyor Belt Maintenance Tips: Revamp Efficiency & Lifespan to explore the best maintenance practices; Industrial Rubber Rollers: Know their Role and Procedures to know the core procedures; or get into the specifics of Roller Alignment: Tips for Extended Conveyor Belt Life and Industrial Roller Hardness: Choosing The Right Shore A so you prepare everything ahead.
Real World Studies
According to studies conducted by the National Mining Association (NMA), vulcanized splices that are done well can withstand forces amounting to 180 percent of what the belt is rated at. One reason for this strength is that vulcanization creates a permanent chemical bond between two materials–in this case, the ends of conveyor belting. Consequently, there is a smaller chance these joins will fail because they become worn down over time; one big plus is fewer repairs in the long run and lower maintenance costs overall. You may indeed have to wait slightly longer for vulcanizing work than if opted for an easier option such as mechanical splicing which tends not to last quite so well once installed: still needing repairs more often and increasing periods when machinery isn’t available for use.
What Are The Downsides?
There are also downsides. For instance, special equipment and training are needed. The need to be patient whilst the job is done (though hurry-up jobs are possible if required) Strength issues reliant on various factors. Selecting an appropriate design for your particular belts plus making sure conditions are right when joining them together chemically are just two things that need careful consideration beforehand. Because if either goes awry then– like any type of bonding exercise–problems could follow shortly afterward!
Importance Of Trained Personnel
It cannot be stressed too greatly how vital it is that any vulcanized splicing work should be carried out solely by fully certificated operatives because there lot involved in the process going wrong really not worth thinking about. With their knowledge and skill, you can trust them to choose the best splicing method for your belt; use only high-quality materials; follow all best practices to a tee–and do it all so there’s minimal risk of early splice failure. Because our experts understand vulcanized splicing inside and out (including how well it works plus any drawbacks), they can help clients incorporate this technique into overall conveyor belt maintenance strategies that pay off over time.
Stay tuned to our news section and our team will be sharing some valuable tools with readers. These will empower you to make smart choices around which splices are right for the job at hand—whatever that may be!
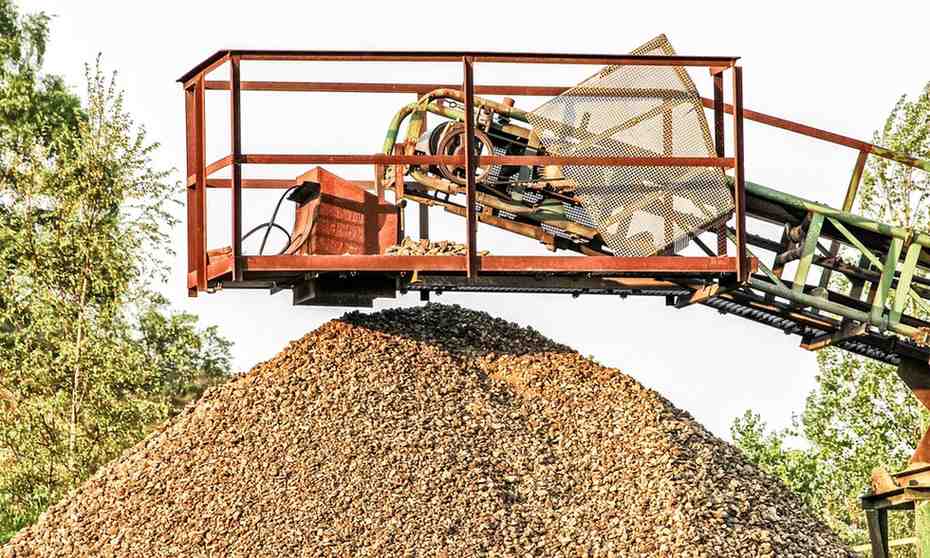
Conveyor Belt Splicing Methods: A Data-Driven Decision Matrix
Selecting the optimal conveyor belt splicing method for your machinery repair is akin to choosing the right tool for the job. A well-informed decision translates to minimized downtime, reduced maintenance costs, and optimal conveyor belt performance. Here’s a comprehensive decision matrix, packed with facts and figures, to guide your selection process:
Factor | Mechanical Splice | Vulcanized Splice |
Belt Type | Most belt types can be used with these fasteners including PVC and those with fabric or lightweight synthetic plies. | Great for high-strength applications with fabric- or steel cord-reinforced belts. Vulcanization has many advantages for steel cord reinforcement; one of the biggest is its impressive capacity to produce an even bond across the entire cord structure. |
Tension Rating | Mechanical splices are suitable for belts with low to medium tensions (usually below 1,800 N/mm). Going over this could mean they fail earlier than expected because they cannot cope with higher pull forces. | Vulcanized splices are recommended for use with high-tension belts (exceeding 1,800 N/mm) and in heavy-duty applications where they will be required to carry heavy loads over long distances. When done correctly, vulcanized splicing may provide nearly the same tensile strength as the original belt–so these products can deliver dependable performance even under tough conditions. Indeed, an international standard suggests that when belts have been vulcanized as per ISO 21186:2004 users might expect up 150% more strength than their rating! |
Application | Use them on belts with low usage or until you can schedule a vulcanized repair. | Vulcanized splices are the number one choice for permanent fixes, critical conveyor systems, and extreme-wear environments where belt strength and durability are top priorities. These splices provide better resistance against fatigue and wear than any other option available – meaning there is less chance of unexpected failures or interruptions to production! |
Repair Needs | They are the obvious choice for making fast repairs during routine maintenance or if you have a breakdown (typically taking less than half an hour to fit by an experienced engineer). | Perfect for creating connections that are both strong and durable, designed to thrive under tough conditions over an extended period of time. Although fitting them takes a while–it can be several hours depending on how thick the belts are and the style of splice you choose–once fitted these robust joints reduce how often repairs are needed. Meaning there is less downtime for maintenance in the future. |
Downtime Constraints | If your main concern is reducing downtime, then a mechanical splice is the quickest way to get your belts up and running again. Just bear in mind they may not go the distance. | When you absolutely must have a repair job that won’t fail, even if it takes a bit longer to put in at first, vulcanized splicing is your best option—it may take longer to install but you’ll make up for that when the splice doesn’t break and shut you down later on! |
Remember: This decision matrix is a valuable tool, but it shouldn’t replace the expertise of a qualified conveyor belt service provider. When faced with a specific repair scenario, don’t hesitate to consult Tehnoguma’s team of experts and get a precise diagnosis for the machinery. They can analyze your unique needs, belt specifications, and operational environment to recommend the most suitable splicing technique, maximizing the efficiency and longevity of your conveyor belt system.
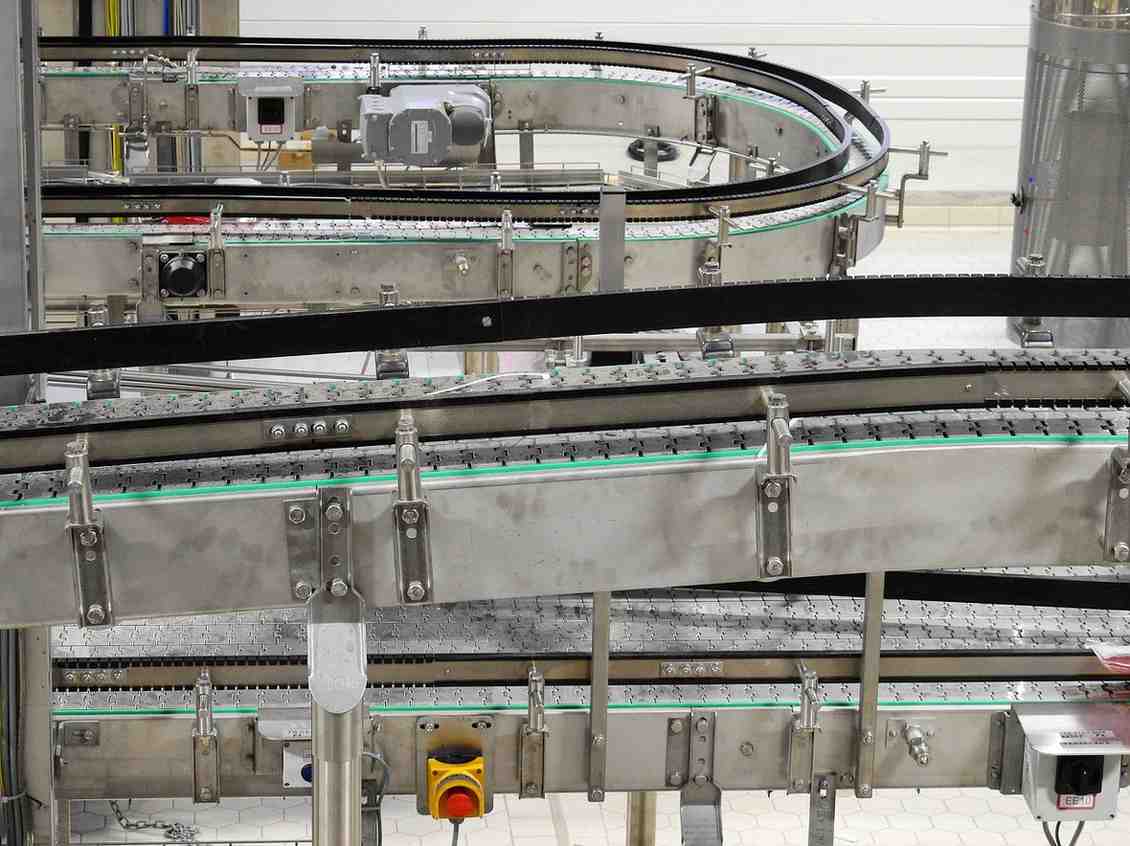
The Chain Reaction of Downtime: Why Proper Splicing Is Vital
In manufacturing’s fast lane, conveyors keep things moving. But if one stops working ─ even temporarily ─ the whole operation can grind to a halt. And that’s bad news for business! Let’s take a look at some numbers that show just how costly downtime from conveyor belt issues can be.
The Cost Of Downtime
A study conducted in 2020 for Manufacturing Engineering Magazine called “The True Cost of Downtime” makes sobering reading: an hour’s unplanned stoppage might set firms back anywhere between $10,000 and $75,000. Such sums illustrate not only the financial pressures faced by companies large and small when belts suddenly cease turning; they also hint at complexities within sectors such as automotive manufacture ─ where an hour-long hiatus along an assembly line could lead to vastly bigger losses than those seen after 60 minutes’ inactivity at a plant producing industrial sand alone. Nor are such impacts limited solely to immediate monetary concerns (though regular readers of this blog will be aware of how keenly we dislike those): because whenever production halts because of malfunctioning machinery there will probably follow costs associated with idle staff plus disgruntled clients who don’t receive orders when expected because something has gone wrong further up-stream–an aside.
The Cost Of Safety
In industries where safety is a top priority–such as mining or petrochemical processing–the repercussions of conveyor belt stoppages are magnified. It’s not just about the financial hit from lost production either; there could be safety hazards too, with dangerous outcomes. Take coal mines as an example. If a conveyor belt were to grind to a halt, then coal dust (which is known to cause respiratory problems) might hang in the air, putting miners’ health at risk.
Or if flammable substances like methane gas build-up because they haven’t been moved along, things could go bang–literally–if someone doesn’t act fast to shift them. Petrochemical firms face similar worries if belts carrying things like toxic chemicals or flammable liquid stop moving: you end up with a ticking time bomb. This is because it’s still possible for leaks or spills to take place, which may then put workers in danger and influence wildlife/ the surrounding landscape.
Such incidents can lead not only to fines being imposed but also to costly clean-up operations, as well as damage your standing within the industry. For tasks that need to be carried out swiftly when machinery has to be taken offline (such as belt repairs), it is therefore vital. Using methods that allow them to do a good job quickly — like modern splicing techniques combined with regular maintenance procedures designed to make wear-&-tear happen more slowly — is essential if such companies want both avoidable risks under control.
Effective Splicing: Your Weapon Against Downtime
If there is one thing companies can count on in the manufacturing industry, it’s that at some point their conveyor belts will break down. When this happens, a lot of time and money is lost–unless businesses have an effective splicing system in place. Splicing refers to the process of joining two pieces of belts together. By choosing the right method (mechanical for fast fixes, vulcanization for a more permanent solution) and making sure it is done properly with high-quality materials, firms can slash repair times and keep their belts running for longer stretches than would otherwise be possible. So it is paramount to have regular checks and implement the best standards to achieve effective splicing results for your machinery.
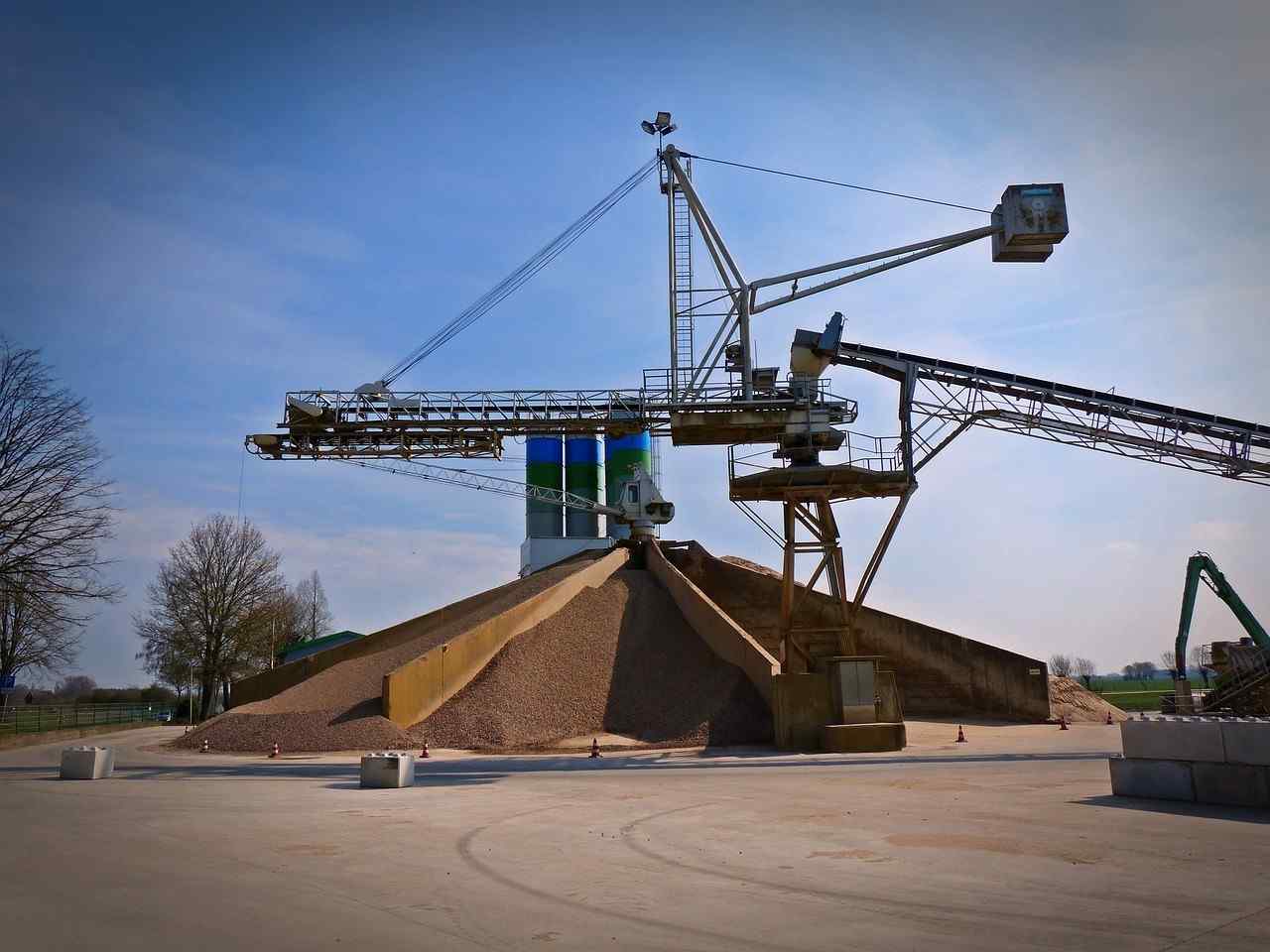
Tehnoguma’s Conveyor Belt Splicing Methods & Service
Tehnoguma specializes in splicing services for conveyor belts. The company’s technicians are skilled in mechanical and vulcanized splicing methods, with expertise in choosing the right technique based on belt type and splicing material. Besides their knowledge, all team members have been certified; this combination allows them not only to make quick repairs when necessary (such as those needed on low-tension belts) but also to create long-lasting splices vital for high-tension applications. To further set itself apart from competitors’ everyday repairs staffed by under-qualified individuals, Tehnoguma has invested heavily in top-of-the-line equipment that enables its crewmembers to work both effectively and efficiently. The results speak volumes, clients experience fewer downtime risk splice failures—two things known disrupt manufacturing schedules bring added costs. Partnering with Tehnoguma can benefit companies in several ways.
Keep Everything Going
For one thing, businesses will not need to shut down their operations as often because these professionals offer such good service; studies have shown that reactive maintenance alone could mean being up 50 percent more hours a year than following proactive programs outlined by experts here. Use their advanced knowledge to recommend the best splicing technique for your specific application and suggest maintenance methods to help you save money in the long term. This proactive approach enhances safety too: maintaining strong, secure conveyor belt connections is crucial in any workplace. Tehnoguma’s expert splicing helps make sure belts don’t fail–keeping your employees safer. Things can go wrong with conveyor belts at any time of day or night. That is why Tehnoguma offers a 24/7 emergency service. Our team will get back to you quickly and is used to dealing with urgent problems such as making sure production lines do not grind to a halt for too long. Do not forget to ask about this if there are things that concern or confuse you. The company also wants clients to know they do not have to put up with frequent breakdowns (when machines stop working).
Get in touch with Tehnoguma now to arrange an appointment slot; during which a member of staff will come round and chat through all the things he can do concerning your needs — starting from saving cash to the best possible solutions for your needs!
Conclusion
Just as a piece of clothing will unravel completely if you don’t repair a small tear promptly, a conveyor belt breakdown can follow from a minor problem with one joint. The stitching together of the two ends is what keeps things moving along nicely–and this stops both delays and expensive periods of downtime for repairs. But (and here’s where it gets really interesting): choosing which type of stitch to use is absolutely vital if further damage to the belt is to be avoided. By having Tehnoguma look after your belts, you can be sure they’ll be in tip-top condition plus there’ll always be someone around who can offer advice on the best kind of splice for any job: how it should be done as well as when it ought not to be tried at all! Their preventive maintenance tips will also help lengthen intervals between checks meaning production lines need stoppages only for routine servicing purposes–until worn parts begin showing signs of giving trouble that is.
So with help from our rubber experts, why not take steps now before things start going wrong? Keep returning to our industrial rubber news section and stay ahead of competitors with the latest advancements and best practices in the domain.